No products
- Airbag Reset
- Acura
- Alfa Romeo
- AUDI
- BMW
- Buick
- Cadillac
- Cherry
- Chevrolet
- Chrysler
- Citroen
- Dacia
- Daewoo
- Daihatsu
- dodge
- Ferrari
- Fiat
- Ford
- GMC
- GREAT WALL MOTORS
- Holden
- Honda
- HUMMER
- Hyundai
- Infiniti
- Isuzu
- Iveco
- Jaguar
- Jeep
- Kia
- Lada
- Lancia
- Land Rover
- Lexus
- Lincoln
- Maserati
- Mazda
- Mercedes Benz
- Mini Cooper
- Mitsubishi
- Nissan
- Opel
- Peugeot
- Pontiac
- Porsche
- Renault
- Rover
- Saab
- Saturn
- Scion
- Seat
- Skoda
- Smart
- Ssang yong
- Subaru
- Suzuki
- Tesla
- Toyota
- Volkswagen
- Volvo
- DTC
- Acura DTC
- B1011
- B1012
- B1013
- B1014
- B1015
- B1016
- B1032
- B1050
- B1051
- B1056
- B1057
- B1060
- B1061
- B1062
- B1063
- B1064
- B1065
- B1066
- B1075
- B1076
- B1077
- B1078
- B1079
- B1080
- B1132
- B1133
- B1134
- B1135
- B1136
- B1147
- B1148
- B1149
- B1150
- B1152
- B1155
- B1156
- B1157
- B1158
- B1159
- B1161
- B1162
- B1166
- B1168
- B1169
- B1170
- B1171
- B1173
- B1175
- B1176
- B1177
- B1178
- B1180
- B1181
- B1182
- B1187
- B1188
- B1189
- B1200
- B1202
- B1205
- B1206
- B1207
- B1208
- B1213
- B1214
- B1215
- B1223
- B1225
- B1226
- B1227
- B1228
- B1229
- B1230
- B1231
- B1232
- B1233
- B1234
- B1235
- B1236
- B1237
- B1238
- B1239
- B1240
- B1241
- B1244
- B1245
- B1246
- B1250
- B1252
- B1255
- B1275
- B1276
- B1277
- B1278
- B1279
- B1280
- B1281
- B1283
- B1284
- B1352
- B1355
- B1356
- B1357
- B1358
- B1359
- B1375
- B1376
- B1377
- B1379
- B1380
- B1381
- B1382
- B1383
- B1384
- B1386
- B1387
- B1388
- B1389
- B1390
- B1575
- B1600
- B1605
- B1750
- B1775
- B1776
- B1779
- B1780
- B1785
- B1786
- B1792
- B1800
- B1802
- B1805
- B1806
- B1808
- B1810
- B1811
- B1812
- B1825
- B1826
- B1827
- B1828
- B1829
- B1835
- B1836
- B1837
- B1840
- B1841
- B1842
- B1843
- B1844
- B1845
- B1846
- B1847
- B1905
- B1906
- B1950
- B1955
- B1956
- B1957
- B1958
- B1959
- B2100
- B2150
- B2152
- B2155
- B2157
- B2160
- B2161
- B2162
- B2175
- B2176
- B2177
- B2178
- B2179
- B2180
- B2181
- B2182
- B2183
- B2184
- B2185
- B2186
- B2187
- B2188
- B2189
- B2190
- B2191
- B2200
- B2202
- B2204
- B2205
- B2206
- B2207
- B2208
- B2209
- B2211
- B2212
- B2240
- B2248
- B2249
- B2965
- B2967
- B2968
- B2969
- B2970
- B2975
- B2976
- B2977
- B2978
- B2979
- B2980
- B2981
- B2982
- B2983
- B2984
- B2985
- B2987
- B2991
- P0010
- P0011
- P0101
- P0102
- P0103
- P0106
- P0107
- P0108
- P0111
- P0112
- P0113
- P0116
- P0118
- P0121
- P0122
- P0123
- P0125
- P0128
- P0131
- P0132
- P0133
- P0134
- P0135
- P0137
- P0138
- P0139
- P0140
- P0141
- P0151
- P0152
- P0153
- P0154
- P0155
- P0157
- P0158
- P0159
- P0160
- P0161
- P0171
- P0172
- P0174
- P0175
- P0201
- P0202
- P0203
- P0204
- P0205
- P0206
- P0218
- P0222
- P0223
- P0300
- P0301
- P0302
- P0303
- P0304
- P0306
- P0325
- P0327
- P0330
- P0335
- P0336
- P0337
- P0339
- P0340
- P0342
- P0344
- P0351
- P0352
- P0354
- P0356
- P0365
- P0385
- P0386
- P0389
- P0401
- P0402
- P0404
- P0405
- P0406
- P0420
- P0430
- P0440
- P0441
- P0442
- P0443
- P0446
- P0451
- P0452
- P0453
- P0455
- P0456
- P0457
- P0461
- P0462
- P0463
- P0480
- P0496
- P0497
- P0498
- P0499
- P050
- P0500
- P0501
- P0502
- P0505
- P0506
- P0507
- P050B
- P0560
- P0562
- P0563
- P060
- P0600
- P0601
- P0602
- P0615
- P0627
- P0630
- P0661
- P0662
- P0685
- P0700
- P0705
- P0706
- P0710
- P0711
- P0712
- P0713
- P0715
- P0716
- P0717
- P0718
- P0719
- P0720
- P0722
- P0723
- P0724
- P0725
- P0730
- P0731
- P0732
- P0733
- P0734
- P0735
- P0740
- P0741
- P0742
- P0745
- P0746
- P0747
- P0748
- P0750
- P0751
- P0752
- P0753
- P0756
- P0757
- P0758
- P0761
- P0762
- P0763
- P0766
- P0767
- P0768
- P0773
- P0775
- P0776
- P0777
- P0778
- P0780
- P0795
- P0796
- P0797
- P0798
- P0812
- P0815
- P0816
- P0840
- P0842
- P0843
- P0845
- P0847
- P0848
- P0872
- P0873
- P0957
- P0958
- P0962
- P0963
- P0966
- P0967
- P0970
- P0971
- P0973
- P0974
- P0976
- P0977
- P0979
- P0980
- P0982
- P0983
- P1077
- P1078
- P1102
- P1103
- P1106
- P1107
- P1108
- P1109
- P1111
- P1112
- P1114
- P1115
- P1116
- P1121
- P1122
- P1128
- P1129
- P1133
- P1134
- P1153
- P1154
- P1162
- P1163
- P1164
- P1166
- P1167
- P1171
- P1172
- P1174
- P1201
- P1202
- P1203
- P1204
- P1205
- P1206
- P1241
- P1242
- P1243
- P1244
- P1246
- P1247
- P1248
- P1259
- P1279
- P1297
- P1298
- P1300
- P1301
- P1302
- P1303
- P1304
- P1305
- P1306
- P1316
- P1317
- P1318
- P1319
- P1336
- P1337
- P1359
- P1361
- P1362
- P1366
- P1367
- P1381
- P1382
- P1386
- P1387
- P1404
- P1441
- P1454
- P1456
- P1457
- P1459
- P145C
- P1486
- P1491
- P1498
- P1508
- P1509
- P1519
- P1549
- P1607
- P1608
- P1618
- P1625
- P1640
- P1650
- P1655
- P1656
- P1658
- P1659
- P1660
- P1671
- P1672
- P1676
- P1677
- P1678
- P1683
- P1684
- P1690
- P1696
- P1697
- P16BB
- P16BC
- P16BD
- P16BE
- P16C0
- P1705
- P1706
- P1709
- P1710
- P1717
- P1738
- P1739
- P1740
- P1743
- P1744
- P1745
- P1750
- P1751
- P1753
- P1758
- P1768
- P1773
- P1778
- P1780
- P1786
- P1787
- P1788
- P1790
- P1791
- P1792E
- P1793
- P1794
- P1795
- P1835
- P1850
- P1860
- P2101
- P2108
- P2118
- P2122
- P2123
- P2127
- P2128
- P2135
- P2138
- P2176
- P2183
- P2184
- P2185
- P2195
- P2197
- P2227
- P2228
- P2229
- P2237
- P2238
- P2240
- P2241
- P2243
- P2245
- P2246
- P2247
- P2249
- P2251
- P2252
- P2254
- P2255
- P2270
- P2271
- P2272
- P2273
- P2279
- P2413
- P2422
- P2552
- P2610
- P2646
- P2647
- P2648
- P2649
- P2A00
- P2A03
- U0028
- U0029
- U0073
- U0104
- U0107
- U0114
- U0122
- U0155
- U0300
- Alfa Romeo DTC
- B0003-01
- B0003-11
- B0003-12
- B0003-1E
- B0004-01
- B0004-11
- B0004-12
- B0004-1E
- B0050-01
- B0050-11
- B0050-12
- B0050-13
- B0050-1D
- B0052-01
- B0052-11
- B0052-12
- B0052-13
- B0052-1D
- B0073-01
- B0073-11
- B0073-12
- B0073-1E
- B0075-01
- B0075-11
- B0075-12
- B0075-1E
- B0080-01
- B0080-11
- B0080-12
- B0080-1E
- B0082-01
- B0082-11
- B0082-12
- B0082-1E
- B0099-68
- B00B5-01
- B00B5-11
- B00B5-12
- B00B5-13
- B00B5-1D
- B00C5-01
- B00C5-11
- B00C5-12
- B00C5-13
- B00C5-1D
- B00D5-12
- B00D5-14
- B00D6-12
- B00D6-14
- B0100-49
- B0101-16
- B0101-17
- B0103-01
- B0103-11
- B0103-12
- B0103-1E
- B0104-01
- B0104-11
- B0104-12
- B0104-1E
- B0105-01
- B0105-11
- B0105-12
- B0105-1E
- B0106-01
- B0106-11
- B0106-12
- B0106-1E
- B0107-01
- B0107-11
- B0107-12
- B0107-1E
- B0108-01
- B0108-11
- B0108-12
- B0108-1E
- B0109-01
- B0109-11
- B0109-12
- B0109-1E
- B010F-01
- B010F-11
- B010F-12
- B010F-1E
- B0110-01
- B0110-11
- B0110-12
- B0110-1E
- B0111-64
- B0112-2F
- B0112-64
- B0112-96
- B0113-01
- B0113-11
- B0113-12
- B0113-1E
- B0114-01
- B0114-11
- B0114-12
- B0114-1E
- B0115-01
- B0115-11
- B0115-12
- B0115-1E
- B0118-95
- B0119-68
- B012-2F
- B012-64
- B012-96
- B0120-68
- B0121-68
- B0122-68
- B0123-01
- B0123-11
- B0123-12
- B0123-1E
- B0124-01
- B0124-11
- B0124-12
- B0124-1E
- B0126-54
- B012B-01
- B012B-11
- B012B-12
- B012B-2F
- B012B-64
- B012B-96
- B012C-2F
- B012C-64
- B012C-96
- B012D-2F
- B012D-64
- B012D-96
- B012F-68
- B0131-68
- B0135-09
- B0135-64
- B100-11
- B100-11
- B100-13
- B100-15
- B100-64
- B100-92
- B1000-01
- B1000-04
- B1000-44
- B1000-45
- B1000-46
- B1000-47
- B1000-96
- B1001-16
- B1001-17
- B1001-21
- B1001-24
- B1001-64
- B1002-21
- B1002-24
- B1002-64
- B1002-68
- B1003-21
- B1003-64
- B1003-86
- B1004-21
- B1004-64
- B1005-21
- B1005-24
- B1005-64
- B1006-11
- B1006-12
- B1006-13
- B1006-21
- B1006-49
- B1006-64
- B1007-11
- B1007-13
- B1007-21
- B1007-54
- B1007-64
- B1008-11
- B1008-13
- B1008-21
- B1008-64
- B100B-11
- B100B-15
- B100B-92
- B100C-11
- B100C-15
- B100C-92
- B100D-11
- B100D-92
- B101-11
- B101-64
- B101-96
- B1010-09
- B1010-62
- B1010-64
- B1010-67
- B1010-71
- B1011-11
- B1011-13
- B1011-15
- B1011-64
- B1012-11
- B1012-13
- B1012-15
- B1013-11
- B1013-13
- B1013-15
- B1013-19
- B1013-62
- B1014-11
- B1014-15
- B1014-86
- B1015-11
- B1015-15
- B1015-23
- B1015-67
- B1016-11
- B1016-15
- B1017-11
- B1017-15
- B1018-11
- B1018-15
- B1019-96
- B101B-11
- B101B-12
- B101B-13
- B101B-15
- B101C-96
- B101D-11
- B101D-15
- B101F-11
- B102-64
- B102-64
- B1020-29
- B1021-01
- B1021-11
- B1021-12
- B1021-13
- B1021-29
- B1022-01
- B1022-11
- B1022-12
- B1022-13
- B1022-1C
- B1023-11
- B1023-12
- B1023-13
- B1024-01
- B1024-11
- B1024-12
- B1024-13
- B1025-01
- B1025-11
- B1025-12
- B1025-13
- B1026-64
- B1027-64
- B1028-64
- B1029-64
- B102C-11
- B102C-13
- B102C-15
- B102C-64
- B102D-11
- B102D-13
- B102D-64
- B102F-64
- B1030-01
- B1030-08
- B1030-64
- B1031-87
- B1032-31
- B1032-87
- B1033-64
- B1034-23
- B1035-01
- B1035-24
- B1035-71
- B1036-12
- B1036-14
- B1039-11
- B1040-11
- B1040-24
- B1040-64
- B1040-86
- B1040-96
- B1041-11
- B1041-16
- B1041-17
- B1041-86
- B1041-96
- B1042-11
- B1042-13
- B1042-24
- B1042-42
- B1043-11
- B1043-13
- B1043-24
- B1043-86
- B1043-96
- B1044-86
- B1045-01
- B1045-11
- B1045-24
- B1045-49
- B1046-01
- B1046-11
- B1046-13
- B1046-15
- B1046-49
- B1047-11
- B1047-13
- B1047-15
- B1048-12
- B1048-14
- B1049-12
- B104B-11
- B104C-11
- B104C-13
- B104D-13
- B104D-71
- B105-64
- B1050-11
- B1050-15
- B1050-65
- B1051-11
- B1051-15
- B1051-55
- B1051-65
- B1052-11
- B1052-12
- B1052-13
- B1052-15
- B1052-65
- B1053-11
- B1053-64
- B1053-65
- B1054-11
- B1054-13
- B1054-62
- B1054-64
- B1054-67
- B1054-86
- B1055-11
- B1055-15
- B1055-23
- B1055-92
- B105B-64
- B105D-64
- B105F-64
- B1060-12
- B1060-14
- B1061-12
- B1061-14
- B1062-11
- B1062-15
- B1062-71
- B1063-11
- B1063-15
- B1064-11
- B1064-15
- B106C-23
- B107-24
- B1070-11
- B1071-11
- B1071-86
- B1072-11
- B1072-71
- B1072-96
- B1072-97
- B1073-71
- B1073-86
- B1073-96
- B1074-62
- B1074-71
- B1074-96
- B1076-11
- B1076-13
- B1078-15
- B107B-11
- B107B-13
- B107C 24
- B107C-23
- B107D-23
- B107D-24
- B107F-24
- B108-11
- B1080-64
- B1080-86
- B1081-86
- B1081-87
- B1082-09
- B1083-23
- B1084-11
- B1084-15
- B1085-18
- B1086-87
- B1087-15
- B1089-11
- B1089-13
- B108C-12
- B108C-14
- B108D-12
- B1091-12
- B1092-12
- B10A-4A
- B10C9-29
- B110-11
- B110-13
- B110-15
- B1100-16
- B1100-68
- B1101-64
- B1102-16
- B1102-17
- B1104-11
- B1104-13
- B1105-11
- B1105-13
- B1106-64
- B1107-11
- B1107-13
- B1108-11
- B1108-13
- B110F-11
- B110F-13
- B110F-15
- B1112-64
- B1116-11
- B1116-13
- B1126-64
- B1161-64
- B1170-01
- B1173-01
- B1174-01
- B1174-86
- B1174-97
- B1175-01
- B1175-86
- B1175-97
- B1176-01
- B1176-86
- B1176-97
- B1177-01
- B1177-86
- B1177-97
- B1265-01
- B1265-68
- B1265-78
- B1265-86
- B1266-11
- B1266-23
- B1267-11
- B1267-15
- B1268-12
- B1268-14
- B1269-11
- B1269-23
- B126A-11
- B126A-23
- B12a-11
- B12a-15
- B12AD-11
- B12AD-15
- B12AD-62
- B12AF-11
- B12AF-15
- B12B0-11
- B12B0-15
- B12B1-11
- B12B1-15
- B12B2-11
- B12D3-12
- B12E3-12
- B140-11
- B140-11
- B140-12
- B140-12
- B140-13
- B140-13
- B140-1A
- B140-92
- B140-92
- B1400-11
- B1400-12
- B1400-13
- B1400-1A
- B1400-92
- B1401-11
- B1401-12
- B1401-13
- B1401-1A
- B1401-92
- B1402-11
- B1402-12
- B1402-13
- B1402-1A
- B1402-92
- B1403-11
- B1403-12
- B1403-13
- B1403-1A
- B1403-92
- B1404-11
- B1404-12
- B1404-13
- B1404-1A
- B1404-92
- B1405-11
- B1405-12
- B1405-13
- B1405-1A
- B1405-92
- B1406-11
- B1406-12
- B1406-13
- B1406-1A
- B1406-92
- B1407-11
- B1407-12
- B1407-13
- B1407-1A
- B1407-92
- B1408-11
- B1408-12
- B1408-13
- B1408-1A
- B1408-49
- B1409-11
- B1409-12
- B1409-13
- B1409-1A
- B1409-92
- B1409-98
- B140B-11
- B140B-12
- B140B-13
- B140B-1A
- B140B-92
- B140C-11
- B140C-1A
- B140C-92
- B140D-11
- B140D-12
- B140D-13
- B140D-1A
- B140D-92
- B1410-16
- B1410-17
- B1411-05
- B1413-05
- B142-4B
- B143-11
- B143-12
- B143-13
- B143D-11
- B143D-12
- B143D-13
- B1552-68
- B1562-11
- B1562-13
- B156B-13
- B156B-1A
- B1570-19
- B1577-13
- B1578-13
- B1578-1A
- B1579-1A
- B157A-13
- B157A-1A
- B1600-01
- B1600-04
- B1600-1C
- B1600-42
- B1600-47
- B1601-04
- B1601-68
- B1602-68
- B1603-68
- B162-11
- B162-11
- B162-13
- B162-13
- B1632-11
- B1632-13
- B1636-11
- B1636-13
- B165A-68
- B1701-11
- B1702-11
- B1711-12
- B1712-12
- B1714-12
- B1715-12
- B1716-12
- B1717-12
- B1718-12
- B1719-12
- B1720-11
- B1720-15
- B1810
- B1811
- B1813
- B1814
- B1885-64
- B1888-09
- B1889-04
- B1889-1F
- B188c-11
- B188c-12
- B188c-13
- B188c-15
- B188c-19
- B188c-31
- B1890-11
- B1890-12
- B1890-13
- B1890-15
- B1890-19
- B1890-31
- B1900-01
- B1901-11
- B1901-15
- B1902-11
- B1902-12
- B1902-77
- B1903-11
- B1903-15
- B1904-11
- B1904-12
- B1904-77
- B1905-11
- B1905-15
- B1906-11
- B1906-12
- B1906-77
- B1907-11
- B1907-15
- B1908-11
- B1908-12
- B1908-77
- B1909-11
- B1909-15
- B1910-11
- B1910-12
- B1910-77
- B1911-11
- B1911-15
- B1912-11
- B1912-12
- B1912-77
- B1913-11
- B1913-15
- B1914-11
- B1914-12
- B1914-77
- B1915-11
- B1915-15
- B1916-11
- B1916-12
- B1916-77
- B1920-11
- B1920-15
- B1921-11
- B1921-15
- B1924-11
- B1924-15
- B1925-11
- B1925-15
- B1926-11
- B1926-15
- B1927-11
- B1927-15
- B1930-11
- B1930-15
- B1931-11
- B1931-15
- B1935-11
- B1935-15
- B1935-96
- B1937-64
- B1938-64
- B1938-96
- B1939-64
- B1939-96
- B1940-16
- B1940-17
- B1941-11
- B1941-15
- B1942-11
- B1942-15
- B1943-11
- B1943-15
- B1945-11
- B1945-15
- B1947-42
- B1948-49
- B1949-12
- B1949-2A
- B1954-02
- B1954-93
- B1968-92
- B196B-92
- B197f-02
- B197f-12
- B1A7D-23
- B1B50
- B1B51
- B1EB1-29
- B1EB2-29
- B210-16
- B210B-17
- B2199-16
- B2199-17
- B2199-62
- B2206-00
- B221E-00
- B222C-00
- B224-45
- B244E-44
- B25C7
- B25C8
- B2734-01
- B2734-12
- B2734-13
- B2761-01
- B2761-11
- B2761-12
- B2764-01
- B2764-11
- B2764-12
- B3901-00
- B3905-31
- C0010-01
- C0011-01
- C0014-01
- C0015-01
- C0018-01
- C0019-01
- C001C-01
- C001D-01
- C0021-93
- C003-01
- C003-29
- C003-4A
- C003-64
- C003-85
- C0030-29
- C0031-01
- C0031-29
- C0031-4A
- C0031-64
- C0031-85
- C0033-29
- C0034-01
- C0034-29
- C0034-4A
- C0034-64
- C0034-85
- C0036-29
- C0037-01
- C0037-29
- C0037-4A
- C0037-64
- C0037-85
- C0039-29
- C0046-01
- C0046-25
- C0046-26
- C0046-27
- C0046-54
- C0046-64
- C0046-96
- C0049-01
- C0049-7A
- C0049-7b
- C0051-27
- C0051-29
- C0051-54
- C0051-64
- C0051-84
- C0051-85
- C0051-86
- C0061-01
- C0061-09
- C0061-54
- C0061-64
- C0061-95
- C0062-01
- C0062-09
- C0062-54
- C0062-64
- C0062-76
- C0063-01
- C0063-09
- C0063-64
- C006C-64
- C0075-01
- C0082-04
- C0501
- C0507
- C050D
- C0513
- C051C
- C0608
- C100-11
- C100-12
- C100-14
- C100-15
- C100-29
- C1000-16
- C1000-17
- C1000-44
- C1000-45
- C1000-46
- C1000-47
- C1000-68
- C1000-98
- C1001-12
- C1001-14
- C1001-29
- C1001-35
- C1002-02
- C1002-12
- C1002-14
- C1002-25
- C1002-29
- C1002-54
- C1002-68
- C1003-04
- C1003-12
- C1003-14
- C1003-18
- C1003-19
- C1003-29
- C1003-49
- C1003-86
- C1003-97
- C1004-12
- C1004-14
- C1004-16
- C1004-17
- C1004-29
- C1004-51
- C1005-02
- C1005-11
- C1005-12
- C1005-13
- C1006-11
- C1006-12
- C1006-13
- C1006-64
- C1007-54
- C1007-64
- C1008-54
- C1008-64
- C1009-09
- C100B-11
- C100B-12
- C100B-14
- C100B-15
- C100B-29
- C100C-12
- C100C-14
- C100C-29
- C100D-12
- C100D-14
- C100D-29
- C100F-87
- C1011-87
- C1017-1C
- C1018-68
- C1020-68
- C104-02
- C104-04
- C104-11
- C104-12
- C104-13
- C104-1D
- C104-29
- C104-49
- C104-4B
- C104-74
- C104-76
- C104-77
- C104-84
- C104-85
- C104-92
- C104-95
- C1048-01
- C1048-25
- C1048-26
- C1048-27
- C1048-92
- C1048-96
- C1049-01
- C1049-62
- C1049-96
- C104B-11
- C104B-12
- C104B-13
- C104B-79
- C104B-7A
- C104B-92
- C104C-11
- C104C-12
- C104C-13
- C104C-98
- C104D-11
- C104D-12
- C104D-13
- C104D-7A
- C104F-64
- C105B-64
- C105C-64
- C105D-8F
- C106D-11
- C106D-12
- C106D-13
- C1200-13
- C1200-16
- C1200-17
- C1200-19
- C1200-1C
- C1200-49
- C1201-02
- C1202-02
- C1203-16
- C1203-17
- C1203-54
- C1204-01
- C1204-49
- C1205-49
- C1205-54
- C1206-77
- C1207-68
- C1208-13
- C1209-68
- C120B-62
- C1211-05
- C1211-22
- C1211-44
- C1211-45
- C1211-48
- C1211-49
- C1211-4B
- C1211-94
- C1212-49
- C1212-4B
- C1212-94
- C1213-51
- C1213-55
- C1213-56
- C1217-29
- C1220-86
- C1221-86
- C1224-86
- C1240-86
- C1300-00
- C1300-16
- C1300-17
- C1300-48
- C1300-53
- C1301-4B
- C1301-93
- C1301-94
- C1302-78
- C1303-94
- C1304-55
- C1305-09
- C1306-09
- C1307-09
- C1308-68
- C1309-68
- C140-55
- C1400-01
- C1400-02
- C1400-12
- C1400-13
- C1400-86
- C1400-97
- C1401-77
- C1401-86
- C1401-94
- C1402-12
- C1402-14
- C1402-4B
- C1402-86
- C1403-01
- C1403-13
- C1403-19
- C1403-1B
- C1403-1D
- C1403-71
- C1403-86
- C1403-92
- C1403-93
- C1404-86
- C1405-01
- C1405-13
- C1405-19
- C1405-1B
- C1405-1D
- C1405-71
- C1405-86
- C1405-92
- C1405-93
- C1406-86
- C1407-01
- C1407-13
- C1407-1D
- C1407-86
- C1408-86
- C1409-01
- C1409-13
- C1409-1D
- C1409-97
- C140B-05
- C140B-49
- C140B-94
- C140C-86
- C140D-86
- C141-49
- C141-64
- C1410-87
- C1411-49
- C1412-54
- C1413-86
- C1413-87
- C1414-87
- C1415-53
- C1416-51
- C1416-87
- C1416-95
- C1417-78
- C1418-78
- C1419-64
- C141B-97
- C141C-86
- C141d-47
- C141F-96
- C1420-25
- C1420-66
- C1421-64
- C1422-49
- C1422-66
- C1423-4B
- C1424-4B
- C1425-45
- C1426-49
- C1428-68
- C1429-66
- C1429-68
- C1430-86
- C1431-86
- C1432-86
- C1433-86
- C1434-86
- C1435-87
- C1436-86
- C1438-86
- C1439-86
- C1443-87
- C1445-87
- C1446-86
- C144A-86
- C144B-24
- C144D-86
- C144F-86
- C1450-86
- C1451-86
- C1452-86
- C1453-86
- C14A5-97
- C14AA-68
- C1500-77
- C1500-93
- C1501-07
- C1501-16
- C1501-77
- C1501-93
- C1502-07
- C1502-16
- C1502-53
- C1502-68
- C1503-07
- C1503-16
- C1503-9A
- C1504-07
- C1504-16
- C1510-54
- C1512-88
- C1597-53
- C15CB-51
- C1999-86
- C2000-64
- C2002-64
- C2006-16
- C2006-17
- C201-19
- C201-1D
- C2010-16
- C2010-17
- C2010-64
- C2011-16
- C2011-17
- C2012-68
- C2013-4B
- C2014-68
- C2015-68
- C2016-68
- C2017-68
- C2018-68
- C2019-92
- C201B-1D
- C201C-64
- C201D-68
- C201F-68
- C2020-68
- C2021-68
- C2030-11
- C2030-12
- C2031-62
- C2032-64
- C2040-55
- C2041-68
- C2042-64
- C2043-62
- C2044-64
- C2046-64
- C2047-92
- C2048-64
- C2049-64
- C205-68
- C2051-68
- C2052-68
- C2053-68
- C2054-68
- C2055-68
- C2056-68
- C2057-68
- C2058-68
- C2059-64
- C207-64
- C207-68
- C2070-68
- C2071-68
- C2072-68
- C2073-68
- C2074-68
- C2075-68
- C2076-68
- C2077-16
- C2077-17
- C2078-68
- C2079-68
- C207B-68
- C207C-68
- C207D-68
- C207F-68
- C2080-68
- C2090-4B
- C2091-01
- C2100-68
- C2101-68
- C2102-68
- C2110-68
- C2111-68
- C2112-68
- C2117-84
- C2118-84
- C2121-01
- C2130-42
- C2131-42
- C2132-42
- C2140-16
- C2140-17
- C2150-68
- C220-68
- C220-68
- C2200-64
- C2201-68
- C2202-68
- C2204-68
- C2205-98
- C2206-68
- C2207-68
- C2208-68
- C2209-68
- C220B-68
- C220C-68
- C220D-68
- C220F-68
- C2210-4B
- C2210-68
- C2210-86
- C2230-68
- C2231-68
- C2232-68
- C2233-68
- C2240-68
- C2241-68
- C250-16
- C250-17
- C2500-09
- C2500-11
- C2500-12
- C2500-13
- C2501-09
- C2501-11
- C2501-12
- C2501-13
- C2502-02
- C2502-29
- C2502-96
- C2503-09
- C2503-11
- C2503-12
- C2503-13
- C2504-09
- C2504-11
- C2504-12
- C2504-13
- C2505-02
- C2505-29
- C2505-96
- C2506-02
- C2506-29
- C2506-96
- C2507-02
- C2507-29
- C2507-96
- C2508-02
- C2508-29
- C2508-96
- C2509-02
- C2509-29
- C2509-96
- C250F-16
- C250F-17
- C251-02
- C251-29
- C251-96
- C2510-14
- C2510-19
- C2510-77
- C2510-98
- C2511-14
- C2511-19
- C2511-77
- C2511-98
- C2512-14
- C2512-19
- C2512-77
- C2512-98
- C2513-14
- C2513-19
- C2513-77
- C2513-98
- C2518-02
- C2518-29
- C2518-96
- C2519-02
- C2519-29
- C2519-96
- C251B-62
- C251C-62
- C251D-62
- C254D-44
- C254D-45
- C254D-46
- C254D-47
- C254D-48
- C254D-92
- C254D-96
- C2558-27
- C2558-29
- C2565-27
- C2565-29
- C2566-54
- C2567-55
- C256E-27
- C256E-29
- C257-27
- C257-27
- C257-29
- C257-29
- C2577-27
- C2577-29
- C2578-27
- C2578-29
- C2579-27
- C2579-29
- C257B-27
- C257B-29
- C257C-27
- C257C-29
- C257D-27
- C257D-29
- C257F-27
- C257F-29
- C2590-27
- C2590-29
- C2591-27
- C2591-29
- C2600-64
- C2601-04
- C2601-27
- C2602-16
- C2602-17
- C2602-54
- C2605-11
- C2605-15
- C2608-11
- C2608-15
- C260B-11
- C260B-12
- C260D-11
- C260D-12
- C261-11
- C261-15
- C2610-64
- C2610-65
- C2614-64
- C2614-65
- C2617-11
- C2617-15
- C261D-11
- C261D-12
- C261D-13
- C2620-64
- C2626-11
- C2626-12
- C2626-13
- C2629-64
- C2633-68
- C2652-81
- C2654-81
- C2657-68
- C2658-68
- C2659-07
- C265A-07
- C266-4B
- C266C-4B
- C266D-4B
- C266F-4B
- C2670-4B
- C2671-4B
- C2672-4B
- C2673-4B
- P0001
- P0002
- P0003
- P0004
- P0016
- P0030
- P0031
- P0032
- P0033
- P0034
- P0035
- P0036
- P0037
- P0038
- P0039
- P0054
- P0071
- P0072
- P0073
- P007B
- P007C
- P007D
- P0087
- P0088
- P008A
- P008B
- P0096
- P0097
- P0098
- P00B7
- P00D2
- P00DF
- P00E0
- P00E1
- P00F3
- P00F4
- P00F5
- P0100
- P0101
- P0102
- P0103
- P0106
- P0107
- P0108
- P0111
- P0112
- P0113
- P0116
- P0117
- P0118
- P0122
- P0123
- P0128
- P0131
- P0132
- P0133
- P0135
- P0136
- P0137
- P0138
- P0139
- P013A
- P013B
- P015A
- P015B
- P0171
- P0172
- P0182
- P0183
- P018B
- P018C
- P018D
- P0191
- P0192
- P0193
- P0196
- P0197
- P0198
- P0199
- P01BA
- P01BB
- P01BC
- P01C0
- P01C1
- P0201
- P0202
- P0203
- P0204
- P0219
- P0222
- P0223
- P022B
- P022C
- P023
- P0234
- P0236
- P0237
- P0238
- P023B
- P023C
- P024
- P0243
- P0244
- P0245
- P0246
- P024B
- P0261
- P0262
- P0264
- P0265
- P0267
- P0268
- P026A
- P026E
- P0270
- P0300
- P0301
- P0302
- P0303
- P0304
- P0325
- P0326
- P0327
- P0328
- P0330
- P0331
- P0332
- P0333
- P0363
- P0401
- P0402
- P0403
- P0404
- P0405
- P0406
- P040B
- P040C
- P040D
- P0420
- P0489
- P0490
- P04DB
- P053F
- P0560
- P0560-1C
- P0562-16
- P0563-17
- P0578
- P058C
- P05E4
- P05E5
- P05E6
- P0601
- P0606-42
- P0607-48
- P0914-81
- P0919-81
- P107F
- P110
- P110
- P110B
- P110F
- P1128
- P1188
- P1189
- P118B
- P118C
- P1190
- P1300
- P149A
- P1515
- P152
- P152D
- P152F
- P1607
- P16A1
- P16A2
- P16A3
- P16A4
- P16A5
- P1C72-09
- P1C72-24
- P1C74-09
- P1C75-24
- P1C76-24
- P1C77-16
- P1C77-17
- P1C78-16
- P1C78-17
- P1C79-18
- P1C79-19
- P1C7A-09
- P1CEA
- P1CF3
- P1CF4
- P1D7F
- P1DD0
- P1DD2
- P1E2B
- P1E2C
- P1E5B
- P1E5C
- P1E5F
- P1E60
- P2066
- P2067
- P2068
- P2096
- P2097
- P2100
- P2101
- P2102
- P2103
- P2135
- P2173
- P2175
- P2183
- P2184
- P2185
- P219C
- P219D
- P219E
- P219F
- P2227
- P2229
- P2237
- P2238
- P2239
- P2243
- P2244
- P2245
- P2246
- P2251
- P2252
- P2253
- P2262
- P2299
- P2305
- P2311
- P2422
- P24D6
- P2510
- P254F
- P257E
- P257F
- P2610
- P2626
- P2627
- P2628
- P2682
- P2683
- P26A3
- P26AB
- P26B1
- P26E4
- P26E5
- P26E6
- P26F0
- P26F2
- P2ABF
- P2AC0
- P2AC1
- P2AC2
- P2AE0
- P2AE1
- P2AE2
- P2AE3
- P2AE4
- P2AE5
- P2AE6
- P2AE7
- P2AE8
- P2B2F
- P2B81
- P2B89
- P2B8A
- P2B8C
- P2B8D
- P302C
- P302D
- P3053
- U0001-87
- U0001-88
- U0001-96
- U0010-31
- U0010-87
- U0010-88
- U0100-87
- U0101-87
- U0121-86
- U0121-87
- U0122-86
- U0122-87
- U0129-87
- U0131-87
- U0140-86
- U0140-87
- U0140-8F
- U0155-87
- U0155-8F
- U0184-87
- U0186-31
- U0198-86
- U0198-87
- U0208-87
- U0247-86
- U0247-87
- U0254-87
- U02A9
- U0331
- U0401-86
- U0402-86
- U0416-86
- U0418-86
- U0418-96
- U0419-96
- U0420-86
- U0422-86
- U0423-86
- U0426-31
- U0426-62
- U0426-64
- U0426-87
- U0427-64
- U0427-87
- U0428-86
- U0433-64
- U0433-87
- U0434-64
- U0435-64
- U05AA
- U0809-29
- U1001-08
- U1001-86
- U1001-87
- U1001-88
- U1008-08
- U1010-88
- U110C
- U11E3
- U1200-08
- U1200-88
- U1201-86
- U1201-87
- U1202-86
- U1202-87
- U1301-49
- U1302-49
- U1411-09
- U1411-29
- U1411-87
- U1412-09
- U1412-87
- U1413-09
- U1413-87
- U1414-09
- U1414-52
- U1414-87
- U1415-09
- U1416-29
- U1417-09
- U1421-87
- U1422-87
- U1423-87
- U1424-87
- U1425-87
- U1426-87
- U1446-87
- U1451-87
- U1459-83
- U1459-87
- U145E-87
- U1460-64
- U146D-64
- U147d-64
- U148d-64
- U149D-64
- U1700-29
- U1700-35
- U1700-86
- U1700-87
- U1700-8F
- U1701-67
- U1701-86
- U1701-87
- U1701-8F
- U1702-54
- U1702-86
- U1702-87
- U1703-86
- U1703-87
- U1703-8F
- U1704-87
- U1706-29
- U1706-86
- U1706-87
- U1707-87
- U1708-87
- U170B-86
- U170B-87
- U1710-86
- U1710-87
- U1711-2F
- U1711-86
- U1711-87
- U1712-2F
- U1713-2F
- U1714-2F
- U1715-2F
- U1716-2F
- U171A-86
- U171A-87
- U1722-87
- U1724-64
- U1724-86
- U1724-87
- U1726-86
- U1726-87
- U1727-09
- U1728-09
- U1730-86
- U1730-87
- U1736-86
- U1736-87
- U1737-87
- U173F-29
- U173F-86
- U173F-87
- U1741-86
- U1741-87
- U1746-86
- U1746-87
- U1751-86
- U1751-87
- U1752-86
- U1752-87
- U1757-86
- U1757-87
- U1763-86
- U1763-87
- U1765-86
- U1765-87
- U1765-8F
- U1766-86
- U1766-87
- U1766-8F
- U1767-86
- U1767-87
- U1768-86
- U1768-87
- U1769-86
- U1769-87
- U176C-86
- U176C-87
- U1770-87
- U1772-87
- U1801-08
- U1802-08
- U1803-08
- U1804-08
- U1930-29
- U1930-86
- U1931-86
- U1931-87
- U1932-29
- U1932-86
- U1932-87
- U1933-86
- U1933-87
- U1934-87
- U1950-83
- U1952-83
- U1953-83
- U1954-83
- U1956-83
- U1958-83
- U195A-83
- U195C-83
- U195E-83
- U1960-83
- U1962-83
- U1964-83
- U1966-83
- U196A-83
- U196E-83
- U1970-83
- U1972-83
- U1978-83
- U197A-83
- U197C-67
- U197C-83
- U1981-83
- U1982-83
- U1983-83
- U1984-83
- U1985-83
- U1986-83
- U198A-83
- U1990-83
- U1992-83
- U19B0-83
- U1A01-87
- U1A05-86
- U1A05-87
- U1A06-86
- U1A06-87
- U1A07-86
- U1A07-87
- U1A08-86
- U1A08-87
- U1A09-83
- U1A10-83
- U1A10-86
- U1A10-87
- U1A15-83
- U1A16-83
- U1A16-87
- U1A17-86
- U1A17-87
- U1A1A-86
- U1A1A-87
- U1A50-64
- U1A55-01
- U1A55-87
- U1A56-01
- U1A56-86
- U1A56-87
- U2001-87
- U2002-87
- U2003-87
- U2004-87
- U2005-87
- U2006-64
- U2006-87
- U2007-64
- U2008-64
- U2009-64
- U2010-64
- U2011-64
- U2012-64
- U2013-64
- U2014-64
- U2015-64
- U2016-64
- U2017-64
- U2018-64
- U2019-64
- U2020-87
- U2021-87
- U2022-64
- U2023-87
- U2024-87
- U2025-87
- U2026-87
- U2027-64
- U2028-64
- U202A-87
- U202B-87
- U202C-87
- U2051-87
- U2052-87
- U2053-87
- U2054-87
- U2055-87
- U2056-87
- U2057-87
- U2058-87
- U2059-87
- U2061-67
- U2061-87
- U2062-87
- U2063-87
- U2064-87
- U2065-87
- U2066-87
- U2067-87
- U2068-87
- U2069-87
- U2070-87
- U2071-67
- U2072-64
- U2073-64
- U2081-87
- U2082-87
- U2083-64
- U2083-87
- U2084-87
- U2085-64
- U2086-64
- U2086-87
- U2090-64
- U2700-86
- U2700-87
- U2706-86
- U2706-87
- U3002-4A
- U3002-87
- Audi DTC
- P000
- P000B
- P000C
- P000D
- P0010
- P0011
- P0012
- P0013
- P0014
- P0015
- P0016
- P0017
- P0018
- P0019
- P0020
- P0021
- P0022
- P0023
- P0024
- P0025
- P0030
- P0031
- P0032
- P0036
- P0037
- P0038
- P0040
- P0041
- P0042
- P0043
- P0044
- P0045
- P0047
- P0048
- P0050
- P0051
- P0052
- P0056
- P0057
- P0058
- P0068
- P0070
- P0071
- P0072
- P0073
- P0087
- P0088
- P0089
- P0090
- P0092
- P0097
- P0098
- P00AF
- P00D1
- P00D2
- P00D5
- P010
- P0100
- P0101
- P0102
- P0103
- P0105
- P0106
- P0107
- P0108
- P010B
- P010C
- P010D
- P0111
- P0112
- P0113
- P0116
- P0117
- P0120
- P0121
- P0122
- P0123
- P0128
- P012B
- P0130
- P0131
- P0132
- P0133
- P0134
- P0135
- P0136
- P0137
- P0138
- P0139
- P0140
- P0141
- P0142
- P0143
- P0144
- P0145
- P0146
- P0147
- P0150
- P0151
- P0152
- P0153
- P0154
- P0155
- P0156
- P0157
- P0158
- P0159
- P0160
- P0161
- P0169
- P0170
- P0171
- P0172
- P0173
- P0174
- P0175
- P0181
- P0190
- P0191
- P0192
- P020
- P0201
- P0202
- P0203
- P0204
- P0205
- P0206
- P0207
- P0208
- P0209
- P020B
- P020C
- P020D
- P0210
- P0219
- P0221
- P0222
- P0223
- P0225
- P0226
- P0228
- P0230
- P0234
- P0235
- P0236
- P0237
- P0238
- P0240
- P0243
- P0245
- P0246
- P025
- P025C
- P025D
- P0261
- P0262
- P0263
- P0264
- P0265
- P0266
- P0267
- P0268
- P0269
- P0270
- P0271
- P0272
- P0273
- P0274
- P0276
- P0277
- P0279
- P0280
- P0282
- P0283
- P0285
- P0286
- P0288
- P0289
- P0290
- P0299
- P0300
- P0301
- P0302
- P0303
- P0304
- P0305
- P0306
- P0307
- P0308
- P0309
- P0310
- P0318
- P0321
- P0324
- P0325
- P0326
- P0327
- P0328
- P0331
- P0332
- P0333
- P0335
- P0336
- P0340
- P0341
- P0342
- P0343
- P0346
- P0351
- P0352
- P0353
- P0355
- P0356
- P0357
- P0358
- P0359
- P0366
- P0367
- P0368
- P0381
- P0383
- P0401
- P0402
- P0405
- P0406
- P040B
- P040C
- P040D
- P0411
- P0412
- P0413
- P0414
- P0415
- P0416
- P0417
- P0418
- P0419
- P0420
- P0421
- P0422
- P0430
- P0431
- P0440
- P0441
- P0442
- P0443
- P0444
- P0445
- P0449
- P0455
- P0456
- P0458
- P0459
- P045E
- P045F
- P0471
- P047F
- P0480
- P0481
- P048A
- P048C
- P0491
- P0492
- P0498
- P0499
- P050
- P0501
- P0503
- P0506
- P0507
- P050B
- P0510
- P052A
- P052C
- P053F
- P0544
- P0545
- P054A
- P054C
- P0560
- P0562
- P0563
- P0571
- P0600
- P0601
- P0602
- P0604
- P0605
- P0606
- P0607
- P0608
- P0613
- P0614
- P0627
- P0628
- P0629
- P062B
- P0638
- P0641
- P0659
- P066A
- P066C
- P066E
- P0670
- P0671
- P0672
- P0673
- P0674
- P067A
- P0684
- P0685
- P0686
- P0687
- P0688
- P0691
- P0692
- P0697
- P0698
- P0699
- P0702
- P0704
- P0705
- P0706
- P0707
- P0708
- P0710
- P0711
- P0712
- P0713
- P0714
- P0715
- P0716
- P0717
- P0720
- P0721
- P0722
- P0725
- P0726
- P0727
- P0729
- P0730
- P0731
- P0732
- P0733
- P0734
- P0735
- P0736
- P0740
- P0741
- P0746
- P0747
- P0748
- P0751
- P0752
- P0753
- P0754
- P0756
- P0757
- P0758
- P0761
- P0762
- P0763
- P0766
- P0768
- P0771
- P0773
- P0776
- P0777
- P0778
- P0781
- P0782
- P0783
- P0784
- P0785
- P0796
- P0797
- P0798
- P0805
- P0807
- P0808
- P0810
- P0811
- P0829
- P0840
- P0841
- P0842
- P0843
- P0845
- P0846
- P0863
- P0864
- P0865
- P0889
- P0890
- P0891
- P0892
- P0914
- P0919
- P0929
- P0944
- P0945
- P0947
- P0948
- P1004
- P1005
- P1006
- P1007
- P1009
- P100F
- P10A0
- P10A4
- P1103
- P1105
- P1107
- P1110
- P1111
- P1112
- P1113
- P1114
- P1115
- P1116
- P1117
- P1118
- P1127
- P1128
- P1129
- P1130
- P1136
- P1137
- P1138
- P1139
- P1141
- P1143
- P1146
- P1149
- P1160
- P1161
- P1171
- P1172
- P1173
- P1176
- P1177
- P117A
- P117C
- P117D
- P117E
- P117F
- P1196
- P1197
- P1198
- P1199
- P1201
- P1202
- P1203
- P1204
- p1213
- P1214
- P1215
- P1216
- P1217
- P1218
- P1225
- P1226
- P1227
- P1228
- P1229
- P1230
- P1237
- P1238
- P1239
- P1240
- P1241
- P1242
- P1250
- P1255
- P1256
- P1287
- P1288
- P1289
- P1295
- P1296
- P1297
- P129B
- P129C
- P129D
- P12A1
- P12A2
- P12A4
- P12A5
- P12A6
- P12A7
- P1300
- P1325
- P1326
- P1328
- P1329
- P1330
- P1335
- P1336
- P1337
- P1338
- P1340
- P1341
- P1343
- P1345
- P1355
- P1356
- P1357
- P1358
- P1359
- P1360
- P1361
- P1362
- P1363
- P1364
- P1365
- P1366
- P1386
- P1387
- P1388
- P1391
- P1392
- P1393
- P1394
- P1395
- P1398
- P13CE
- P13CF
- P13D1
- P13D2
- P13D3
- P13D4
- P13D5
- P13D6
- P13D7
- P13D8
- P13D9
- P13EA
- P1409
- P140C
- P1410
- P1420
- P1421
- P1422
- P1424
- P1425
- P1426
- P1432
- P1433
- P1434
- P1435
- P1436
- P1470
- P1471
- P1472
- P1473
- P1475
- P1476
- P1477
- P1478
- P1489
- P1490
- P1491
- P1494
- P1497
- P1498
- P150
- P1500
- P1501
- P1502
- P1512
- P1515
- P1516
- P1517
- P1519
- P1522
- P1529
- P1530
- P1531
- P1541
- P1542
- P1543
- P1544
- P1545
- P1546
- P1547
- P1548
- P1550
- P1555
- P1556
- P1557
- P1558
- P1559
- P1560
- P1564
- P1565
- P1568
- P1580
- P1582
- P1602
- P1603
- P1604
- P1606
- P1609
- P1610
- P1611
- P1612
- P1613
- P1624
- P1626
- P1630
- P1631
- P1633
- P1634
- P1639
- P1640
- P1648
- P1649
- P1650
- P1654
- P1676
- P1677
- P1681
- P1690
- P1691
- P1692
- P1693
- P1702
- P172
- P1750
- P1757
- P1778
- P1780
- P17A8
- P17A9
- P17AA
- P17AB
- P17AC
- P17AD
- P17AE
- P17AF
- P17B0
- P17B1
- P17B2
- P17B3
- P17B8
- P17B9
- P17BA
- P17BB
- P17BC
- P17BD
- BMW DTC
- P0010
- P0011
- P0012
- P0013
- P0014
- P0015
- P0016
- P0017
- P0018
- P0019
- P0020
- P0021
- P0022
- P0023
- P0024
- P0025
- P0030
- P0031
- P0032
- P0036
- P0037
- P0038
- P0040
- P0050
- P0051
- P0052
- P0056
- P0057
- P0058
- P0070
- P0071
- P0100
- P0101
- P0102
- P0103
- P0111
- P0112
- P0113
- P0116
- P0117
- P0118
- P0119
- P0120
- P0121
- P0122
- P0123
- P0125
- P0128
- P0130
- P0131
- P0132
- P0133
- P0134
- P0135
- P0136
- P0137
- P0138
- P0139
- P0140
- P0141
- P0150
- P0151
- P0152
- P0153
- P0154
- P0155
- P0156
- P0157
- P0158
- P0159
- P0160
- P0161
- P0170
- P0171
- P0172
- P0173
- P0174
- P0175
- P0201
- P0202
- P0203
- P0204
- P0205
- P0206
- P0207
- P0208
- P0221
- P0222
- P0223
- P0261
- P0262
- P0264
- P0265
- P0267
- P0268
- P0270
- P0271
- P0273
- P0274
- P0276
- P0277
- P0279
- P0280
- P0282
- P0283
- P0298
- P0300
- P0301
- P0302
- P0303
- P0304
- P0305
- P0306
- P0307
- P0308
- P0313
- P0324
- P0325
- P0327
- P0328
- P0330
- P0332
- P0333
- P0335
- P0336
- P0339
- P0340
- P0341
- P0342
- P0343
- P0344
- P0345
- P0346
- P0347
- P0348
- P0351
- P0353
- P0354
- P0355
- P0356
- P0357
- P0358
- P0365
- P0366
- P0367
- P0368
- P0369
- P0370
- P0372
- P0373
- P0385
- P0390
- P0391
- P0392
- P0393
- P0394
- P0411
- P0412
- P0413
- P0414
- P0418
- P0420
- P0430
- P0440
- P0441
- P0442
- P0443
- P0444
- P0445
- P0446
- P0450
- P0451
- P0452
- P0453
- P0455
- P0456
- P0458
- P0459
- P0460
- P0461
- P0462
- P0463
- P0477
- P0478
- P0479
- P0491
- P0492
- P0500
- P0501
- P0503
- P0505
- P0506
- P0507
- P0512
- P0520
- P0530
- P0532
- P0533
- P0560
- P0561
- P0562
- P0563
- P0571
- P0597
- P0598
- P0599
- P0600
- P0601
- P0603
- P0604
- P0605
- P0606
- P0620
- P0704
- P0705
- P0710
- P0711
- P0712
- P0713
- P0714
- P0715
- P0716
- P0717
- P0720
- P0721
- P0722
- P0727
- P0730
- P0731
- P0732
- P0733
- P0734
- P0735
- P0740
- P0741
- P0743
- P0745
- P0748
- P0750
- P0751
- P0752
- P0753
- P0755
- P0756
- P0757
- P0758
- P0760
- P0761
- P0762
- P0763
- P0768
- P0773
- P0775
- P0778
- P0781
- P0782
- P0783
- P0784
- P0795
- P0798
- P0829
- P0962
- P0963
- P0966
- P0967
- P0970
- P0971
- P0973
- P0979
- P1001
- P1002
- P1003
- P1004
- P1005
- P1006
- P1007
- P1008
- P1009
- P1010
- P1011
- P1012
- P1013
- P1014
- P1015
- P1022
- P1023
- P1024
- P1025
- P1026
- P1027
- P1028
- P1030
- P1031
- P1033
- P1034
- P1035
- P1036
- P1037
- P1038
- P1039
- P1040
- P1041
- P1042
- P1043
- P1044
- P1045
- P1046
- P1047
- P1048
- P1050
- P1051
- P1052
- P1054
- P1055
- P1056
- P1057
- P1058
- P1059
- P1060
- P1061
- P1062
- P1063
- P1065
- P1352
- P1354
- P1355
- P1356
- P1357
- P1377
- P1381
- P1382
- P1383
- P1384
- P1385
- P1386
- P1396
- P1397
- P1403
- P1411
- P1412
- P1413
- P1414
- P1418
- P1420
- P1421
- P1423
- P1432
- P1453
- P1470
- P1472
- P1473
- P1475
- P1476
- P1500
- P1501
- P1502
- P1503
- P1504
- P1506
- P1507
- P1508
- P1509
- P1511
- P1512
- P1513
- P1515
- P1517
- P1518
- P1519
- P1521
- P1522
- P1526
- P1527
- P1529
- P1530
- P1532
- P1535
- P1536
- P1537
- P1538
- P1539
- P1542
- P1550
- P1551
- P1590
- P1591
- P1592
- P1603
- P1604
- P1614
- P1624
- P1626
- P1628
- P1629
- P1633
- P1634
- P1635
- P1636
- P1637
- P1638
- P1639
- P1640
- P1641
- P1642
- P1643
- P1644
- P1645
- P1649
- P1650
- P1660
- P1661
- P1662
- P1663
- P1664
- P1665
- P1666
- P1667
- P1668
- P1677
- P1680
- P1719
- P1720
- P1721
- P1727
- P1728
- P1734
- P1738
- P1740
- P1743
- P1745
- P1747
- P1750
- P1753
- P1758
- P1762
- P1763
- P1764
- P1765
- P1766
- P1771
- P1782
- P1790
- P1791
- P1801
- P1802
- P1803
- P1810
- P1811
- P1812
- P1813
- P1814
- P1831
- P1832
- P1833
- P1834
- P1835
- P1841
- P1842
- P1843
- P1844
- P1845
- P1861
- P1862
- P1863
- P1864
- P1865
- P1881
- P1882
- P1883
- P1884
- P1885
- P1889
- P1890
- P1891
- P1892
- P1893
- P1894
- P1895
- P2089
- P2090
- P2091
- P2093
- P2094
- P2195
- P2196
- P2197
- P2198
- P2227
- P2228
- P2229
- P2231
- P2234
- P2237
- P2240
- P2243
- P2247
- P2251
- P2254
- P2270
- P2271
- P2272
- P2273
- P2400
- P2401
- P2402
- P2414
- P2415
- P2418
- P2419
- P2420
- P2430
- P2540
- P2626
- P2629
- P2713
- P2716
- P2720
- P2721
- P2722
- P2725
- P2729
- P2730
- P2761
- P2763
- P2764
- P3013
- P3014
- P3015
- P3016
- P3017
- P3018
- P3019
- P3020
- P3021
- P3022
- P3023
- P3024
- P3025
- P3026
- P3027
- P3028
- P3029
- P3037
- P3200
- P3201
- P3202
- P3203
- P3204
- P3205
- P3206
- P3207
- P3208
- P3209
- P3210
- P3211
- P3212
- P3213
- P3214
- P3215
- P3216
- P3217
- P3219
- P3220
- P3221
- P3223
- P3225
- P3226
- P3227
- P3228
- P3231
- P3232
- P3233
- P3236
- P3237
- P3238
- P3247
- P3300
- P3301
- P3302
- P3303
- P3304
- P3305
- P3306
- P3307
- P3308
- P3309
- P3310
- P3311
- P3312
- P3313
- P3314
- P3315
- P3316
- P3317
- P3318
- P3319
- P3320
- U1115
- U1116
- U1120
- U1121
- U1129
- U1134
- Buick DTC
- C0055
- C0235
- C0241
- C0244
- C0267
- C0287
- C0298
- C0660
- C0775
- P000
- P0008
- P0009
- P000B
- P000C
- P000D
- P0010
- P0011
- P0013
- P0014
- P0016
- P0017
- P0018
- P0019
- P0020
- P0021
- P0023
- P0024
- P0030
- P0031
- P0032
- P0036
- P0037
- P0038
- P0050
- P0053
- P0054
- P0056
- P0059
- P0060
- P0068
- P0087
- P0088
- P0089
- P0090
- P0091
- P0092
- P0100
- P0101
- P0102
- P0103
- P0106
- P0107
- P0108
- P0111
- P0113
- P0116
- P0117
- P0118
- P0119
- P0120
- P0121
- P0122
- P0123
- P0125
- P0128
- P0130
- P0131
- P0132
- P0133
- P0134
- P0135
- P0136
- P0137
- P0138
- P013C
- P013E
- P0140
- P014A
- P0150
- P0151
- P0152
- P0153
- P0154
- P0155
- P0157
- P0158
- P0160
- P0167
- P0171
- P0172
- P0174
- P0175
- P0200
- P0201
- P0202
- P0203
- P0204
- P0205
- P0206
- P0207
- P0208
- P0218
- P0220
- P0221
- P0222
- P0223
- P0230
- P025
- P0261
- P0262
- P0264
- P0265
- P0267
- P0268
- P0270
- P0271
- P0273
- P0276
- P0277
- P029D
- P02A1
- P02A5
- P02A9
- P02AD
- P02B1
- P0300
- P0302
- P0303
- P0304
- P0305
- P0306
- P0307
- P0308
- P0315
- P0318
- P0321
- P0323
- P0324
- P0326
- P0327
- P0328
- P0330
- P0331
- P0332
- P0333
- P0335
- P0336
- P0338
- P0340
- P0341
- P0343
- P0346
- P0347
- P0350
- P0351
- P0352
- P0353
- P0354
- P0355
- P0356
- P0357
- P0358
- P0365
- P0366
- P0367
- P0368
- P0372
- P0385
- P0386
- P0392
- P0393
- P0400
- P0401
- P0403
- P0404
- P0405
- P0406
- P0410
- P0411
- P0412
- P0418
- P0420
- P0430
- P0440
- P0442
- P0443
- P0446
- P0449
- P0450
- P0451
- P0452
- P0453
- P0455
- P0458
- P0459
- P0461
- P0462
- P0463
- P0464
- P0480
- P0481
- P0483
- P0493
- P0495
- P0496
- P0497
- P0498
- P0499
- P050
- P0500
- P0501
- P0502
- P0503
- P0504
- P0506
- P0507
- P0520
- P0521
- P0522
- P0523
- P0530
- P0531
- P0532
- P0533
- P0556
- P0557
- P0558
- P0560
- P0562
- P0563
- P0564
- P0568
- P0571
- P0575
- P060
- P0601
- P0602
- P0603
- P0604
- P0605
- P0606
- P0607
- P0608
- P060D
- P0615
- P0616
- P0617
- P0620
- P0621
- P0622
- P0625
- P0626
- P0627
- P0628
- P062B
- P062F
- P0634
- P0638
- P0641
- P0645
- P0646
- P0647
- P064A
- P0650
- P0651
- P0654
- P0656
- P0658
- P0659
- P0667
- P0668
- P0669
- P0685
- P0686
- P0687
- P0690
- P0691
- P0692
- P0693
- P0694
- P06A6
- P06AC
- P06AD
- P06AE
- P0700
- P0703
- P0705
- P0706
- P0711
- P0712
- P0713
- P0716
- P0717
- P0719
- P071A
- P0723
- P0724
- P0730
- P0740
- P0741
- P0742
- P0748
- P0751
- P0752
- P0753
- P0755
- P0756
- P0757
- P0758
- P0776
- P0777
- P0785
- P0787
- P0788
- P0796
- P0797
- P0816
- P0826
- P0843
- P0850
- P0851
- P0852
- P0856
- P0864
- P0872
- P0873
- P0877
- P0878
- P0894
- P0961
- P0962
- P0963
- P0965
- P0966
- P0967
- P0969
- P0970
- P0971
- P0973
- P0974
- P0976
- P0977
- P0990
- P1011
- P1012
- P1013
- P1014
- P1101
- P1106
- P1107
- P1111
- P1112
- P1114
- P1115
- P1121
- P1122
- P1125
- P1133
- P1134
- P1137
- P1138
- P1153
- P1154
- P1174
- P1175
- P1189
- P1200
- P1222
- P1257
- P1258
- P1260
- P1336
- P1350
- P1351
- P1352
- P1361
- P1362
- P1374
- P1380
- P1381
- P1400
- P1404
- P1406
- P1415
- P1416
- P1441
- P1442
- P1481
- P1482
- P1483
- P1484
- P150
- P1504
- P1508
- P1509
- P150B
- P1516
- P1520
- P1530
- P1532
- P1533
- P1536
- P1539
- P1540
- P1543
- P1545
- P1546
- P1550
- P1551
- P1554
- P1558
- P1561
- P1562
- P1565
- P1567
- P1568
- P1573
- P1574
- P1575
- P1585
- P1599
- P1600
- P1602
- P1604
- P1605
- P1610
- P1619
- P1621
- P1623
- P1626
- P1627
- P1630
- P1631
- P1632
- P1633
- P1634
- P1635
- P1637
- P1638
- P1639
- P1640
- P1641
- P1642
- P1643
- P1644
- P1645
- P1646
- P1651
- P1652
- P1653
- P1654
- P1655
- P1657
- P1660
- P1661
- P1662
- P1665
- P1667
- P1668
- P167
- P1670
- P1671
- P1672
- P1673
- P1675
- P1676
- P167D
- P1680
- P1681
- P1682
- P1683
- P1684
- P1685
- P1686
- P1689
- P1751
- P1762
- P1810
- P1811
- P1812
- P1815
- P1816
- P1817
- P1818
- P1819
- P1820
- P1822
- P1823
- P1825
- P1826
- P182E
- P1831
- P1832
- P1845
- P1860
- P1864
- P1870
- P1873
- P1874
- P1886
- P1887
- P1915
- P2008
- P2009
- P2010
- P2066
- P2088
- P2089
- P2090
- P2091
- P2092
- P2093
- P2094
- P2095
- P2096
- P2097
- P2098
- P2099
- P2100
- P2101
- P2105
- P2107
- P2108
- P2119
- P2120
- P2121
- P2122
- P2123
- P2125
- P2127
- P2128
- P2135
- P2138
- P2162
- P2177
- P2178
- P2179
- P2180
- P2187
- P2188
- P2189
- P2190
- P2195
- P2196
- P2227
- P2228
- P2229
- P2231
- P2232
- P2235
- P2237
- P2243
- P2251
- P2270
- P2271
- P2272
- P2273
- P2297
- P2300
- P2301
- P2303
- P2304
- P2306
- P2307
- P2309
- P2310
- P2312
- P2313
- P2315
- P2316
- P2431
- P2432
- P2433
- P2440
- P2444
- P2534
- P2544
- P258A
- P258B
- P258C
- P258D
- P2610
- P2626
- P2635
- P2715
- P2719
- P2720
- P2721
- P2723
- P2724
- P2728
- P2729
- P2730
- P2761
- P2763
- P2764
- P2769
- P2770
- P2A00
- P2A01
- P2A04
- P3400
- P3401
- P3425
- P3441
- P3449
- U0001
- U0073
- U0100
- U0101
- U0140
- U0151
- U0155
- U0184
- U0299
- U1001
- U1016
- U1017
- U1024
- U1026
- U1040
- U1041
- U1048
- U1088
- U1096
- U1097
- U1098
- U1099
- U1111
- U1128
- U1129
- U1133
- U1137
- U1144
- U1147
- U1151
- U1152
- U1153
- U1160
- U1161
- U1162
- U1163
- U1166
- U1167
- U1170
- U1173
- U1176
- U1192
- U1241
- U1254
- U1255
- U1300
- U1301
- U1305
- U1500
- U2100
- U2105
- U2107
- U2108
- U2199
- Cadilack DTC
- B1513
- B1514
- B3105
- B3844
- C008
- C0235
- C0236
- C0237
- C0298
- C0775
- C120
- C120
- C120C
- C120D
- C121
- C121
- C121C
- C121D
- C121F
- C122
- C123
- C123
- C123B
- C123C
- C123D
- C123F
- C124F
- C1255
- C1256
- C126D
- C126E
- C126F
- C1276
- C1277
- C127C
- C127D
- C127E
- C128
- C128
- C128B
- C128C
- C128D
- C128F
- C129
- C129B
- C129D
- C12A7
- C12B1
- C12B2
- C12B3
- C12B4
- C12B6
- C12B7
- C12B8
- C12B9
- C12BA
- C12BB
- C12BC
- C12BD
- C12BE
- C12C2
- C12C5
- C12C6
- C12C8
- C12CC
- C12CF
- C12D0
- C12D1
- C12D2
- C12D3
- C12D4
- C12D5
- C12D6
- C12D7
- C12D8
- C12D9
- C12DA
- C12DB
- C12DC
- C12DD
- C12DE
- C12DF
- C12E4
- C12E6
- C12E7
- C12F2
- C12F3
- C12F4
- C12F5
- C12F6
- C12F7
- C12F8
- C1457
- C145D
- C1464
- C1477
- C1480
- C14A4
- C151C
- C157C
- C157E
- C1580
- C1581
- C2201
- C2205
- C2209
- C2210
- C2219
- C2226
- P0010
- P0011
- P0016
- P0018
- P0019
- P0030
- P0031
- P0032
- P0036
- P0037
- P0038
- P0050
- P0051
- P0052
- P0053
- P0054
- P0056
- P0057
- P0058
- P0059
- P0060
- P0061
- P0062
- P0068
- P0071
- P0100
- P0101
- P0102
- P0103
- P0105
- P0106
- P0107
- P0108
- P0110
- P0111
- P0112
- P0113
- P0116
- P0117
- P0118
- P0120
- P0121
- P0122
- P0123
- P0125
- P0128
- P0130
- P0131
- P0132
- P0133
- P0134
- P0135
- P0136
- P0137
- P0138
- P0139
- P013A
- P013B
- P013C
- P013D
- P013E
- P013F
- P0140
- P0141
- P0143
- P0144
- P0146
- P0147
- P014A
- P014B
- P0150
- P0151
- P0152
- P0153
- P0154
- P0155
- P0156
- P0157
- P0158
- P0159
- P0160
- P0161
- P0165
- P0169
- P0171
- P0172
- P0174
- P0175
- P0178
- P0179
- P018B
- P018C
- P018D
- P0196
- P0200
- P0201
- P0202
- P0203
- P0204
- P0205
- P0206
- P0207
- P0208
- P0211
- P0218
- P0219
- P0220
- P0221
- P0222
- P0223
- P023
- P0230
- P0231
- P0232
- P023B
- P0261
- P0262
- P0264
- P0265
- P0267
- P0268
- P0270
- P0271
- P0273
- P0274
- P0276
- P0277
- P0298
- P0300
- P0301
- P0302
- P0303
- P0304
- P0305
- P0306
- P0307
- P0308
- P0313
- P0315
- P0318
- P0321
- P0322
- P0323
- P0324
- P0325
- P0326
- P0327
- P0328
- P0330
- P0331
- P0332
- P0333
- P0335
- P0336
- P0337
- P0338
- P0339
- P0340
- P0341
- P0342
- P0343
- P0351
- P0352
- P0353
- P0354
- P0355
- P0356
- P0357
- P0358
- P0371
- P0372
- P0381
- P0385
- P0386
- P0400
- P0401
- P0403
- P0404
- P0405
- P0406
- P0410
- P0411
- P0412
- P0418
- P0419
- P0420
- P042E
- P0430
- P0440
- P0441
- P0442
- P0443
- P0444
- P0445
- P0446
- P0447
- P0448
- P0449
- P0450
- P0451
- P0452
- P0453
- P0454
- P0455
- P0461
- P0462
- P0463
- P0464
- P0480
- P0481
- P0482
- P0496
- P0500
- P0501
- P0502
- P0503
- P0504
- P0505
- P0506
- P0507
- P0512
- P0513
- P0520
- P0522
- P0523
- P0530
- P0531
- P0532
- P0533
- P0550
- P0560
- P0561
- P0562
- P0563
- P0567
- P0568
- P0571
- P0572
- P0573
- P0574
- P0575
- P0601
- P0602
- P0603
- P0604
- P0605
- P0606
- P0607
- P0608
- P0609
- P060D
- P0610
- P0615
- P0616
- P0617
- P061A
- P061B
- P0620
- P0621
- P0622
- P0625
- P0626
- P0628
- P0629
- P062F
- P0633
- P0634
- P0638
- P0641
- P0642
- P0643
- P0645
- P0646
- P0647
- P0650
- P0651
- P0652
- P0653
- P0654
- P0658
- P0659
- P0660
- P0661
- P0662
- P0667
- P0668
- P0669
- P0685
- P0689
- P0690
- P069E
- P06AC
- P0717
- P0719
- P071A
- P0721
- P0722
- P0723
- P0724
- P0725
- P0727
- P0729
- P0730
- P0731
- P0732
- P0733
- P0734
- P0735
- P0736
- P0740
- P0741
- P0742
- P0743
- P0748
- P0751
- P0752
- P0753
- P0756
- P0757
- P0758
- P0761
- P0762
- P0776
- P0777
- P0785
- P079
- P0796
- P0797
- P079B
- P079C
- P079D
- P07A3
- P07A5
- P07A7
- P07A9
- P0802
- P0815
- P0816
- P0826
- P0827
- P0828
- P0842
- P0843
- P0847
- P0848
- P0850
- P0851
- P0852
- P0856
- P0872
- P0873
- P0877
- P0878
- P0880
- P0881
- P0882
- P0883
- P0894
- P0897
- P0960
- P0961
- P0962
- P0963
- P0964
- P0965
- P0966
- P0967
- P0969
- P0970
- P0971
- P0972
- P0973
- P0974
- P0975
- P0976
- P0977
- P0978
- P0979
- P0980
- P0989
- P0990
- P0A01
- P0A02
- P0A03
- P0A06
- P0A07
- P0A0A
- P0A1B
- P0A1C
- P0A1D
- P0A1F
- P0A2B
- P0A2C
- P0A2D
- P0A2F
- P0A31
- P0A32
- P0A33
- P0A35
- P0A3E
- P0A3F
- P0A40
- P0A45
- P0A46
- P0A78
- P0A79
- P0A7E
- P0A80
- P0A81
- P0A8D
- P0A8E
- P0A95
- P0A9C
- P0A9D
- P0A9E
- P0AAD
- P0AAE
- P0AAF
- P0AB2
- P0AB3
- P0AB4
- P0AB9
- P0ABB
- P0ABC
- P0ABD
- P0AC0
- P0AC1
- P0AC2
- P0AC4
- P0AC6
- P0AC7
- P0AC8
- P0ACB
- P0ACC
- P0ACD
- P0ADB
- P0ADC
- P0ADF
- P0AE0
- P0AE7
- P0AE9
- P0AEA
- P0AEB
- P0AEF
- P0AF0
- P0AF4
- P0AF5
- P0AF7
- P0AFA
- P0AFB
- P0AFF
- P0B3C
- P0B3D
- P0B3E
- P0B41
- P0B42
- P0B43
- P0B46
- P0B47
- P0B48
- P0B4B
- P0B4C
- P0B4D
- P0B50
- P0B51
- P0B52
- P0B55
- P0B56
- P0B57
- P0B5A
- P0B5B
- P0B5C
- P0B5F
- P0B60
- P0B64
- P0B65
- P0B66
- P0B69
- P0B6A
- P0B6B
- P0B6E
- P0B6F
- P0B70
- P0B73
- P0B74
- P0B75
- P0B78
- P0B79
- P0B7A
- P0B7D
- P0B7F
- P0B82
- P0B83
- P0B84
- P0B87
- P0B88
- P0B89
- P0B8C
- P0B8D
- P0B8E
- P0B91
- P0B92
- P0B93
- P0B96
- P0B97
- P0B98
- P0B9B
- P0B9C
- P0B9D
- P0BBD
- P0BC1
- P0BD3
- P0BD4
- P0BD8
- P0BD9
- P0BDD
- P0BDE
- P0BE2
- P0BE3
- P0BFD
- P0BFE
- P0C05
- P0C08
- P0C0B
- P0C0E
- P0C11
- P0C12
- P0C13
- P0C14
- P0C15
- P0C16
- P0C18
- P0C1A
- P0C2B
- P0C2F
- P0C32
- P0C52
- P0C53
- P0C57
- P0C58
- P0C5C
- P0C5D
- P0C61
- P0C62
- P0C76
- P0C77
- P1031
- P1032
- P1101
- P1106
- P1107
- P1108
- P1111
- P1112
- P1113
- P1114
- P1115
- P1120
- P1121
- P1122
- P1133
- P1134
- P1139
- P1140
- P1141
- P1153
- P1154
- P1161
- P1171
- P1174
- P1175
- P1220
- P1221
- P1222
- P1258
- P1260
- P1271
- P1275
- P1276
- P1280
- P1281
- P1285
- P1286
- P1323
- P1336
- P1345
- P1350
- P1351
- P1352
- P1359
- P1360
- P1361
- P1370
- P1371
- P1372
- P1374
- P1375
- P1376
- P1377
- P1380
- P1381
- P1400
- P1404
- P1406
- P1415
- P1416
- P1431
- P1433
- P1441
- P1460
- P1483
- P1501
- P1502
- P1503
- P1508
- P1509
- P150C
- P1510
- P1511
- P1515
- P1516
- P1517
- P1518
- P1519
- P1520
- P1523
- P1524
- P1526
- P1527
- P1531
- P1532
- P1536
- P1539
- P1540
- P1543
- P1545
- P1546
- P1551
- P1554
- P1560
- P1564
- P1566
- P1567
- P1570
- P1571
- P1572
- P1574
- P1575
- P1576
- P1577
- P1578
- P1579
- P1585
- P1599
- P15F0
- P15F1
- P15F2
- P1600
- P1601
- P1602
- P1603
- P1604
- P1605
- P1610
- P1611
- P1612
- P1613
- P1614
- P1615
- P1617
- P1621
- P1624
- P1625
- P1626
- P1627
- P1629
- P162B
- P1630
- P1631
- P1632
- P1633
- P1634
- P1635
- P1637
- P1638
- P1639
- P1640
- P1641
- P1642
- P1643
- P1644
- P1645
- P1646
- P1650
- P1652
- P1653
- P1654
- P1657
- P1660
- P1661
- P1662
- P1663
- P1668
- P1670
- P1680
- P1682
- P1683
- P1684
- P1685
- P1686
- P1688
- P1689
- P16F2
- P16F3
- P16F4
- P16F5
- P16F6
- P16F9
- P1700
- P1701
- P1705
- P1740
- P1743
- P1751
- P1760
- P1762
- P1779E
- P1780
- P1781
- P1791
- P1792E
- P1793
- P1795
- P179B
- P1800
- P181
- P1810
- P1811
- P1812
- P1814
- P1815
- P1818
- P1819
- P181C
- P181D
- P181F
- P1820
- P1822
- P1823
- P1824
- P1825
- P1826
- P182A
- P182B
- P182C
- P182D
- P182E
- P182F
- P183
- P183
- P1831
- P1832
- P1833
- P1834
- P1835
- P183B
- P183C
- P183D
- P183F
- P1842
- P1843
- P1845
- P1847
- P184A
- P184B
- P1850
- P1860
- P1864
- P1865
- P1866
- P1867
- P1868
- P1870
- P1873
- P1874
- P1875
- P1876
- P1886
- P1887
- P1890
- P1895
- P1915
- P1A00
- P1A01
- P1A02
- P1A04
- P1A06
- P1A07
- P1A08
- P1A09
- P1A0C
- P1A0D
- P1A1F
- P1A20
- P1A21
- P1A4E
- P1A4F
- P1A50
- P1A51
- P1A52
- P1A53
- P1A54
- P1A6C
- P1A7E
- P1A7F
- P1A80
- P1A82
- P1A83
- P1A84
- P1A85
- P1A86
- P1A87
- P1A88
- P1A89
- P1A8A
- P1A8C
- P1ABE
- P1AC1
- P1AC6
- P1AC7
- P1ADC
- P1ADD
- P1ADE
- P1AE0
- P1AE2
- P1AE3
- P1AE4
- P1AE5
- P1AE6
- P1AE7
- P1AE8
- P1AE9
- P1AEA
- P1AEB
- P1AEC
- P1AED
- P1AEE
- P1AEF
- P1AF0
- P1AF2
- P1AF4
- P1AF5
- P1AF6
- P1AF7
- P1AF8
- P1AFA
- P1AFB
- P1AFC
- P1AFD
- P1AFE
- P1B01
- P1B02
- P1B03
- P1B04
- P1B05
- P1B06
- P1B0D
- P1B0E
- P1B10
- P1B15
- P2008
- P2009
- P2010
- P2067
- P2068
- P2096
- P2099
- P2100
- P2101
- P2105
- P2107
- P2110
- P2119
- P2120
- P2121
- P2122
- P2123
- P2125
- P2127
- P2128
- P2135
- P2138
- P215B
- P215C
- P2160
- P2161
- P2176
- P219A
- P219B
- P2227
- P2228
- P2229
- P2270
- P2271
- P2272
- P2273
- P2430
- P2431
- P2432
- P2433
- P2440
- P2444
- P2500
- P2501
- P2534
- P2544
- P254F
- P2610
- P2632
- P2636
- P2670
- P2714
- P2715
- P2719
- P2720
- P2721
- P2723
- P2724
- P2727
- P2728
- P2729
- P2730
- P2761
- P2762
- P2763
- P2764
- P2771
- P2796
- P2797
- P279D
- P2A00
- P2A01
- P2A03
- P2A04
- P3400
- P3401
- P3425
- P3441
- P3449
- U0001
- U0073
- U0100
- U0101
- U0104
- U0105
- U0106
- U0107
- U0111
- U0120
- U0121
- U0122
- U0131
- U0132
- U0151
- U0155
- U0159
- U0170
- U0184
- U0186
- U0194
- U0198
- U0199
- U0200
- U0209
- U0214
- U0241
- U0293
- U0299
- U1000
- U1001
- U1016
- U1026
- U1040
- U1041
- U1048
- U1056
- U1064
- U1065
- U1066
- U1088
- U1096
- U1097
- U1128
- U1129
- U1144
- U1145
- U1151
- U1152
- U1153
- U1160
- U1161
- U1162
- U1163
- U1166
- U1169
- U1170
- U1176
- U1192
- U1193
- U1254
- U1300
- U1301
- U1305
- U1500
- U1511
- U1512
- U1513
- U1713
- U1714
- U1715
- U1716
- U1800
- U180F
- U1814
- U1842
- U1843
- U186A
- U1881
- U1883
- U1884
- U1885
- U1886
- U1887
- U1888
- U1889
- U1890
- U1891
- U1892
- U1893
- U1894
- U1895
- U1896
- U1897
- U1898
- U1899
- U2099
- U2100
- U2102
- U2103
- U2104
- U2106
- U2108
- U2150
- U2151
- U2153
- → P1320
- Chevrolet DTC
- B1016
- B101D
- B1428
- B2713
- B2722
- B3105
- C0235
- C0236
- C0237
- C0240
- C0241
- C0244
- C0267
- C0287
- C0292
- C0298
- C0775
- C120
- C120D
- C121
- C121
- C121C
- C121D
- C121F
- C122
- C123
- C123
- C123B
- C123C
- C123D
- C1256
- C126E
- C126F
- C1276
- C127C
- C127D
- C128
- C128
- C128B
- C128C
- C128D
- C128F
- C129
- C129
- C129B
- C129D
- C12A7
- C12B1
- C12B2
- C12B3
- C12B4
- C12B6
- C12B7
- C12B8
- C12B9
- C12BA
- C12BB
- C12BC
- C12BD
- C12BE
- C12C2
- C12C6
- C12CC
- C12CF
- C12D0
- C12D1
- C12D2
- C12D3
- C12D4
- C12D5
- C12D6
- C12D7
- C12D9
- C12DA
- C12DB
- C12DC
- C12DD
- C12DE
- C12DF
- C12E1
- C12E2
- C12E4
- C12E6
- C12E7
- C12F2
- C12F3
- C12F4
- C12F6
- C12F7
- P000
- P0005
- P0008
- P000B
- P000C
- P000D
- P0011
- P0013
- P0014
- P0016
- P0017
- P0018
- P0019
- P0020
- P0021
- P0023
- P0024
- P003
- P0030
- P0031
- P0032
- P0033
- P0036
- P0037
- P0038
- P0045
- P0047
- P0048
- P0050
- P0051
- P0052
- P0053
- P0054
- P0056
- P006
- P0060
- P0068
- P0069
- P006D
- P006F
- P0072
- P0073
- P007C
- P007D
- P0088
- P0089
- P009
- P0090
- P0092
- P0093
- P0094
- P0096
- P0097
- P0098
- P00B3
- P00B4
- P00B6
- P00B7
- P00C9
- P00CA
- P0100
- P0101
- P0102
- P0103
- P0105
- P0106
- P0107
- P0110
- P0111
- P0112
- P0113
- P0114
- P0115
- P0116
- P0117
- P0118
- P0119
- P0120
- P0121
- P0122
- P0123
- P0125
- P0126
- P0128
- P012B
- P0130
- P0131
- P0132
- P0133
- P0134
- P0135
- P0136
- P0137
- P0138
- P013A
- P013B
- P013D
- P013E
- P013F
- P0140
- P0141
- P0143
- P0144
- P0148
- P014B
- P0150
- P0152
- P0153
- P0154
- P0155
- P0157
- P0158
- P0160
- P0161
- P0168
- P0169
- P0171
- P0174
- P0175
- P0178
- P0179
- P0181
- P0182
- P0183
- P0187
- P0188
- P0191
- P0193
- P0200
- P0201
- P0202
- P0203
- P0206
- P0207
- P0208
- P0215
- P0216
- P0217
- P0218
- P0220
- P0221
- P0222
- P0223
- P0226
- P0227
- P0228
- P023
- P0230
- P0231
- P0232
- P0234
- P0236
- P0237
- P0238
- P023F
- P0243
- P025
- P0251
- P0262
- P0263
- P0264
- P0266
- P0267
- P0268
- P0269
- P0270
- P0271
- P0272
- P0273
- P0275
- P0276
- P0277
- P0278
- P0281
- P0299
- P029D
- P02A1
- P02A5
- P02AD
- P02B1
- P02B5
- P02B9
- P02E0
- P02E2
- P02E7
- P02E8
- P02EB
- P0300
- P0301
- P0302
- P0303
- P0304
- P0305
- P0306
- P0307
- P0308
- P0315
- P0321
- P0323
- P0324
- P0325
- P0326
- P0327
- P0328
- P0330
- P0331
- P0332
- P0333
- P0335
- P0336
- P0337
- P0339
- P0340
- P0341
- P0342
- P0343
- P0346
- P0347
- P0348
- P0350
- P0352
- P0353
- P0354
- P0355
- P0356
- P0357
- P0358
- P0365
- P0366
- P0367
- P0370
- P0372
- P0374
- P0380
- P0381
- P0385
- P0391
- P0392
- P0393
- P0401
- P0402
- P0403
- P0404
- P0406
- P040C
- P040D
- P040F
- P0410
- P0411
- P0418
- P041C
- P0420
- P042E
- P0430
- P043E
- P043F
- P0440
- P0441
- P0442
- P0443
- P0444
- P0445
- P0446
- P0449
- P0450
- P0451
- P0452
- P0453
- P0454
- P0456
- P0459
- P0460
- P0461
- P0462
- P0463
- P0464
- P046C
- P0480
- P0481
- P0482
- P0483
- P0488
- P0489
- P0490
- P0493
- P0494
- P0495
- P0496
- P0497
- P0498
- P049D
- P050
- P0500
- P0501
- P0502
- P0503
- P0504
- P0505
- P0506
- P0508
- P0510
- P0513
- P0520
- P0522
- P0526
- P0530
- P0532
- P0533
- P0534
- P0537
- P0538
- P0540
- P0543
- P0545
- P0546
- P0556
- P0557
- P0558
- P0561
- P0562
- P0563
- P0564
- P0567
- P0568
- P0571
- P0572
- P0573
- P0597
- P0598
- P0599
- P060
- P0600
- P0601
- P0602
- P0603
- P0604
- P0605
- P0606
- P0607
- P0608
- P0609
- P060B
- P060D
- P0610
- P0611
- P0613
- P0615
- P0616
- P0617
- P061A
- P061B
- P061C
- P0620
- P0621
- P0622
- P0627
- P0628
- P0629
- P062C
- P062F
- P0630
- P0638
- P0640
- P0641
- P0642
- P0643
- P0645
- P0646
- P064A
- P064C
- P0650
- P0651
- P0652
- P0653
- P0654
- P0656
- P0657
- P0658
- P0659
- P065E
- P0660
- P0661
- P0662
- P0667
- P0668
- P0669
- P0671
- P0672
- P0673
- P0674
- P0675
- P0676
- P0677
- P0685
- P0687
- P0689
- P068B
- P0690
- P0697
- P0698
- P0699
- P069E
- P06A3
- P06A6
- P06AD
- P06AE
- P06AF
- P06B1
- P06B2
- P06B4
- P06B5
- P06D2
- P06E8
- P0700
- P0701
- P0703
- P0704
- P0705
- P0707
- P0708
- P0712
- P0713
- P0715
- P0717
- P0719
- P071A
- P0720
- P0721
- P0722
- P0724
- P0726
- P0727
- P0729
- P0730
- P0731
- P0732
- P0733
- P0734
- P0735
- P0736
- P0740
- P0741
- P0742
- P0743
- P0746
- P0747
- P0750
- P0751
- P0752
- P0755
- P0757
- P0758
- P0761
- P0762
- P0763
- P0770
- P0771
- P0773
- P0777
- P0778
- P0785
- P0787
- P0788
- P079
- P0796
- P0797
- P079B
- P079C
- P079D
- P07A3
- P07A5
- P07A7
- P07A9
- P0801
- P0802
- P0804
- P0806
- P0807
- P0808
- P0815
- P0826
- P0827
- P0828
- P0831
- P0833
- P0836
- P0840
- P0841
- P0842
- P0843
- P0845
- P0846
- P0847
- P0850
- P0851
- P0852
- P0856
- P0870
- P0872
- P0873
- P0875
- P0876
- P0877
- P0878
- P0880
- P0881
- P0882
- P0883
- P0894
- P0897
- P0960
- P0963
- P0964
- P0966
- P0967
- P0969
- P0970
- P0971
- P0972
- P0973
- P0975
- P0976
- P0977
- P0978
- P0979
- P0980
- P0982
- P0983
- P0985
- P0986
- P0989
- P0990
- P0A01
- P0A02
- P0A03
- P0A06
- P0A0A
- P0A0C
- P0A1B
- P0A1C
- P0A1D
- P0A1F
- P0A27
- P0A2B
- P0A2C
- P0A2D
- P0A2F
- P0A31
- P0A32
- P0A33
- P0A35
- P0A3E
- P0A3F
- P0A45
- P0A78
- P0A7E
- P0A7F
- P0A80
- P0A81
- P0A82
- P0A83
- P0A88
- P0A8B
- P0A8D
- P0A8E
- P0A95
- P0A9C
- P0A9D
- P0A9E
- P0AA6
- P0AAE
- P0AAF
- P0AB2
- P0AB4
- P0AB9
- P0ABB
- P0ABF
- P0AC0
- P0AC1
- P0AC2
- P0AC4
- P0AC6
- P0AC7
- P0ACB
- P0ACC
- P0ACD
- P0AD9
- P0ADB
- P0ADC
- P0ADD
- P0ADF
- P0AE0
- P0AE7
- P0AEA
- P0AEB
- P0AEE
- P0AEF
- P0AF0
- P0AF4
- P0AF5
- P0AF7
- P0AF8
- P0AFA
- P0AFB
- P0AFF
- P0B0D
- P0B10
- P0B11
- P0B13
- P0B3B
- P0B3C
- P0B3E
- P0B40
- P0B41
- P0B42
- P0B43
- P0B45
- P0B46
- P0B48
- P0B4A
- P0B4B
- P0B4C
- P0B4D
- P0B4F
- P0B50
- P0B51
- P0B52
- P0B55
- P0B56
- P0B57
- P0B59
- P0B5A
- P0B5B
- P0B5C
- P0B5E
- P0B5F
- P0B60
- P0B61
- P0B63
- P0B64
- P0B65
- P0B68
- P0B69
- P0B6A
- P0B6B
- P0B6D
- P0B6E
- P0B70
- P0B72
- P0B73
- P0B74
- P0B75
- P0B78
- P0B79
- P0B7A
- P0B7D
- P0B7E
- P0B7F
- P0B81
- P0B82
- P0B83
- P0B84
- P0B86
- P0B87
- P0B88
- P0B89
- P0B8B
- P0B8C
- P0B8D
- P0B8E
- P0B90
- P0B91
- P0B92
- P0B93
- P0B96
- P0B98
- P0B9A
- P0B9B
- P0B9C
- P0B9D
- P0BA0
- P0BA1
- P0BA4
- P0BA6
- P0BA7
- P0BA9
- P0BAB
- P0BAE
- P0BAF
- P0BB0
- P0BB1
- P0BB3
- P0BB4
- P0BB5
- P0BB6
- P0BB9
- P0BBA
- P0BBD
- P0BBE
- P0BC1
- P0BC3
- P0BC4
- P0BC5
- P0BD2
- P0BD3
- P0BD7
- P0BD8
- P0BD9
- P0BDC
- P0BDD
- P0BDE
- P0BE1
- P0BE3
- P0BFD
- P0BFE
- P0C01
- P0C04
- P0C08
- P0C0B
- P0C0E
- P0C12
- P0C13
- P0C14
- P0C15
- P0C17
- P0C18
- P0C19
- P0C1A
- P0C20
- P0C2B
- P0C2F
- P0C32
- P0C34
- P0C35
- P0C36
- P0C43
- P0C44
- P0C45
- P0C47
- P0C4A
- P0C4E
- P0C4F
- P0C52
- P0C53
- P0C57
- P0C58
- P0C5D
- P0C61
- P0C62
- P0C76
- P0C77
- P0C78
- P0C7D
- P0C7E
- P0C7F
- P0C83
- P0C84
- P0C89
- P0C8A
- P0C8B
- P0C8E
- P0C8F
- P0C90
- P0C93
- P0C94
- P0C95
- P0C98
- P0C99
- P0C9A
- P0CA9
- P0CAA
- P0CAB
- P0CAE
- P0CAF
- P0CB0
- P0CB3
- P0CB4
- P0CB5
- P0CB8
- P0CBA
- P0CD6
- P0CD7
- P0CD8
- P0CE0
- P0CE2
- P0CE3
- P0CE9
- P0CED
- P0CEF
- P0CF0
- P0CF4
- P0CF6
- P0D01
- P0D0A
- P0D11
- P0D17
- P0D1F
- P0D20
- P0D21
- P0D22
- P0D26
- P0D2B
- P0D2C
- P0D39
- P0D3A
- P0D3B
- P0D3E
- P0D40
- P0D43
- P0D45
- P0D49
- P0D4A
- P0D4E
- P0D4F
- P0D53
- P0D54
- P0D58
- P0D59
- P0D5B
- P0D5C
- P0D5E
- P0D69
- P0D6F
- P0D71
- P0D72
- P0D73
- P0D76
- P0D77
- P0D78
- P0D7A
- P0D7B
- P0D7C
- P0D7D
- P0D7F
- P1021
- P1022
- P1023
- P1024
- P1025
- P1026
- P1027
- P1028
- P1044
- P1045
- P1048
- P1049
- P1093
- P1094
- P10CC
- P10CD
- P10FD
- P1101
- P1106
- P1107
- P1108
- P1111
- P1112
- P1114
- P1115
- P1116
- P111C
- P111D
- P1121
- P1122
- P1125
- P113
- P1132
- P1134
- P1137
- P1138
- P1152
- P1153
- P1154
- P1167
- P1171
- P1172
- P1174
- P1183
- P1184
- P1187
- P1189
- P1191
- P11B2
- P11B5
- P11CC
- P11DB
- P1200
- P1201
- P1202
- P1203
- P1207
- P1214
- P1217
- P1218
- P121B
- P121C
- P122
- P1220
- P1221
- P1224
- P1226
- P1227
- P1229
- P122D
- P122F
- P1230
- P1231
- P1233
- P1238
- P1241
- P1242
- P1247
- P125
- P1250
- P1255
- P1258
- P1261
- P1262
- P1271
- P1272
- P1273
- P1275
- P1276
- P1277
- P1280
- P1283
- P1285
- P1286
- P1287
- P128E
- P1293
- P1294
- P1295
- P1296
- P12B3
- P12B4
- P12B5
- P12B6
- P12B9
- P12BA
- P12BB
- P12BC
- P12BE
- P12BF
- P12C0
- P12C1
- P12C2
- P1300
- P1310
- P1315
- P1321
- P1335
- P1336
- P1345
- P1346
- P1349
- P1350
- P1352
- P1361
- P1371
- P1380
- P1381
- P1382
- P1385
- P1390
- P1391
- P1392
- P1393
- P1397
- P140
- P140
- P1400
- P1402
- P1403
- P1404
- P1405
- P1409
- P140B
- P140D
- P1410
- P1411
- P1413
- P1414
- P1415
- P1416
- P1431
- P1432
- P1433
- P1441
- P1442
- P1448
- P144B
- P144C
- P144F
- P1450
- P1451
- P1458
- P1459
- P145A
- P145C
- P145D
- P145E
- P145F
- P1460
- P1481
- P1482
- P1483
- P1486
- P1487
- P148A
- P148C
- P150
- P150
- P1500
- P150B
- P150D
- P1510
- P1511
- P1512
- P1514
- P1515
- P1516
- P1519
- P151C
- P1530
- P1532
- P1533
- P1537
- P1539
- P153B
- P154
- P1543
- P154B
- P154C
- P154D
- P1550
- P1551
- P1561
- P1562
- P1565
- P1567
- P1568
- P1571
- P1573
- P1575
- P1585
- P1599
- P159C
- P15B9
- P15BA
- P15F0
- P15F1
- P15F2
- P15F9
- P15FB
- P1600
- P1601
- P1602
- P1604
- P1605
- P1607
- P160C
- P1610
- P1611
- P161B
- P1621
- P1623
- P1626
- P1628
- P1629
- P162D
- P163
- P1630
- P1631
- P1632
- P1635
- P1638
- P1639
- P163C
- P163D
- P1640
- P1642
- P1649
- P1651
- P1653
- P1654
- P1655
- P1656
- P1658
- P1661
- P1663
- P1664
- P1665
- P1668
- P166B
- P166C
- P1671
- P1672
- P1673
- P1675
- P1676
- P1681
- P1683
- P1684
- P1686
- P1687
- P1688
- P168C
- P16A0
- P16A1
- P16A2
- P16F3
- P16F4
- P16F5
- P16F6
- P16F7
- P16F9
- P1700
- P1709
- P1711
- P1712
- P1714
- P1715
- P1719
- P1720
- P1721
- P1723
- P1724
- P1740
- P1751
- P1760
- P1762
- P1779E
- P1792E
- P179A
- P179B
- P181
- P1810
- P1812
- P1814
- P1816
- P1819
- P181C
- P181D
- P181F
- P1820
- P1822
- P1824
- P1825
- P1826
- P182B
- P182C
- P182D
- P182F
- P183
- P1831
- P1832
- P1838
- P1839
- P183B
- P183C
- P183D
- P183F
- P184A
- P1862
- P1864
- P1868
- P1870
- P1873
- P1874
- P1875
- P1886
- P1887
- P1915
- P1A00
- P1A02
- P1A04
- P1A05
- P1A06
- P1A09
- P1A0C
- P1A0D
- P1A1F
- P1A21
- P1A24
- P1A2B
- P1A32
- P1A4E
- P1A4F
- P1A50
- P1A51
- P1A52
- P1A53
- P1A54
- P1A56
- P1A58
- P1A5E
- P1A60
- P1A64
- P1A65
- P1A66
- P1A67
- P1A69
- P1A6A
- P1A6C
- P1A71
- P1A72
- P1A73
- P1A76
- P1A77
- P1A78
- P1A79
- P1A7F
- P1A82
- P1A86
- P1A89
- P1A8A
- P1A8C
- P1A90
- P1A91
- P1A92
- P1A93
- P1A94
- P1A96
- P1A97
- P1A98
- P1A9A
- P1AA9
- P1AAB
- P1AAC
- P1AAD
- P1AAE
- P1AB2
- P1ABD
- P1ABE
- P1AC1
- P1AC2
- P1AC6
- P1AC7
- P1AC9
- P1ADC
- P1ADE
- P1ADF
- P1AE0
- P1AE2
- P1AE5
- P1AE6
- P1AE7
- P1AE8
- P1AE9
- P1AEA
- P1AEB
- P1AED
- P1AEE
- P1AEF
- P1AF2
- P1AF5
- P1AF6
- P1AF7
- P1AF8
- P1AFA
- P1AFB
- P1AFD
- P1AFE
- P1B02
- P1B03
- P1B05
- P1B0C
- P1B0D
- P1B0E
- P1B0F
- P1B10
- P1B12
- P1B17
- P1B18
- P1B1A
- P1B1B
- P1B20
- P1B22
- P1B24
- P1B25
- P1B26
- P1B27
- P1B28
- P1B2B
- P1B2C
- P1B2D
- P1B42
- P1B44
- P1B45
- P1B46
- P1B47
- P1B48
- P1B49
- P1B4C
- P1B4D
- P1B50
- P1B51
- P1B52
- P1B54
- P1B57
- P1B59
- P1B5B
- P1B5C
- P1B5D
- P1B5E
- P1B60
- P1B61
- P1B63
- P1B64
- P1B65
- P1B67
- P1B68
- P1B6A
- P1B6B
- P1B6C
- P1B6E
- P1B6F
- P1B70
- P1B71
- P1B72
- P1B73
- P1B74
- P1B78
- P1B79
- P1B7A
- P1B7B
- P1B7D
- P1B80
- P1B81
- P1B82
- P1B83
- P1B84
- P1B85
- P1B86
- P1B87
- P1B88
- P1B89
- P1B8B
- P1B8C
- P1B8D
- P1B8F
- P1B91
- P1B92
- P1B94
- P1B95
- P1B9A
- P1B9B
- P1B9C
- P1B9D
- P1B9E
- P1BA0
- P1BA1
- P1BA2
- P1BA3
- P1BA4
- P1BA5
- P1BA6
- P1BA7
- P1BA8
- P1BA9
- P1BAC
- P1BAE
- P1BB0
- P1BB2
- P1BB3
- P1BB5
- P1BB6
- P1BB7
- P1BBA
- P1BBB
- P1BBC
- P1BBD
- P1BC0
- P1BC1
- P1BC3
- P1BC4
- P1BC5
- P1BC6
- P1BC7
- P1BC9
- P1BCA
- P1BCB
- P1BCD
- P1BCE
- P1BD0
- P1BD1
- P1BD2
- P1BD4
- P1BD5
- P1BD6
- P1BD7
- P1BD8
- P1BD9
- P1BDC
- P1BDF
- P1BE2
- P1BE5
- P1BE7
- P1BE8
- P1BE9
- P1BEA
- P1BEC
- P1BEE
- P1BEF
- P1BF2
- P1BF5
- P1BF6
- P1BFA
- P1BFB
- P1BFC
- P1BFD
- P1BFF
- P1E00
- P1E01
- P1E02
- P1E05
- P1E06
- P1E09
- P1E0A
- P1E0E
- P1E15
- P1E16
- P1E17
- P1E18
- P1E19
- P1E1B
- P1E1D
- P1E1E
- P1E20
- P1E21
- P1E22
- P1E24
- P1E27
- P1E28
- P1E29
- P1E2A
- P1E2B
- P1E2C
- P1E2E
- P1E2F
- P1E30
- P1E31
- P1E32
- P1E33
- P1E34
- P1E35
- P1E36
- P1E37
- P1E38
- P1E39
- P1E3A
- P1E3D
- P1E3F
- P1E41
- P1E43
- P1E44
- P1E45
- P1E49
- P1E4A
- P1E4B
- P1E4C
- P1E4D
- P1E4E
- P1E4F
- P1E51
- P1E53
- P1E54
- P1E55
- P1E56
- P1E57
- P1E59
- P1E5A
- P1E5D
- P1E5E
- P1E61
- P1E62
- P1E63
- P1E65
- P1E66
- P1E67
- P1E68
- P1E69
- P1E6A
- P1E6B
- P1E6C
- P1E6D
- P1E6E
- P1E6F
- P1E72
- P1E73
- P1E74
- P1E75
- P1E76
- P1E77
- P1E78
- P1E7A
- P1E7C
- P1E7E
- P1E7F
- P1E81
- P1E82
- P1E83
- P1E84
- P1E86
- P1E87
- P1E88
- P1E8a
- P1E92
- P1E93
- P1E98
- P1E99
- P1E9E
- P1E9F
- P1EA5
- P1EA6
- P1EA8
- P1EA9
- P1EAC
- P1EB6
- P1EB8
- P1EBA
- P1EBC
- P1EBD
- P1EBE
- P1EBF
- P1EC0
- P1EC3
- P1EC4
- P1EC5
- P1EC6
- P1EC7
- P1EC8
- P1EC9
- P1ECB
- P1ECC
- P1ECD
- P1ECE
- P1ED0
- P1ED1
- P1ED2
- P1ED6
- P1ED7
- P1ED8
- P1ED9
- P1EDA
- P1EDB
- P1EDC
- P1EDD
- P1EDE
- P1EDF
- P1EE0
- P1EE1
- P1EE2
- P1EE4
- P1EE5
- P1EE6
- P1EE7
- P1EE8
- P1EE9
- P1EEA
- P1EEB
- P1EEC
- P1EED
- P1EEF
- P1EF0
- P1EF1
- P1EF3
- P1EF4
- P1EF5
- P1EF6
- P1EF7
- P1EFA
- P1EFC
- P1EFD
- P1EFE
- P1EFF
- P1F01
- P1F02
- P1F03
- P1F04
- P1F05
- P1F0A
- P1F0C
- P1F0E
- P1F14
- P1F15
- P1F16
- P1F17
- P1F18
- P2025
- P2026
- P2027
- P2028
- P2032
- P2033
- P203B
- P203C
- P203D
- P2047
- P2048
- P204B
- P204C
- P205B
- P205C
- P205D
- P2066
- P2068
- P2076
- P2077
- P2078
- P207F
- P2080
- P2084
- P2088
- P2089
- P208A
- P208B
- P208D
- P2090
- P2091
- P2092
- P2093
- P2094
- P2096
- P2098
- P2099
- P20A0
- P20A1
- P20A2
- P20A3
- P20BA
- P20BB
- P20BC
- P20BD
- P20BF
- P20C0
- P20C1
- P20C3
- P20C4
- P20CD
- P20CE
- P20E2
- P20EE
- P2101
- P2104
- P2105
- P2107
- P2108
- P2110
- P2118
- P2119
- P2120
- P2121
- P2122
- P2123
- P2125
- P2127
- P2128
- P2129
- P2132
- P2133
- P2135
- P2139
- P2140
- P2141
- P2142
- P2144
- P2145
- P2149
- P2152
- P2155
- P215B
- P215C
- P216
- P2160
- P2161
- P216D
- P2177
- P2178
- P2179
- P2180
- P2187
- P2188
- P2189
- P2190
- P2195
- P2196
- P2199
- P219A
- P219B
- P21A
- P21AB
- P21AF
- P220
- P2200
- P2201
- P2202
- P2205
- P2209
- P220B
- P2227
- P2229
- P2232
- P2235
- P2261
- P2263
- P2266
- P2269
- P2270
- P2271
- P2273
- P2279
- P2282
- P2294
- P2295
- P2296
- P2297
- P229E
- P229F
- P22A0
- P22A3
- P22A7
- P2300
- P2301
- P2303
- P2306
- P2307
- P2309
- P2310
- P2313
- P2316
- P2400
- P2401
- P2402
- P2413
- P2419
- P2420
- P2422
- P242B
- P242C
- P242D
- P2431
- P2432
- P2433
- P2440
- P2444
- P244C
- P2450
- P2453
- P2454
- P2455
- P2457
- P2459
- P245A
- P245C
- P245D
- P2463
- P246F
- P2470
- P2471
- P2493
- P2494
- P2495
- P249D
- P249E
- P24A0
- P24A1
- P2510
- P2517
- P2518
- P251A
- P251F
- P2535
- P2537
- P254F
- P2563
- P2564
- P2565
- P257D
- P257E
- P258E
- P2598
- P2599
- P260
- P260B
- P260C
- P260D
- P2610
- P2618
- P2619
- P2632
- P2633
- P2634
- P2635
- P2665
- P2669
- P2670
- P2671
- P2681
- P268A
- P268C
- P268D
- P268E
- P268F
- P2690
- P2691
- P2693
- P26A3
- P26A6
- P26A7
- P26A9
- P2714
- P2715
- P2719
- P2720
- P2721
- P2723
- P2724
- P2728
- P2729
- P2730
- P2761
- P2763
- P2764
- P2770
- P2771
- P279D
- P2810
- P2A00
- P2A01
- P2A03
- P2A04
- P3400
- P3401
- P3425
- P3441
- P3449
- U0001
- U0002
- U0073
- U0101
- U0104
- U0105
- U0106
- U0107
- U0111
- U0117
- U0120
- U0121
- U0122
- U0126
- U0131
- U0132
- U0134
- U0136
- U0140
- U0141
- U0151
- U0155
- U0156
- U0158
- U0160
- U0165
- U0170
- U0184
- U0194
- U0199
- U0200
- U0208
- U0209
- U0210
- U0214
- U0230
- U0232
- U0233
- U0236
- U0241
- U0249
- U0291
- U0293
- U0299
- U1000
- U1001
- U1016
- U1017
- U1024
- U1026
- U1040
- U1041
- U1064
- U1088
- U1092
- U1097
- U1098
- U1099
- U1111
- U1128
- U1129
- U1133
- U1136
- U1137
- U1144
- U1147
- U1153
- U1160
- U1161
- U1162
- U1166
- U1167
- U1173
- U1176
- U1177
- U1193
- U1254
- U1255
- U1300
- U1301
- U1305
- U1500
- U180F
- U1814
- U1842
- U1843
- U186A
- U186B
- U1881
- U1882
- U1883
- U1885
- U1886
- U1889
- U1890
- U1891
- U1892
- U1893
- U1894
- U1895
- U1896
- U1897
- U1899
- U18B9
- U18BF
- U2000
- U2001
- U2007
- U2099
- U2100
- U2101
- U2104
- U2105
- U2106
- U2107
- U2109
- U2111
- U2113
- U2116
- U2122
- U2125
- U2127
- U2137
- U2171
- U2172
- → P1320
- Chrysler DTC
- B00C5-95
- B1000
- B1003
- B1006
- B1009
- B101
- B1012
- B1015
- B102
- B1021
- B1024
- B1028
- B1029
- B102F
- B103
- B103
- B1031 Odpady
- B1032
- B1034
- B1035
- B1037
- B103D
- B103F
- B1040
- B1043
- B1044
- B1045
- B1052
- B1055
- B1056
- B1057
- B1058
- B105B
- B105C
- B105D
- B1084
- B1087
- B10A
- B10A5
- B10A6
- B10A7
- B10A8
- B10AC
- B10AD
- B10AF
- B10B2
- B10B4
- B10B5
- B10B8
- B10B9
- B113
- B1138
- B1139
- B113D
- B113F
- B1140
- B1141 smerom
- B1142
- B1143
- B1144
- B1145
- B1146
- B1147
- B114C
- B1151
- B1153
- B1154
- B1156
- B1157
- B11C3
- B11C4
- B11C9
- B11CA
- B11CC
- B11CD
- B11CF
- B11D0
- B11D3
- B11D5
- B11EA-92
- B11FE-11
- B123F
- B1267
- B1268
- B126B
- B126C
- B126F
- B1270
- B1273
- B1274
- B127A
- B1286
- B1287
- B1288
- B129C
- B140
- B140
- B1401
- B1402
- B1403
- B1404-13
- B1405
- B1406
- B1407
- B1408-12
- B1409
- B140B
- B140D
- B140F
- B142
- B142
- B1421
- B1423
- B1424
- B1427
- B1428
- B1429
- B142B
- B142D
- B142F
- B143
- B1430
- B1431
- B143B
- B143C
- B143F
- B1440
- B1441
- B1442
- B1448
- B1460
- B1461
- B1462
- B1463
- B1464
- B1465
- B1466
- B1467
- B1468
- B1469
- B146A
- B146B
- B146C
- B146E
- B146F
- B1470
- B1471
- B1472
- B1474
- B1475
- B1476
- B1477
- B1478
- B147A
- B147B
- B147C
- B147D
- B147E
- B147F
- B1480
- B1481
- B1482
- B1483
- B1484
- B1485
- B1486
- B1487
- B1488
- B1492
- B14B7
- B14B8
- B14B9
- B14BA
- B14BB
- B14BC
- B14BD
- B14C2
- B14C3
- B14C3-11
- B14C4
- B14C5
- B14C6
- B14C7
- B14CE
- B14DF
- B14E0
- B1502
- B1503
- B1504
- B153F
- B1540
- B1541
- B1542
- B1543
- B1544
- B1545
- B1546
- B156B
- B156D
- B156F
- B157B
- B157C
- B157E
- B160
- B1601
- B1602
- B1604
- B1605
- B1607
- B1608
- B160B
- B1610
- B1611
- B1612
- B162B
- B162C
- B162F
- B1630
- B1633
- B1634
- B1637
- B1638
- B163B
- B163C
- B163F
- B1640
- B1643
- B1647
- B1648
- B164B
- B164F
- B1659
- B1660
- B1663
- B1664
- B1673
- B1674
- B1677
- B1678
- B167D
- B1681
- B1684
- B1685
- B1689
- B168F
- B16A
- B16A4
- B16A5
- B16A7
- B16A9
- B16B1
- B16B5
- B16F8
- B16F9
- B16FD
- B1788
- B1789
- B17B8
- B17B9
- B17BF
- B17C4
- B17E3
- B17E6
- B17E9
- B17EA
- B17FB
- B1801
- B1803
- B1806
- B1808
- B1820
- B1840
- B1843
- B1846
- B1849
- B1854
- B1856
- B1858
- B185D
- B185F
- B1861
- B1863
- B186F
- B1870
- B1883
- B1888
- B1889
- B188D
- B188E
- B188F
- B1891
- B1892
- B1893
- B18B5
- B18B6
- B18B8
- B18DE
- B18E0
- B18E3
- B18E4
- B18E5
- B1927
- B1928
- B1929
- B192B
- B192C
- B192D
- B1934
- B1935
- B193B
- B193C
- B193F
- B1940
- B1942
- B1947
- B194B
- B194C
- B194D
- B194F
- B1952
- B1953
- B1954
- B1955
- B1956
- B1958
- B1959
- B1961
- B1963
- B1965
- B1966
- B1967
- B1968
- B1969
- B196A
- B196B
- B196C
- B196D
- B196E
- B196F
- B1970
- B1971
- B1972
- B1973
- B1974
- B1975
- B1976
- B1977
- B1978
- B1979
- B198
- B198
- B1980
- B1981
- B1985
- B1986
- B1988
- B198B
- B198F
- B1991
- B1992
- B1994
- B1998
- B199C
- B19A0
- B19A4
- B19A5
- B19A6
- B19A8
- B19A9
- B19AA
- B19AD
- B19AE
- B19B0
- B19B1
- B19B2
- B19B7
- B19B8
- B19BA
- B19BC
- B19BD
- B19BF
- B19C0
- B19C2
- B19C3
- B19C4
- B19C5
- B19CD
- B19CE
- B19CF
- B19D0
- B19D1
- B19D2
- B19D3
- B19DB
- B19E0
- B19E3
- B19E5
- B19E7
- B19E8
- B19E9
- B19EB
- B19EC
- B19ED
- B19EF
- B19F0
- B19F1
- B19F3
- B19F4
- B19F5
- B19F7
- B19F9
- B19FB
- B1A08
- B1A09
- B1A0A
- B1A0B
- B1A0C
- B1A0D
- B1A0E
- B1A0F
- B1A10
- B1A11
- B1A12
- B1A13
- B1A14
- B1A15
- B1A17
- B1A20
- B1A24
- B1A25
- B1A26
- B1A27
- B1A28
- B1A29
- B1A35
- B1A37
- B1A38
- B1A3A
- B1A3B
- B1A3C
- B1A3D
- B1A3E
- B1A3F
- B1A41
- B1A42
- B1A43
- B1A44
- B1A45
- B1A46
- B1A47
- B1A68
- B1A6B
- B1A6C
- B1A77
- B1A79
- B1A7F
- B1A80
- B1A81
- B1A89
- B1A8A
- B1B54
- B1BA5
- B1BB9
- B1BC7
- B1BD3
- B1D07
- B1D09
- B1D0C
- B1D0D
- B1D0F
- B1D10
- B1D12
- B1D15
- B1D16
- B1D18
- B1D19
- B1D1F
- B1D23
- B1D2B
- B1D2F
- B1D33
- B1D34
- B1D37
- B1D4D
- B1D4F
- B1D5B
- B1D7B
- B1D7F
- B1D83
- B1D87
- B1D93
- B1D97
- B1D9C
- B1DF2
- B1E24
- B1E25
- B1E28
- B1E29
- B1E2A
- B1E2B
- B1E2E
- B1E2F
- B1E30
- B1E31
- B1E34
- B1E35
- B1E37
- B1E3D
- B1E3E
- B1E3F
- B1E40
- B1E41
- B1E44
- B1E45
- B1E46
- B1E49
- B1E4A
- B1E4B
- B1E4D
- B1E4E
- B1E4F
- B1E50
- B1E52
- B1E53
- B1E54
- B1E5F
- B1E60
- B1E61
- B1E62
- B1E63
- B1E64
- B1E65
- B1E67
- B1E68
- B1E6B
- B1E6C
- B1E95
- B1E96
- B1EB6
- B1EB7
- B210
- B210
- B2101
- B2102
- B210B
- B210D
- B2125
- B2142
- B2193
- B219A
- B219F
- B21A1
- B21FB
- B21FC
- B2204
- B2205
- B2206
- B2207
- B2208
- B220B
- B2211
- B2213
- B2214
- B2215
- B2216
- B221A
- B221D
- B221E
- B2223
- B2224
- B2225
- B2227
- B222A
- B222B
- B222D
- B222E
- B222F
- B223
- B2232
- B223B
- B223C
- B224
- B225
- B2254
- B2255
- B225C
- B225D
- B2260
- B2267
- B226F
- B2271
- B2272
- B2273
- B2274
- B2283
- B2286
- B2290
- B229B
- B22A2
- B22A4
- B22A5
- B22A6
- B22A8
- B22A9
- B230
- B2301
- B2304
- B2305
- B2307
- B230D
- B2323
- b2324
- B2339
- B235A
- B238E
- B2390
- B2394
- B23AA
- B250
- B250
- B2500
- B2501
- B2502
- B2503
- B2504
- B2506
- B2507
- B2508
- B2509
- B250B
- B250C
- B250D
- B250F
- B2510
- B2511
- B2512
- B2513
- B2562
- B2563
- B2577
- B2578
- B2580
- B2581
- B2599
- B259A
- B25A3
- B25A4
- B25AC
- B25AD
- B2722
- B2731-11
- B2738-95
- B273F
- B275B
- B2760
- B2761
- B2762
- B2764
- B2765
- B2767
- B2768
- B276A
- B2776
- B2777
- B280B
- B2817
- B2818
- B2846
- B2847
- B2849
- B284A
- B2854
- B285C
- B285D
- C0077
- C008
- C008F
- C1008
- C1078
- C121
- C1219
- C121C
- C1239
- C1240
- C1241
- C127A
- C140
- C1456
- C1457
- C145D
- C1464
- C1465
- C1477
- C147A
- C147B
- C147C
- C14A3
- C14A4
- C14A5
- C1501
- C1502
- C1503
- C1504
- C1504-96
- C151D
- C1570
- C157A
- C157B
- C157D
- C157F
- C1581
- C1597
- C15B7-13
- C15C1
- C15D6
- C15D8
- C15DB
- C2100
- C2101
- C2102
- C2103
- C2111
- C2112
- C2202
- C2205
- C2206
- C2209
- C220B
- C220C
- C2212
- C2217
- C221C
- C2223
- C2225
- C2226
- C2227
- P000
- P000C
- P000D
- P0010
- P0013
- P0014
- P0016
- P0017
- P0018
- P0019
- P0020
- P0023
- P0030
- P0031
- P0032
- P0036
- P0037
- P0040
- P0050
- P0051
- P0052
- P0056
- P0057
- P0058
- P0062
- P0068
- P0069
- P0070
- P0071
- P0072
- P0073
- P0101
- P0102
- P0103
- P0106
- P0107
- P0108
- P0110
- P0111
- P0112
- P0116
- P0120
- P0121
- P0124
- P0125
- P0128
- P0129
- P0130
- P0131
- P0132
- P0133
- P0134
- P0135
- P0138
- P013A
- P013C
- P0140
- P0141
- P0150
- P0151
- P0152
- P0153
- P0154
- P0155
- P0156
- P0160
- P0161
- P0171
- P0172
- P0173
- P0174
- P0179
- P0181
- P0182
- P0196
- P0197
- P0198
- P0200
- P0201
- P0202
- P0205
- P0207
- P0208
- P0218
- P0221
- P0222
- P023
- P023C
- P0243
- P0261
- P0262
- P0265
- P0300
- P0301
- P0302
- P0303
- P0304
- P0305
- P0306
- P0307
- P0308
- P0309
- P0310
- P0315
- P0320
- P0325
- P0330
- P0335
- P0336
- P0339
- P0340
- P0341
- P0344
- P0345
- P0349
- P0351
- P0352
- P0353
- P0355
- P0356
- P0365
- P0369
- P0390
- P0394
- P0400
- P0401
- P0403
- P0404
- P0405
- P0406
- P0410
- P0412
- P0418
- P0420
- P0421
- P0422
- P0430
- P0431
- P0432
- P0441
- P0443
- P0444
- P0445
- P0446
- P0450
- P0451
- P0452
- P0455
- P0456
- P0457
- P0458
- P0459
- P0460
- P0461
- P0462
- P0463
- P0480
- P0498
- P0499
- P050
- P0500
- P0503
- P0505
- P0506
- P0507
- P0508
- P0509
- P050B
- P050D
- P0513
- P0516
- P0517
- P0519
- P0520
- P0521
- P0522
- P0523
- P0532
- P0533
- P054A
- P054C
- P0551
- P0554
- P0561
- P0562
- P0563
- P0571
- P0572
- P0573
- P0579
- P0580
- P0581
- P0582
- P0585
- P0586
- P058C
- P0591
- P0592
- P0593
- P0594
- P060
- P060
- P0600
- P0601
- P0602
- P0603
- P0604
- P0605
- P0606
- P0607
- P060B
- P060D
- P060F
- P0613
- P061A
- P061B
- P061C
- P0622
- P0625
- P0626
- P0627
- P0628
- P0629
- P062C
- P062F
- P0630
- P0632
- P0633
- P0634
- P063A
- P0642
- P0645
- P0646
- P0647
- P0652
- P0653
- P0657
- P0659
- P0660
- P0666
- P0667
- P0668
- P0669
- P0685
- P0686
- P0687
- P0688
- P0690
- P0691
- P0692
- P0693
- P0694
- P06AB
- P06AC
- P06AD
- P06AE
- P06DA
- P06DD
- P06DE
- P0702
- P0703
- P0705
- P0706
- P0710
- P0711
- P0712
- P0713
- P0714
- P0715
- P0716
- P0717
- P0719
- P0720
- P0721
- P0724
- P0725
- P0729
- P0730
- P0731
- P0732
- P0733
- P0734
- P0735
- P0736
- P0740
- P0742
- P0743
- P0748
- P0750
- P0751
- P0752
- P0753
- P0755
- P0757
- P0758
- P075A
- P0760
- P0763
- P0765
- P076F
- P0770
- P0778
- P077C
- P077D
- P077E
- P0781
- P0791
- P0792
- P07BF
- P07C0
- P07D9
- P0814
- P081C
- P083A
- P083B
- P0841
- P0845
- P0846
- P084B-DC
- P0850
- P0868
- P0869
- P0870
- P0871
- P0875
- P0876
- P0882
- P0883
- P0884
- P0888
- P0890
- P0891
- P0897
- P0919
- P093
- P0932
- P0933
- P0934
- P0935
- P093B
- P093C
- P0944
- P0951
- P0952
- P0953
- P0957
- P0960
- P0961
- P0962
- P0963
- P0972
- P0973
- P0974
- P0975
- P0976
- P0977
- P0978
- P0979
- P0980
- P0981
- P0982
- P0983
- P0985
- P0986
- P0987
- P0988
- P0992
- P1004
- P1005
- P1009
- P1106
- P1115
- P1128
- P1129
- P113
- P1135
- P1136
- P113D
- P1188
- P1189
- P1190
- P1192
- P1193
- P1194
- P1195
- P1196
- P121B
- P1239
- P1273
- P1275
- P1282
- P1288
- P1289
- P129
- P1294
- P1295
- P1296
- P1297
- P1299
- P1300
- P1386
- P1388
- P1389
- P1391
- P1398
- P1404
- P1414
- P1416
- P1417
- P1456
- P1457
- P1478
- P1479
- P1486
- P1487
- P1489
- P1490
- P1491
- P1492
- P1493
- P1494
- P1495
- P1496
- P1497
- P1498
- P1500
- P1501
- P1502
- P150D
- P1521
- P1524
- P1530
- P1572
- P1573
- P1593
- P1594
- P1595
- P1596
- P1597
- P1598
- P1599
- P1600
- P1601
- P1602
- P1603
- P1604
- P1610
- P1612
- P1614
- P1616
- P1617
- P1618
- P1621
- P1622
- P1626
- P1627
- P1634
- P1652
- P1653
- P1654
- P1656
- P1666
- P167
- P1681
- P1682
- P1683
- P1684
- P1685
- P1686
- P1687
- P1694
- P1696
- P1697
- P1698
- P1713
- P1714
- P1715
- P1716
- P1717
- P1718
- P1719
- P1731
- P1736
- P1738
- P1739
- P1741
- P1745
- P1751
- P1768
- P1771
- P1776
- P1781
- P1782
- P1784
- P1787
- P1788
- P1789
- P1790
- P1791
- P1792E
- P1793
- P1794
- P1795
- P1796
- P1797
- P1798
- P1799
- P1854
- P1861
- P1897
- P1899
- P1915
- P1B13
- P1B14
- P1C4E
- P1CF3
- P1CF4
- P1D20
- P1D25
- P1D77
- P1D78
- P1D79
- P1D8A
- P1D8B
- P1D8C
- P1D8D
- P1D8E
- P1D8F
- P1D90
- P1D92
- P1D93
- P1D94
- P1D95
- P1D96
- P1D97
- P1D98
- P1D99
- P1D9A
- P1D9B
- P1D9C
- P1D9D
- P1D9E
- P1D9F
- P1DA1
- P1DA2
- P1DA3
- P1DA4
- P1DA5
- P1DA6
- P1DA7
- P1DA8
- P1DA9
- P1DAA
- P1DAB
- P1DAC
- P1DAD
- P1DAE
- P1DAF
- P1DB0
- P1DB1
- P1DB2
- P1DB3
- P1DB4
- P1DB5
- P1DB6
- P1DB7
- P1DB8
- P1DB9
- P1DC6
- P1DC7
- P1DC8
- P1DCA
- P1DCD
- P1DCE
- P1DCF
- P1DD0
- P1DD1
- P1DDC
- P1DDD
- P1DDE
- P1DEB
- P1DF3
- P1DF7
- P1DF8
- P1DF9
- P1DFA
- P1E09
- P1E0A
- P2008
- P2009
- P2010
- P2016
- P2017
- P2066
- P2067
- P2068
- P2072
- P2074
- P2077
- P2078
- P2096
- P2097
- P2098
- P2099
- P2100
- P2101
- P2106
- P2108
- P2110
- P2111
- P2112
- P2115
- P2116
- P2118
- P2122
- P2123
- P2127
- P2128
- P2135
- P2138
- P215C
- P2161
- P2166
- P2167
- P2172
- P2173
- P2174
- P2175
- P2181
- P219A
- P219B
- P2228
- P2229
- P2263
- P2271
- P2273
- P2299
- P2300
- P2302
- P2303
- P2304
- P2305
- P2308
- P2311
- P2314
- P2317
- P232
- P2320
- P2323
- P2431
- P2432
- P2433
- P2448
- P2503
- P2504
- P2513
- P2533
- P2545
- P2561
- P258A
- P258B
- P2610
- P2700
- P2701
- P2702
- P2703
- P2704
- P2706
- P273
- P273B
- P2762
- P2763
- P2764
- P3400
- P3401
- P3402
- P3425
- P3426
- P3441
- P3442
- P3449
- P3450
- P3497
- U0001
- U0002
- U0009
- U0010
- U0011
- U0013
- U0014
- U0016
- U0017
- u0020
- U0021
- u0022
- U0023
- U0024
- U0025
- u0026
- U0027
- U0037
- U0100
- U0101
- U0102
- U0103
- U0104
- U0110
- U0114
- U0121
- U0125
- U0126
- U0127
- U0128
- U0129
- U0131
- U0132
- U0139
- U0140
- U0141
- U0143
- U0146
- U0147
- U0151
- U0154
- U0155
- U0156
- U0159
- U0161
- U0164
- U0167
- U0168
- U0169
- U0170
- U0171
- U0181
- U0182
- U0184
- U0186
- U0187
- U0195
- U0196
- U0197
- U0199
- U0200
- U0201
- U0202
- U0203
- U0204
- U0208
- U0209
- U0212
- U0213
- U0230
- U0231
- U0232
- U0236
- U0241
- U0246
- U0249
- U0250
- U0259
- U0264
- U0401
- U0402
- U0403
- U0405
- U0415
- U0420
- U0421
- U0422
- U0423
- U0424
- U0428
- U0429
- U0430
- U0431
- U0432
- U0452
- U045A
- U0485
- U0487
- U049A
- U0501
- U0531
- U0594
- U1008
- U1009
- U1015
- U103A
- U103C
- U1045
- U110
- U110
- U1101
- U1108
- U1109
- U110C
- U110D
- U110F
- U1110
- U1113
- U1120
- U112B
- U112D
- U113D
- U113E
- U113F
- U1140
- U1141
- U1143
- U1144
- U1145
- U1147
- U1148
- U1149
- U1158
- U1175
- U1176
- U1186
- U1190
- U1197
- U119E
- U119F
- U11A0
- U11A2
- U11B8
- U11B9
- U11BB
- U11BC
- U11C2
- U11C3
- U11DE
- U11E3
- U11E4
- U11E8
- U11EA
- U11EB
- U11ED
- U11EE
- U11F0
- U11F1
- U11FA
- U11FB
- U120
- U120C
- U1213A
- U1214
- U1215
- U1216
- U121E
- U1267
- U12A7
- U12AE
- U140
- U1401
- U1403
- U1411
- U1412
- U1414
- U1415
- U1416
- U1417
- U1418
- U141E
- U142
- U1424
- U1430
- U1431
- U1445
- U1446
- U1447
- U1450
- U1454
- U145D
- U145E
- U1461
- U1464
- U1465
- U1466
- U1467
- U1469
- U1477
- U1479
- U147D
- U147E
- U1480
- U1489
- U148D
- Citroen DTC
- Dacia DTC
- Daewoo DTC
- P0106
- P0107
- P0108
- P0112
- P0113
- P0117
- P0118
- P0121
- P0122
- P0123
- P0125
- P0128
- P0131
- P0132
- P0133
- P0134
- P0137
- P0138
- P0140
- P0141
- P0171
- P0172
- P0201
- P0202
- P0203
- P0204
- P0218
- P0300
- P0301
- P0302
- P0303
- P0304
- P0325
- P0327
- P0336
- P0337
- P0341
- P0342
- P0351
- P0352
- P0401
- P0402
- P0404
- P0405
- P0406
- P0420
- P0440
- P0442
- P0443
- P0446
- P0449
- P0452
- P0453
- P0461
- P0462
- P0463
- P0464
- P0480
- P0481
- P0502
- P0506
- P0507
- P0532
- P0533
- P0560
- P0562
- P0563
- P0601
- P0700
- P0711
- P0712
- P0713
- P0716
- P0717
- P0719
- P0722
- P0723
- P0724
- P0730
- P0741
- P0742
- P0748
- P0751
- P0753
- P0756
- P0758
- P1106
- P1107
- P1109
- P1111
- P1112
- P1114
- P1115
- P1121
- P1122
- P1130
- P1133
- P1134
- P1171
- P1336
- P1380
- P1381
- P1391
- P1392
- P1393
- P1404
- P1441
- P1508
- P1509
- P1520
- P1546
- P1618
- P1625
- P1640
- P1781
- P1782
- P1790
- P1792E
- P1810
- P1811
- P1877
- P1895
- Daihatsu DTC
- Dodge DTC
- B0002-2B
- B0004-13
- B0028-13
- B0050-13
- B007-9A
- B0070-95
- B007F-13
- B0090-95
- B1000
- B1003
- B1006
- B1009
- B101
- B1012
- B1021
- B1028
- B1029
- B102F
- B103
- B103
- B1030-11
- B1031 Odpady
- B1032
- B1034
- B1035
- B1037
- B103D
- B103F
- B1040
- B1043
- B1044
- B1045
- B1052
- B1055
- B1056
- B1057
- B1058
- B1058-2B
- B105B
- B105C
- B106-11
- B1084
- B1087
- B10A
- B10A5
- B10A6
- B10A7
- B10A8
- B10AC
- B10AD
- B10B2
- B10B4
- B10B5
- B10B8
- B10B9
- B113
- B1139
- B113D
- B113F
- B1140
- B1141 smerom
- B1142
- B1142-92
- B1143
- B1145
- B1146
- B1147
- B114C
- B1151
- B1153
- B1154
- B1156
- B1157
- B11C4
- B11C9
- B11CA
- B11CB-92
- B11CC
- B11CD
- B11CF
- B11D0
- B11D3
- B11D5
- B123F
- B1267
- B1268
- B126B
- B126C
- B126F
- B1270
- B1273
- B1274
- B127A
- B1286
- B1287
- B1288
- B128E-25
- B1290-25
- B1295-92
- B1297-25
- B1297-92
- B129C
- B140
- B140
- B1401
- B1402
- B1403
- B1405
- B1406
- B1407
- B1409
- B140B
- B140D
- B140F
- B142
- B142
- B1421
- B1423
- B1427
- B1428
- B1429
- B142B
- B142D
- B142F
- B1430
- B1431
- B143B
- B143C
- B143F
- B1440
- B1441
- B1446
- B1448
- B1460
- B1461
- B1462
- B1463
- B1464
- B1465
- B1466
- B1467
- B1468
- B1469
- B146A
- B146B
- B146C
- B146D
- B146E
- B146F
- B1470
- B1471
- B1472
- B1473
- B1474
- B1474-11
- B1475
- B1476
- B1477
- B1478
- B1479
- B147A
- B147B
- B147C
- B147D
- B147E
- B147F
- B1480
- B1482
- B1483
- B1483-92
- B1484
- B1485
- B1486
- B1487
- B1488
- B1492
- B14B7
- B14B8
- B14B9-11
- B14BA
- B14BB
- B14BC
- B14BD
- B14BE-13
- B14BF
- B14C0
- B14C1
- B14C2
- B14C3
- B14C4
- B14C5
- B14C6
- B14C7
- B14CE
- B14CF
- B14DF
- B14E0
- B1502
- B1503
- B1504
- B153F
- B1540
- B1541
- B1542
- B1543
- B1544
- B1545
- B1546
- B1560-13
- B156D
- B156F
- B1570-19
- B1579-12
- B157B
- B157C
- B157E
- B160
- B1601
- B1602
- B1604
- B1605
- B1607
- B1608
- B160B
- B1610
- B1611
- B1612
- B162B
- B162C
- B162F
- B1630
- B1633
- B1634
- B1637
- B1638
- B163B
- B163C
- B163F
- B1640
- B1643
- B1644
- B1647
- B1648
- B164B
- B164F
- B1659
- B1660
- B1663
- B1664
- B1673
- B1674
- B1677
- B1678
- B168F
- B1692-12
- B16A
- B16A4
- B16A5
- B16A7
- B16A8
- B16A9
- B16B1
- B16B5
- B16BF-15
- B16C3-15
- B16F8
- B16F9
- B16FC
- B16FD
- B177B-11
- B1788
- B17B8
- B17B9
- B17BF
- B17C4
- B17E3
- B17E5
- B17E6
- B17E9
- B17EA
- B17F3
- B17FB
- B1801
- B1803
- B1806
- B1808
- B180F-11
- B1818-12
- B181E-13
- B1820
- B1840
- B1843
- B1846
- B1849
- B1854
- B1856
- B1858
- B185D
- B185F
- B1861
- B1863
- B186F
- B1883
- B1888
- B1889
- B188D
- B188E
- B188F
- B1891
- B1893
- B18B5
- B18B6
- B18B7
- B18B8
- B18DE
- B18E0
- B18E3
- B18E4
- B18E5
- B1927
- B1928
- B1929
- B192B
- B192C
- B192D
- B1934
- B1935
- B193B
- B193C
- B193F
- B1940
- B1942
- B1947
- B1948
- B194B
- B194C
- B194D
- B194F
- B1952
- B1953
- B1954
- B1955
- B1956
- B1958
- B1959
- B1961
- B1963
- B1965
- B1966
- B1967
- B1968
- B1969
- B196A
- B196B
- B196C
- B196D
- B196E
- B196F
- B1970
- B1971
- B1973
- B1974
- B1975
- B1976
- B1977
- B1978
- B1979
- B197A
- B1980
- B1981
- B1982
- B1984
- B1985
- B1986
- B1987
- B1988
- B198B
- B198F
- B1991
- B1992
- B1994
- B1998
- B199C
- B19A0
- B19A4
- B19A5
- B19A6
- B19A8
- B19A9
- B19AA
- B19AC
- B19AD
- B19AE
- B19B0
- B19B1
- B19B2
- B19B3-11
- B19B7
- B19B8
- B19BA
- B19BC
- B19BD
- B19BF
- B19C0
- B19C1
- B19C2
- B19C3
- B19C4
- B19CD
- B19CE
- B19CF
- B19D0
- B19D1
- B19D2
- B19D3
- B19DB
- B19DE
- B19E0
- B19E3
- B19E5
- B19E7
- B19E8
- B19E9
- B19EB
- B19EC
- B19ED
- B19EF
- B19F0
- B19F1
- B19F3
- B19F4
- B19F5
- B19F9
- B19FB
- B19FD
- B1A08
- B1A09
- B1A0A
- B1A0B
- B1A0C
- B1A0D
- B1A0E
- B1A0F
- B1A10
- B1A11
- B1A12
- B1A13
- B1A14
- B1A15
- B1A16
- B1A17
- B1A20
- B1A24
- B1A25
- B1A26
- B1A27
- B1A28
- B1A29
- B1A35
- B1A37
- B1A38
- B1A3A
- B1A3B
- B1A3C
- B1A3D
- B1A3E
- B1A3F
- B1A42
- B1A43
- B1A44
- B1A45
- B1A46
- B1A47
- B1A68
- B1A6B
- B1A6C
- B1A77
- B1A79
- B1A80
- B1A8A
- B1B54
- B1BA5
- B1BB9
- B1BC7
- B1BD3
- B1D07
- B1D0C
- B1D0D
- B1D0F
- B1D10
- B1D12
- B1D15
- B1D16
- B1D18
- B1D19
- B1D1F
- B1D23
- B1D2B
- B1D2F
- B1D33
- B1D34
- B1D37
- B1D38
- B1D4D
- B1D4F
- B1D77-12
- B1D7B
- B1D7F
- B1D87
- B1D93
- B1D97
- B1D9C
- B1DF2
- B1E11-11
- B1E24
- B1E25
- B1E28
- B1E29
- B1E2A
- B1E2B
- B1E2E
- B1E2F
- B1E30
- B1E34
- B1E36
- B1E37
- B1E3D
- B1E3E
- B1E3F
- B1E40
- B1E41
- B1E44
- B1E45
- B1E46
- B1E49
- B1E4A
- B1E4B
- B1E4D
- B1E4E
- B1E4F
- B1E50
- B1E52
- B1E53
- B1E54
- B1E5F
- B1E60
- B1E61
- B1E62
- B1E63
- B1E64
- B1E65
- B1E67
- B1E68
- B1E6B
- B1E6C
- B1E95
- B1E96
- B1EB6
- B1EB7
- B1F02-12
- B1F03-13
- B1F06-12
- B210
- B210
- B2101
- B2102
- B2103-15
- B210D
- B212D-16
- B212D-17
- B2142
- B2193
- B219A
- B219F
- B21A1
- B21FB
- B21FC
- B2204
- B2205
- B2206
- B2207
- B2208
- B220B
- B2211
- B2213
- B2214
- B2215
- B2216
- B221A
- B221D
- B221E
- B221F
- B2224
- B2225
- B2227
- B222A
- B222B
- B222C
- B222D
- B222E
- B222F
- B223
- B2232
- B223B
- B223C
- B224
- B225
- B2254
- B2255
- B225C
- B2260
- B2267
- B226F
- B2271
- B2272
- B2273
- B2274
- B2283
- B2286
- B2299
- B229B
- B22A5
- B22A6
- B22A7
- B22A8
- B22A9
- B230
- B2301
- B2304
- B2305
- B2307
- B230D
- B2312-11
- B2312-15
- B232
- B2323
- b2324
- B2339
- B235A
- B238E
- B2390
- B2394
- B23AA
- B250
- B250
- B2500
- B2501
- B2502
- B2503
- B2504
- B2505
- B2506
- B2507
- B2508
- B2509
- B250B
- B250C
- B250D
- B250F
- B2510
- B2511
- B2512
- B2513
- B2562
- B2563
- B2577
- B2578
- B2580
- B2581
- B2598
- B2599
- B259A
- B259B
- B259F-11
- B25A3
- B25A4
- B25AC
- B25AD
- B2722
- B2736-49
- B273F
- B275B
- B2760
- B2761
- B2762
- B2762-49
- B2764
- B2765
- B2767
- B2767-11
- B2768
- B2768-49
- B276A
- B2776
- B2777
- B280B
- B2817
- B2818
- B2846
- B2847
- B2849
- B284A
- B2854
- B285C
- B285D
- B287B-12
- C0051-49
- C0077
- C008
- C008F
- C1008
- C1078
- C1086-4B
- C121
- C1219
- C1239
- C123F
- C1240
- C1241
- C124F
- C127A
- C140
- C1456
- C145D
- C1464
- C1465
- C1477
- C147A
- C147B
- C147C
- C1480
- C14A3
- C14A4
- C14A5
- C1501
- C1502-96
- C1503
- C1504
- C151C
- C151D
- C1570
- C157A
- C157B
- C157C
- C157D
- C157E
- C157F
- C1580
- C1581
- C1597
- C15B5-11
- C15B8-11
- C15BC-11
- C15BC-12
- C15BD-12
- C15C1
- C15D6
- C15D8
- C15DB
- C2100
- C2101
- C2102
- C2103
- C2111
- C2112
- C2201
- C2202
- C2205
- C2206
- C2209
- C220B
- C220C
- C2210
- C2212
- C2217
- C2219
- C221C
- C2223
- C2225
- C2227
- C2312
- P000
- P000B
- P000C
- P000D
- P0013
- P0014
- P0016
- P0017
- P0018
- P0019
- P0020
- P0023
- P0030
- P0031
- P0032
- P0033
- P0036
- P0037
- P0038
- P0043
- P0044
- P0050
- P0051
- P0052
- P0057
- P0058
- P0060
- P0062
- P0068
- P0069
- P0070
- P0070-15
- P0071
- P0072
- P0073
- P007B
- P007C
- P007D
- P0088
- P0096
- P0097
- P0098
- P00A1
- P00A2
- P00A3
- P00DF
- P00E0
- P00E1
- P00E9
- P00EA
- P00EB
- P00F8
- P00F9
- P00FA
- P00FB
- P0101
- P0102
- P0106
- P0108
- P0109
- P0110
- P0111
- P0112
- P0113
- P0116
- P0117
- P0118
- P0120
- P0121
- P0122
- P0123
- P0124
- P0125
- P0128
- P0129
- P012A
- P012B
- P012C
- P012D
- P0130
- P0132
- P0133
- P0134
- P0135
- P0136
- P0137
- P0138
- P013A
- P013C
- P0140
- P0141
- P0143
- P0144
- P0145
- P0147
- P0150
- P0151
- P0152
- P0154
- P0155
- P0157
- P0158
- P0159
- P0160
- P0161
- P0165
- P0168
- P0171
- P0172
- P0175
- P0176
- P0177
- P0179
- P0180
- P0181
- P0182
- P0183
- P018C
- P018D
- P0192
- P0193
- P0197
- P0198
- P0201
- P0202
- P0203
- P0204
- P0205
- P0206
- P0207
- P0208
- P0209
- P0210
- P0215
- P0216
- P0217
- P0219
- P0221
- P0222
- P0223
- P023
- P0230
- P0232
- P0234
- P0236
- P0237
- P0238
- P023B
- P023C
- P0243
- P025
- P0251
- P0252
- P0253
- P0254
- P025B
- P025C
- P025D
- P0261
- P0262
- P0264
- P0265
- P0267
- P0268
- P026E
- P0270
- P0271
- P0298
- P0299
- P0300
- P0301
- P0302
- P0303
- P0304
- P0305
- P0306
- P0307
- P0308
- P0309
- P0310
- P0320
- P0325
- P0335
- P0336
- P0337
- P0338
- P0339
- P0340
- P0341
- P0342
- P0343
- P0344
- P0345
- P0349
- P0350
- P0351
- P0352
- P0354
- P0355
- P0357
- P0358
- P0365
- P0369
- P0370
- P0380
- P0381
- P0382
- P0387
- P0388
- P0390
- P0394
- P0401
- P0403
- P0404
- P0405
- P0406
- P0410
- P0418
- P0420
- P0421
- P0430
- P0431
- P0432
- P0440
- P0441
- P0442
- P0443
- P0444
- P0445
- P0446
- P0450
- P0451
- P0452
- P0453
- P0455
- P0456
- P0457
- P0458
- P0459
- P0460
- P0461
- P0463
- P0477
- P0478
- P0480
- P0481
- P0483
- P0498
- P0499
- P04DB
- P050
- P0500
- P0503
- P0505
- P050B
- P050D
- P0513
- P0514
- P0516
- P0520
- P0523
- P0532
- P0541
- P054A
- P0575
- P0576
- P0577
- P0586
- P0587
- P058C
- P0592
- P0596
- P0605
- P0606
- P0614
- P061A
- P061B
- P061C
- P0625
- P0642
- P0657
- P0659
- P0667
- P0685
- P0688
- P0692
- P0698
- P06AB
- P0700
- P0703
- P0706
- P0710
- P0720
- P0730
- P0731
- P0732
- P0735
- P0763
- P0783
- P07C0
- P0820
- P0841
- P084A-DC
- P0850
- P0869
- P0875
- P0883
- P0884
- P0890
- P0930
- P0931
- P093C
- P0952
- P0960
- P0961
- P0962
- P0972
- P0979
- P0980
- P0982
- P0985
- P0988
- P1110
- P112
- P1135
- P1189
- P1197
- P1205
- P1206
- P1239
- P1286
- P1289
- P1290
- P1291
- P129C
- P1388
- P1417
- P1457
- P1478
- P1486
- P1490
- P1497
- P1499
- P1521
- P1601
- P1610
- P1616
- P1617
- P1629
- P1632
- P1637
- P1653
- P1656
- P1665
- P1681
- P1683
- P1684
- P1692
- P1693
- P1713
- P1715
- P1731
- P1736
- P1751
- P1756
- P1764
- P1768
- P1775
- P1789
- P1790
- P1794
- P1795
- P1B13
- P1B14
- P1CF3
- P1D79
- P1D83
- P1D8C
- P1D8E
- P1D8F
- P1D92
- P1D96
- P1D9F
- P1DA0
- P1DAB
- P1DAC
- P1DAD
- P1DAE
- P1DAF
- P1DB0
- P1DB1
- P1DB2
- P1DB3
- P1DB4
- P1DB5
- P1DB6
- P1DB7
- P1DB8
- P1DB9
- P1DC6
- P1DC7
- P1DC8
- P1DC9
- P1DCA
- P1DCD
- P1DCE
- P1DCF
- P1DD0
- P1DD1
- P1DD2
- P1DDC
- P1DDD
- P1DDE
- P1DEB
- P1DF3
- P1DF7
- P1DF9
- P1DFA
- P1E09
- P1E0A
- P2008
- P2016
- P2017
- P2066
- P2067
- P2068
- P2072
- P2074
- P2077
- P2078
- P2096
- P2098
- P2099
- P2100
- P2101
- P2106
- P2107
- P2108
- P2110
- P2111
- P2112
- P2115
- P2116
- P2118
- P2121
- P2122
- P2123
- P2127
- P2128
- P2138
- P2146
- P2149
- P215C
- P2161
- P2166
- P2167
- P2172
- P2173
- P2174
- P2175
- P2181
- P219A
- P219B
- P2226
- P2227
- P2228
- P2229
- P2237
- P2238
- P2239
- P2240
- P2241
- P2242
- P2244
- P2246
- P2247
- P2248
- P2249
- P2250
- P2251
- P2252
- P2253
- P2254
- P2255
- P2256
- P2266
- P2269
- P2271
- P2273
- P2299
- P2300
- P2301
- P2304
- P2305
- P2308
- P2311
- P2314
- P2317
- P232
- P2320
- P2323
- P2431
- P2432
- P2433
- P2448
- P2502
- P2504
- P2509
- P2533
- P258A
- P258B
- P2608
- P2609
- P2610
- P2620
- P2626
- P2627
- P2628
- P2629
- P2630
- P2631
- P2638
- P2700
- P2701
- P2702
- P2703
- P2704
- P2706
- P273
- P273B
- P2761
- P2762
- P2763
- P2764
- P2767
- P2769
- P2770
- P2775
- P2779
- P2783
- P2784
- P2A0A
- P2A0B
- P2A0C
- P2A0D
- P3032
- P3400
- P3401
- P3425
- P3426
- P3441
- P3442
- P3449
- P3450
- P3497
- U0001
- U0002
- U0009
- U0010
- U0011
- U0013
- U0014
- U0016
- U0017
- u0020
- U0021
- u0022
- U0023
- U0024
- U0025
- u0026
- U0027
- U0037
- U0064
- U0065
- U0074
- U0100
- U0101
- U0102
- U0103
- U0104
- U0109
- U0110
- U0114
- U0121
- U0125
- U0127
- U0128
- U0129
- U0131
- U0132
- U0140
- U0141
- U0143
- U0146
- U0147
- U0151
- U0154
- U0155
- U0156
- U0159
- U0161
- U0164
- U0167
- U0168
- U0169
- U0170
- U0171
- U0181
- U0184
- U0186
- U0187
- U0191
- U0195
- U0196
- U0197
- U0199
- U0200
- U0201
- U0202
- U0203
- U0204
- U0208
- U0209
- U0212
- U0213
- U0230
- U0231
- U0232
- U0236
- U0241
- U0249
- U0250
- U0259
- U0264
- U0293
- U02A9
- U0401
- U0402
- U0403
- U0404
- U0405
- U0412
- U0414
- U0415
- U0416
- U0418
- U0420
- U0421
- U0422
- U0423
- U0424
- U0428
- U0429
- U0431
- U0432
- U0452
- U045A
- U0485
- U0487
- U0531
- U0594
- U05AA
- U1008
- U1009
- U1015
- U103C
- U1045
- U110
- U110
- U1108
- U1109
- U110B
- U110C
- U110D
- U110F
- U1110
- U1113
- U1118
- U1119
- U1120
- U112D
- U113D
- U113E
- U113F
- U1140
- U1141
- U1143
- U1145
- U1147
- U1148
- U1149
- U114C
- U1158
- U1175
- U1176
- U1186
- U1190
- U1197
- U119E
- U119F
- U11A0
- U11A2
- U11B9
- U11BC
- U11C2
- U11C3
- U11DE
- U11E3
- U11E4
- U11E8
- U11EA
- U11EB
- U11ED
- U11EE
- U11F0
- U11F1
- U11F9
- U11FA
- U11FB
- U120
- U120C
- U1213A
- U1214
- U1215
- U1216
- U121E
- U1267
- U12A7
- U12AE
- U140
- U140
- U1400
- U1401
- U1402
- U1403
- U1404
- U1405
- U1406
- U1407
- U1408
- U1409
- U140B
- U140C
- U140D
- U140F
- U1410
- U1411
- U1414
- U1415
- U1416
- U1417
- U1418
- U142
- U1420
- U142B
- U142C
- U1430
- U1431
- U1440
- U1445
- U1446
- U1447
- U1450
- U1454
- U145D
- U145E
- U1461
- U1464
- U1465
- U1466
- U1477
- U1479
- U147D
- U147E
- U1480
- U1489
- U148D
- U1504
- U1505
- Fiat DTC
- B0004-01
- B0004-01
- B0004-11
- B0004-12
- B0004-1A
- B0004-1B
- B0050-01
- B0050-11
- B0050-12
- B0050-13
- B0050-1D
- B0052-01
- B0052-11
- B0052-12
- B0052-13
- B0052-1D
- B0099-00
- B00B5-01
- B00B5-11
- B00B5-12
- B00B5-1D
- B00C5-01
- B00C5-11
- B00C5-12
- B00C5-13
- B00C5-1D
- B00D5-12
- B00D5-14
- B00D6-12
- B00D6-14
- B0100-49
- B0101-16
- B0101-17
- B0103-01
- B0103-11
- B0103-12
- B0103-1A
- B0103-1B
- B0104-01
- B0104-11
- B0104-12
- B0104-1A
- B0104-1B
- B0105-01
- B0105-11
- B0105-12
- B0105-1A
- B0105-1B
- B0106-01
- B0106-11
- B0106-12
- B0106-1A
- B0106-1B
- B0107-01
- B0107-11
- B0107-12
- B0107-1A
- B0107-1B
- B0108-01
- B0108-11
- B0108-12
- B0108-1A
- B0108-1B
- B0109-01
- B0109-11
- B0109-12
- B0109-1A
- B0109-1B
- B010F-01
- B010F-11
- B010F-12
- B010F-1A
- B010F-1B
- B0110-01
- B0110-11
- B0110-12
- B0110-1A
- B0110-1B
- B0111-1C
- B0111-2F
- B0111-64
- B0111-96
- B0112-1C
- B0112-2F
- B0112-64
- B0112-96
- B0114-01
- B0114-11
- B0114-12
- B0114-1A
- B0114-1B
- B0115-01
- B0115-11
- B0115-12
- B0115-1A
- B0115-1B
- B0118-95
- B0119-00
- B100-15
- B100-18
- B100-19
- B100-64
- B1007-15
- B1007-18
- B1007-19
- B1007-21
- B1007-54
- B1008-12
- B1008-15
- B1008-18
- B1008-19
- B1008-21
- B1008-64
- B1009-15
- B1009-18
- B1009-19
- B1010-09
- B1010-64
- B1010-67
- B1010-71
- B1011-15
- B1011-18
- B1011-19
- B1011-64
- B1013-62
- B1014-86
- B1015-23
- B1015-67
- B1017-15
- B1017-19
- B1019-45
- B1019-46
- B1019-8F
- B1020-15
- B1020-19
- B1020-64
- B1021-01
- B1021-11
- B1021-12
- B1021-13
- B1022-01
- B1022-11
- B1022-12
- B1022-13
- B1022-15
- B1022-19
- B1022-64
- B1023-01
- B1023-09
- B1023-11
- B1023-12
- B1023-13
- B1023-15
- B1023-19
- B1024-01
- B1024-11
- B1024-12
- B1024-13
- B1024-64
- B1025-01
- B1025-11
- B1025-12
- B1025-13
- B1025-64
- B1030-19
- B1031-01
- B1032-19
- B1032-31
- B1033-19
- B1033-64
- B1034-64
- B1035-01
- B1035-71
- B1036-12
- B1036-14
- B1039-19
- B104-15
- B104-19
- B1040-12
- B1040-13
- B1040-19
- B1040-64
- B1041-13
- B1041-16
- B1041-17
- B1041-19
- B1042-42
- B1045-01
- B1046-01
- B1048-12
- B1049-14
- B104D
- B105-64
- B1050-15
- B1051-15
- B1051-19
- B1051-55
- B1052-13
- B1052-15
- B1053-15
- B1053-64
- B1054-11
- B1054-13
- B1054-62
- B1054-67
- B1054-86
- B105B-64
- B105D-64
- B105F-64
- B106-11
- B106-19
- B1061-19
- B1062-11
- B1063-00
- B1064-13
- B1066-13
- B106B-11
- B106B-19
- B106C-11
- B106C-12
- B106C-13
- B106C-64
- B106D-86
- B106D-87
- B1071-19
- B1077-01
- B1078-15
- B107B-11
- B107B-13
- B1080-64
- B1080-86
- B1081-86
- B1082
- B1083-23
- B1085-18
- B1086-87
- B10A-4A
- B10C4-11
- B10C4-12
- B10C4-13
- B10E9
- B10EA
- B110-15
- B110-18
- B110-19
- B1100-68
- B1101-72
- B1101-73
- B1104-24
- B1105-86
- B1106-64
- B1107-15
- B1107-18
- B1107-19
- B1108-15
- B1108-18
- B1108-19
- B1109-15
- B1109-18
- B1109-19
- B110F-15
- B110F-19
- B1110-15
- B1110-19
- B1112-18
- B1112-19
- B1118-15
- B1118-19
- B112C-13
- B112C-19
- B1139-19
- B1161-64
- B1164-71
- B1166-71
- B116D-11
- B116D-19
- B11C1-13
- B1239-19
- B1265-23
- B1265-24
- B1267-23
- B1267-24
- B1268-23
- B1268-24
- B1269-23
- B1269-24
- B126A-23
- B126A-24
- B12AC-11
- B12AC-13
- B12AD-11
- B12AD-15
- B12D3-19
- B13D3-11
- B13D3-13
- B13D4-11
- B13D4-12
- B13D4-13
- B1400-11
- B1400-1A
- B1400-92
- B1401-11
- B1401-12
- B1401-13
- B1401-1A
- B1401-92
- B1402-11
- B1402-12
- B1402-13
- B1402-1A
- B1402-92
- B1403-11
- B1403-12
- B1403-13
- B1403-1A
- B1403-92
- B1404-11
- B1404-12
- B1404-13
- B1404-1A
- B1404-92
- B1405-11
- B1405-12
- B1405-13
- B1405-1A
- B1405-92
- B1406-11
- B1406-12
- B1406-13
- B1406-1A
- B1406-92
- B1407-11
- B1407-12
- B1407-13
- B1407-1A
- B1407-92
- B1408-11
- B1408-12
- B1408-13
- B1408-1A
- B1408-49
- B1408-92
- B1409-98
- B140C-11
- B140C-12
- B140C-13
- B140C-1A
- B140C-92
- B1410-16
- B1410-17
- B1411-05
- B1414-09
- B142-4B
- B143-11
- B143-12
- B143-13
- B143-1A
- B143D-11
- B143D-12
- B143D-13
- B143D-1A
- B145E-01
- B145F-01
- B1460-01
- B1488
- B14DA-2A
- B1514-09
- B1552-2A
- B1553-2A
- B1560-11
- B1560-13
- B1562-11
- B1562-12
- B1562-13
- B1562-1A
- B156B-13
- B156B-1A
- B1570-19
- B1577-13
- B1578-13
- B1578-1A
- B1579-13
- B1579-1A
- B157A-13
- B157A-1A
- B157E
- B162-15
- B162-15
- B162-19
- B162-19
- B1632-15
- B1632-19
- B1636-15
- B1636-19
- B165A-68
- B1900-01
- B1901-11
- B1901-15
- B1902-11
- B1902-12
- B1902-77
- B1905-11
- B1905-15
- B1906-11
- B1906-12
- B1906-77
- B1907-11
- B1907-15
- B1908-11
- B1908-12
- B1908-77
- B1909-11
- B1909-12
- B1909-77
- B1910-11
- B1910-15
- B1911-11
- B1911-15
- B1912-11
- B1912-15
- B1913-11
- B1913-15
- B1914-11
- B1914-15
- B1915-11
- B1915-15
- B1916-11
- B1916-15
- B1917-11
- B1917-15
- B1919-11
- B1919-12
- B1919-14
- B1919-15
- B1919-1C
- B1923-42
- B1924-49
- B1926-11
- B1926-12
- B1931-11
- B1931-15
- B1932-11
- B1932-15
- B1933-11
- B1933-15
- B1935-11
- B1935-15
- B1A7D-23
- B1E99-11
- B1E99-12
- B1E99-13
- B1E99-1E
- B1E9A-11
- B1E9A-12
- B1E9A-13
- B1E9A-1E
- B1EB0-87
- B1EB1-1A
- B1EB1-1B
- B1EB2-1A
- B1EB2-1B
- B210-16
- B210-17
- B210B-17
- B210C-16
- B210C-17
- B2206
- B221E
- B221E-00
- B222C
- B222C-00
- B223B
- B223B-00
- B22AB-23
- B2734-01
- B2734-12
- B2734-13
- B2761-01
- B2761-11
- B2761-12
- B2764-01
- B2764-11
- B2764-12
- B280B
- C0010-01
- C0011-01
- C0014-01
- C0015-01
- C0018-01
- C0019-01
- C001C-01
- C001D-01
- C0020-49
- C003-01
- C003-29
- C003-4A
- C003-95
- C0030-29
- C0031-01
- C0031-29
- C0031-4A
- C0033-29
- C0034-01
- C0034-29
- C0034-4A
- C0036-29
- C0037-01
- C0037-29
- C0037-4A
- C0037-95
- C0039-29
- C003B-95
- C0047-01
- C0047-29
- C0047-62
- C0051-29
- C0051-54
- C0051-86
- C0052-86
- C006-29
- C006-54
- C0061
- C0061-09
- C0061-29
- C0061-64
- C0061-86
- C0062-09
- C0062-29
- C0062-64
- C0062-86
- C0063-09
- C0063-29
- C0063-64
- C0063-86
- C006C-4A
- C0075-86
- C0076-68
- C0077-87
- C0078-86
- C0501
- C0507
- C050D
- C0513
- C0546-00
- C100-11
- C100-12
- C100-14
- C100-15
- C100-29
- C100-4B
- C100-61
- C100-86
- C100-86
- C1000-44
- C1000-45
- C1000-46
- C1000-47
- C1000-68
- C1000-98
- C1001-12
- C1001-14
- C1001-29
- C1001-48
- C1001-49
- C1002-12
- C1002-14
- C1002-25
- C1002-29
- C1003-04
- C1003-12
- C1003-14
- C1003-29
- C1003-49
- C1003-86
- C1003-97
- C1004-12
- C1004-14
- C1004-16
- C1004-17
- C1004-29
- C1004-49
- C1005-02
- C1005-11
- C1005-12
- C1005-13
- C1005-68
- C1005-86
- C1006-01
- C1006-11
- C1006-12
- C1006-13
- C1006-64
- C1007-87
- C1008-54
- C1008-64
- C1009-09
- C100B-11
- C100B-12
- C100B-14
- C100B-15
- C100B-29
- C100B-4B
- C100B-86
- C100C-12
- C100C-14
- C100C-29
- C100C-86
- C100D-12
- C100D-14
- C100D-29
- C100D-86
- C100F-08
- C100F-86
- C100F-87
- C1010-86
- C1011-85
- C1012-85
- C1013-12
- C1013-14
- C1013-29
- C1013-49
- C1013-86
- C1014-12
- C1014-14
- C1014-29
- C1014-86
- C1015-12
- C1015-14
- C1015-29
- C1015-92
- C1016-12
- C1016-14
- C1016-29
- C1016-85
- C1017-1C
- C1017-86
- C1018-68
- C1019-68
- C1020-68
- C104-11
- C104-12
- C104-13
- C104B-11
- C104B-12
- C104B-13
- C104C-11
- C104C-12
- C104D-11
- C104D-12
- C104D-13
- C104F-64
- C105B-64
- C105C-64
- C105D-8F
- C106D-11
- C106D-12
- C106D-13
- C120-24
- C1200-16
- C1200-17
- C1200-1C
- C1200-1F
- C1201-16
- C1201-17
- C1202-01
- C1202-29
- C1205-01
- C1205-49
- C1206-01
- C1207-01
- C1208-01
- C1209-01
- C120C-24
- C1210-86
- C1211-49
- C1211-96
- C1212-49
- C1214-62
- C1214-87
- C1215-29
- C1215-86
- C1217-23
- C1217-24
- C1217-86
- C1218-4B
- C1219-16
- C1220-86
- C1221-86
- C1222-87
- C1230-51
- C1230-55
- C1240-86
- C1251-86
- C1252-86
- C1253-86
- C1254-86
- C1260-86
- C1261-55
- C1262-05
- C140-07
- C140-53
- C140-55
- C1400-01
- C1400-13
- C1400-86
- C1400-97
- C1401-86
- C1402-86
- C1403-01
- C1403-11
- C1403-13
- C1403-15
- C1403-86
- C1404-86
- C1405-01
- C1405-11
- C1405-13
- C1405-15
- C1405-86
- C1406-86
- C1407-19
- C1407-77
- C1407-86
- C1408-19
- C1408-77
- C1408-86
- C1409-07
- C1409-97
- C140B-05
- C140B-94
- C140C-04
- C140C-86
- C140D-54
- C140D-86
- C140F-53
- C141-49
- C141-64
- C1410-87
- C1411-49
- C1412-54
- C1413-86
- C1413-87
- C1414-87
- C1416-87
- C1417-78
- C1418-78
- C1419-64
- C141B-97
- C141C-86
- C141D-47
- C141F-96
- C1420-25
- C1420-64
- C1420-66
- C1421-64
- C1421-67
- C1422-49
- C1422-64
- C1422-66
- C1423-4B
- C1423-86
- C1424-4B
- C1424-64
- C1425-01
- C1425-45
- C1426-49
- C1426-86
- C1427-66
- C1427-68
- C1427-87
- C1428-68
- C1428-87
- C1429-66
- C1429-68
- C1429-86
- C1430-86
- C1430-87
- C1431-86
- C1432-86
- C1432-87
- C1433-86
- C1434-86
- C14A5-97
- C14AA-64
- C1501-07
- C1501-16
- C1501-64
- C1502-07
- C1502-16
- C1502-64
- C1503-07
- C1503-16
- C1503-64
- C1504-07
- C1504-16
- C1504-64
- C1510-54
- C1512-88
- C1597-53
- C15CB-51
- C2000-64
- C2001-64
- C2002-64
- C2006-16
- C2006-17
- C2010-16
- C2010-17
- C2020-01
- C2020-47
- C2020-48
- C2020-94
- C2030-42
- C2050-1C
- C2060-09
- C2070-09
- C2080-09
- C2080-64
- C2090-09
- C2100-04
- C2100-13
- C2100-14
- C2100-15
- C2120-04
- C2120-13
- C2120-14
- C2120-15
- C2150-98
- C2160-04
- C2180-98
- C2190-98
- C2200-04
- C2201-64
- C2202-64
- C2203-24
- C2204-24
- C2205-24
- C2206-64
- C2208-64
- C2209-64
- C221-64
- C2210-4B
- C2210-92
- C221B-64
- C221D-98
- C221F-64
- C2220-54
- C2224-64
- C2225-64
- C2226-64
- C2227-64
- C2228-64
- C2229-64
- C2230-98
- C2240-92
- C2250-78
- C2260-63
- C2270-77
- C2280-92
- C2290-92
- C2300-00
- C2400-55
- C2501-87
- C2502-64
- C2503-87
- C2504-87
- C2506-64
- C2507-64
- C2508-64
- C2509-64
- P0016
- P0031
- P0032
- P0033
- P0034
- P0035
- P0037
- P0038
- P0069
- P006C
- P006D
- P0071
- P0072
- P0073
- P0105
- P0106
- P0107
- P0108
- P0111
- P0112
- P0113
- P0114
- P0116
- P0117
- P0118
- P0119
- P0121
- P0122
- P0123
- P0125
- P0128
- P012B
- P0130
- P0131
- P0132
- P0133
- P0135
- P0137
- P0138
- P0139
- P0140
- P0141
- P0171
- P0172
- P0196
- P0197
- P0198
- P0199
- P0201
- P0202
- P0203
- P0204
- P0219
- P0221
- P0222
- P0223
- P0234
- P0237
- P0238
- P0243
- P0245
- P0246
- P0261
- P0262
- P0264
- P0265
- P0267
- P0268
- P0270
- P0271
- P0298
- P0299
- P0300
- P0301
- P0302
- P0303
- P0304
- P0315
- P0324
- P0325
- P0326
- P0327
- P0328
- P0335
- P0339
- P0340
- P0342
- P0343
- P0344
- P0351
- P0352
- P0353
- P0354
- P0420
- P0440
- P0441
- P0443
- P0444
- P0452
- P0455
- P0456
- P0457
- P0458
- P0459
- P0461
- P0462
- P0463
- P0480
- P0481
- P0498
- P0499
- P04DB
- P0500
- P0501
- P0503
- P0506
- P0507
- P050B
- P050D
- P0513
- P051C
- P051D
- P0520
- P0521
- P0522
- P0523
- P0532
- P0533
- P0562
- P0563
- P0564
- P0571
- P0572
- P0573
- P0579
- P0580
- P0581
- P0585
- P0591
- P0592
- P0593
- P060
- P060
- P0600
- P0601
- P0604
- P0605
- P0606
- P0607
- P060B
- P060C
- P060D
- P060F
- P0610
- P0613
- P0615
- P0616
- P0617
- P061A
- P061B
- P061C
- P0622
- P0625
- P0626
- P0627
- P0628
- P0629
- P062C
- P062F
- P0630
- P0631
- P0632
- P0633
- P0634
- P063A
- P0641
- P0642
- P0643
- P0645
- P0646
- P0647
- P064F
- P0651
- P0652
- P0653
- P0658
- P0659
- P0685
- P0686
- P0687
- P0688
- P0691
- P0692
- P0693
- P0694
- P0697
- P0701
- P0703
- P0706
- P0707
- P0711
- P0712
- P0713
- P0716
- P0721
- P0729
- P072F
- P0731
- P0732
- P0733
- P0734
- P0735
- P073E
- P076F
- P077C
- P077D
- P077E
- P079
- P07A7
- P07BF
- P07C0
- P07D9
- P07F6
- P080
- P0806
- P0807
- P0808
- P0810
- P0814
- P081C
- P0850
- P0885
- P0887
- P0914
- P0919
- P0928
- P0929
- P0933
- P0934
- P0935
- P0955
- P0960
- P0962
- P097
- P0973
- P0974
- P0975
- P0976
- P0978
- P0979
- P097B
- P097C
- P097D
- P0981
- P0982
- P0984
- P0985
- P0998
- P0999
- P099B
- P099C
- P101
- P101B
- P101C
- P101D
- P102
- P1021
- P1022
- P1023
- P1024
- P1025
- P1028
- P102B
- P102C
- P103
- P1031
- P1033
- P1034
- P1037
- P1039
- P103B
- P103C
- P103F
- P1043
- P1045
- P1046
- P1047
- P1049
- P104B
- P1063
- P1067
- P106B
- P1115
- P112
- P112B
- P113D
- P1185
- P1300
- P1456
- P1457
- P1489
- P1500
- P1618
- P1622
- P1628
- P1629
- P167
- P1696
- P1697
- P16A3
- P16A5
- P1720
- P1727
- P1728
- P1B14
- P1C4E
- P1C57
- P1C82
- P1C8C
- P1CA7
- P1CA8
- P1CC9
- P1D66
- P1D67
- P1D68
- P1D78
- P1D80
- P1D8F
- P1D91
- P1D94
- P1D99
- P1DAB
- P1DAD
- P1DAF
- P1DB2
- P1DB3
- P1DB6
- P1DB8
- P1DB9
- P1DC8
- P1DCE
- P1DCF
- P1E23
- P2072
- P2096
- P2097
- P2100
- P2101
- P2102
- P2103
- P2107
- P2112
- P2115
- P2116
- P2118
- P2123
- P2128
- P2135
- P2166
- P2174
- P2175
- P2228
- P2238
- P2243
- P2244
- P2252
- P2253
- P2262
- P2271
- P2299
- P2301
- P2304
- P2305
- P2307
- P2310
- P2311
- P2503
- P2761
- P2784
- P2802
- P2803
- P2879
- U0101
- U0102
- U0103
- U0126
- U0151
- U0168
- U0300
- U0402
- U0403
- U0404
- U0416
- U0423
- U0429
- U110
- U110C
- U1120
- U11B9
- U11DD
- U140
- U1400
- U1401
- U1403
- U140B
- U1412
- U1461
- U1465
- U1504
- U1932
- U1934
- U193C
- U1950
- Ford DTC
- B012-1C
- B012-2F
- B012-64
- B012-96
- B0120-00
- B0121-00
- B0122-00
- B0123-01
- B0123-11
- B0123-12
- B0123-1A
- B0123-1B
- B0124-01
- B0124-11
- B0124-12
- B0124-1A
- B0124-1B
- B0126-54
- B0127-00
- B012B-01
- B012B-11
- B012B-12
- B012B-1C
- B012B-2F
- B012B-64
- B012B-96
- B012C-01
- B012C-11
- B012C-12
- B012C-1C
- B012C-2F
- B012C-64
- B012C-96
- B012D-1C
- B012D-2F
- B012D-64
- B012D-96
- B012F
- B0131-00
- B0135-09
- B0135-1E
- B0135-64
- B1000-01
- B1000-44
- B1000-45
- B1000-46
- B1000-47
- B1000-96
- B1001-16
- B1001-17
- B1001-61
- B1001-62
- B1001-64
- B1001-68
- B1001-79
- B1002-02
- B1002-13
- B1002-64
- B1003-09
- B1003-12
- B1003-13
- B1003-64
- B1004-12
- B1004-13
- B1004-64
- B1005-12
- B1005-64
- B1006-11
- B1006-12
- B1006-15
- B1006-49
- B1006-64
- B1007-12
- B1007-13
- B103C
- B103D
- B1111
- B1113
- B111B
- B111C
- B111D
- B1317
- B1318
- B1663
- B1664
- B1665
- B1666
- B1703
- B1707
- B1711
- B1715
- B1719
- B1723
- B1727
- B1731
- B1952
- B1953
- B1956
- B1957
- B1960
- B1961
- B1964
- B1965
- B19A1
- B19A2
- B19A3
- B19A4
- B19A5
- B19A6
- B19A7
- B19A8
- B2330
- B2331
- B2334
- B2335
- B2340
- B2341
- B2486
- B2572
- B2729
- B272A
- B272B
- B272C
- B272D
- B272E
- B272F
- B2730
- C113
- P000
- P000
- P0001
- P0002
- P0003
- P000B
- P0010
- P0011
- P0013
- P0015
- P0016
- P0017
- P0018
- P0019
- P0020
- P0021
- P0022
- P0023
- P0024
- P0025
- P0030
- P0031
- P0032
- P0034
- P0035
- P0036
- P0037
- P0038
- P0040
- P0041
- P0045
- P0046
- P0047
- P0048
- P0050
- P0053
- P0054
- P0055
- P0056
- P0060
- P0068
- P0069
- P006B
- P007
- P0070
- P0071
- P0072
- P0073
- P0074
- P007B
- P007C
- P007D
- P0087
- P0088
- P0089
- P008A
- P008B
- P008C
- P008D
- P008E
- P008F
- P009
- P0090
- P0091
- P0092
- P0093
- P0096
- P0098
- P00AB
- P00AD
- P00BA
- P00BB
- P00BC
- P00BD
- P00BE
- P00BF
- P00C1
- P00C2
- P00C6
- P00CE
- P00D2
- P00DF
- P00E0
- P00E1
- P010
- P0100
- P0102
- P0104
- P0106
- P0107
- P0108
- P0109
- P010C
- P0112
- P0113
- P0114
- P0115
- P0117
- P0119
- P011E
- P0120
- P0121
- P0122
- P0123
- P0124
- P0125
- P0128
- P012B
- P012C
- P012D
- P012E
- P012F
- P0130
- P0131
- P0132
- P0133
- P0134
- P0135
- P0136
- P0137
- P0138
- P0139
- P013A
- P013C
- P013E
- P0140
- P0141
- P0144
- P0147
- P0148
- P0149
- P014A
- P0150
- P0151
- P0152
- P0153
- P0154
- P0155
- P0156
- P0158
- P0159
- P016
- P0161
- P0168
- P016B
- P016C
- P016D
- P0170
- P0171
- P0172
- P0174
- P0175
- P0176
- P017C
- P017D
- P017E
- P0181
- P0182
- P0183
- P0184
- P0186
- P0188
- P018B
- P018C
- P018D
- P0190
- P0191
- P0192
- P0193
- P0194
- P0195
- P0197
- P0198
- P01C4
- P01C5
- P01C6
- P0201
- P0203
- P0204
- P0205
- P0206
- P0207
- P0208
- P0209
- P0210
- P0212
- P0216
- P0217
- P0218
- P0220
- P0221
- P0222
- P0223
- P023
- P0230
- P0231
- P0232
- P0234
- P0237
- P0238
- P023B
- P023C
- P0243
- P0244
- P0245
- P0246
- P0247
- P0248
- P025
- P025
- P0250
- P025B
- P025C
- P025D
- P0261
- P0262
- P0263
- P0264
- P0265
- P0266
- P0267
- P0268
- P0269
- P026A
- P0270
- P0271
- P0272
- P0274
- P0275
- P0276
- P0277
- P0278
- P0279
- P027A
- P027B
- P028
- P0281
- P0282
- P0283
- P0284
- P028D
- P0297
- P0298
- P0299
- P029A
- P029B
- P029D
- P029E
- P029F
- P02A1
- P02A2
- P02A3
- P02A5
- P02A6
- P02A7
- P02A9
- P02AA
- P02AB
- P02CC
- P02CD
- P02CE
- P02CF
- P02D0
- P02D1
- P02D2
- P02D3
- P02D4
- P02D5
- P02D6
- P02D7
- P02D8
- P02D9
- P02DA
- P02DB
- P02E
- P02E0
- P02E1
- P02E2
- P02E3
- P02E8
- P02E9
- P02EC
- P02ED
- P02F0
- P02F1
- P02F2
- P02F3
- P02F4
- P02F5
- P02FC
- P0300
- P0302
- P0303
- P0304
- P0305
- P0306
- P0307
- P0309
- P0313
- P0315
- P0316
- P0322
- P0326
- P0327
- P0328
- P032C
- P0330
- P0331
- P0332
- P0333
- P0335
- P0336
- P0339
- P033A
- P033C
- P033D
- P0340
- P0341
- P0342
- P0343
- P0344
- P0345
- P0346
- P0349
- P0350
- P0351
- P0352
- P0353
- P0354
- P0355
- P0356
- P0357
- P0358
- P0359
- P0365
- P0369
- P0380
- P0381
- P0390
- P0391
- P0394
- P0400
- P0401
- P0402
- P0403
- P0404
- P0405
- P0406
- P040B
- P040C
- P040D
- P0410
- P0411
- P0412
- P0413
- P0416
- P0417
- P041B
- P041C
- P041D
- P0420
- P0421
- P0430
- P0431
- P043E
- P043F
- P0440
- P0442
- P0443
- P0444
- P044C
- P044D
- P0450
- P0451
- P0452
- P0453
- P0454
- P0455
- P0456
- P0457
- P0458
- P0459
- P0461
- P0462
- P0463
- P046D
- P0470
- P0471
- P0472
- P0473
- P0474
- P0475
- P0476
- P0480
- P0481
- P0482
- P0483
- P0488
- P0489
- P0490
- P0491
- P0495
- P0496
- P0497
- P04D7
- P04D9
- P04DA
- P04DB
- P04E2
- P04E3
- P04ED
- P04EE
- P04EF
- P04FA
- P050
- P050
- P0500
- P0501
- P0502
- P0503
- P0504
- P0505
- P0506
- P0507
- P050B
- P050F
- P0511
- P0512
- P051B
- P051C
- P051D
- P0523
- P0524
- P0528
- P0529
- P052A
- P052B
- P052D
- P0532
- P0533
- P0534
- P0537
- P0538
- P053A
- P053F
- P0541
- P0542
- P0544
- P0545
- P0546
- P054A
- P054C
- P054D
- P054E
- P054F
- P0552
- P0553
- P0560
- P0562
- P0565
- P0567
- P0568
- P0569
- P0571
- P0572
- P0573
- P0579
- P059F
- P05A1
- P05A2
- P05A7
- P05C0
- P05C8
- P05C9
- P05FF
- P060
- P0600
- P0601
- P0602
- P0603
- P0604
- P0605
- P0606
- P0607
- P060B
- P060C
- P060D
- P0611
- P0613
- P0615
- P0616
- P0617
- P061A
- P061B
- P061D
- P061E
- P061F
- P0620
- P0622
- P0623
- P0625
- P0626
- P0627
- P0628
- P0629
- P062A
- P062B
- P062D
- P062E
- P062F
- P0634
- P0640
- P0641
- P0642
- P0643
- P0645
- P0646
- P0647
- P0649
- P064A
- P064C
- P064D
- P064E
- P064F
- P0652
- P0653
- P0657
- P0658
- P0659
- P065B
- P065C
- P0660
- P0667
- P0668
- P0669
- P066A
- P066C
- P066D
- P066E
- P0670
- P0671
- P0672
- P0673
- P0678
- P067A
- P067C
- P067D
- P067F
- P0683
- P0685
- P0687
- P0689
- P068A
- P068C
- P068D
- P068E
- P068F
- P0690
- P0691
- P0692
- P0693
- P0694
- P06A0
- P06A6
- P06A7
- P06A8
- P06A9
- P06B1
- P06B6
- P06B8
- P06BA
- P06BB
- P06BD
- P06BE
- P06C0
- P06D1
- P06DA
- P06DB
- P06DC
- P06DD
- P06DF
- P06E4
- P06E5
- P06E9
- P06EA
- P06EB
- P0700
- P0701
- P0702
- P0703
- P0704
- P0705
- P0706
- P0707
- P0710
- P0711
- P0712
- P0713
- P0714
- P0715
- P0716
- P0717
- P0718
- P071A
- P071B
- P0720
- P0721
- P0722
- P0723
- P0726
- P0727
- P0729
- P072B
- P072C
- P072D
- P072F
- P0730
- P0731
- P0732
- P0733
- P0734
- P0735
- P0736
- P073A
- P073B
- P073D
- P073E
- P073F
- P0741
- P0742
- P0743
- P0744
- P0745
- P0746
- P0748
- P074A
- P074B
- P074C
- P074D
- P074E
- P0750
- P0751
- P0752
- P0753
- P0754
- P0755
- P0756
- P0757
- P0758
- P0759
- P0760
- P0761
- P0762
- P0764
- P0765
- P0766
- P0767
- P0768
- P0769
- P0770
- P0771
- P0772
- P0773
- P0774
- P0775
- P0778
- P0780
- P0781
- P0782
- P0783
- P0784
- P0791
- P0794
- P0795
- P0798
- P07A2
- P07A3
- P07A4
- P07A5
- P07A8
- P07A9
- P07AA
- P0805
- P0806
- P0812
- P0813
- P0816
- P0817
- P0819
- P0826
- P0829
- P0830
- P0833
- P0840
- P0850
- P0867
- P087A
- P087B
- P087E
- P0882
- P0884
- P0885
- P0887
- P088E
- P08A9
- P08AA
- P08B6
- P08B9
- P090
- P0901
- P0902
- P0903
- P090B
- P090C
- P090D
- P0960
- P0961
- P0962
- P0963
- P0964
- P0966
- P0967
- P0968
- P0971
- P0972
- P0973
- P0974
- P0975
- P0976
- P0977
- P0978
- P0979
- P0980
- P0981
- P0982
- P0983
- P0984
- P0986
- P0997
- P0998
- P0A00
- P0A01
- P0A02
- P0A05
- P0A06
- P0A07
- P0A08
- P0A09
- P0A0A
- P0A0C
- P0A10
- P0A11
- P0A12
- P0A13
- P0A18
- P0A1A
- P0A1B
- P0A1D
- P0A23
- P0A2A
- P0A2B
- P0A2D
- P0A2F
- P0A36
- P0A37
- P0A38
- P0A39
- P0A3B
- P0A3C
- P0A3E
- P0A40
- P0A44
- P0A5A
- P0A5B
- P0A5D
- P0A5F
- P0A60
- P0A62
- P0A63
- P0A65
- P0A6F
- P0A71
- P0A72
- P0A74
- P0A77
- P0A78
- P0A7A
- P0A7C
- P0A7D
- P0A7E
- P0A8B
- P0A8D
- P0A8E
- P0A90
- P0A92
- P0A94
- P0A95
- P0A96
- P0A9B
- P0AA6
- P0AAC
- P0AB1
- P0ABF
- P0AE1
- P0AEE
- P0AEF
- P0AF0
- P0B0D
- P0BCD
- P0BCE
- P0BCF
- P0BFD
- P0C00
- P0C03
- P0C0C
- P0C17
- P0C19
- P0C2F
- P0C39
- P0C3B
- P0C3E
- P0C3F
- P0C40
- P0C50
- P0C51
- P0C64
- P0C65
- P0C73
- P0C79
- P0CA3
- P0D2D
- P0D32
- P0D33
- P0DA8
- P0DFA
- P0DFC
- P0E10
- P0E4E
- P0E4F
- P0E51
- P0E52
- P0E57
- P0E5A
- P0E5B
- P0E71
- P1000
- P1001
- P1009
- P100F
- P1011
- P1012
- P1013
- P1014
- P1015
- P1016
- P101F
- P1021
- P1022
- P1023
- P1024
- P1025
- P1026
- P103
- P1030
- P1031
- P1032
- P1033
- P1034
- P1035
- P1038
- P1039
- P103B
- P1060
- P1061
- P1100
- P1102
- P1103
- P1106
- P1107
- P1111
- P1112
- P1114
- P1115
- P1116
- P1117
- P1119
- P111B
- P1120
- P1121
- P1124
- P1125
- P1127
- P1128
- P1129
- P1130
- P1131
- P1132
- P1137
- P1138
- P1139
- P1140
- P1145
- P1148
- P1149
- P115
- P115
- P1152
- P1157
- P1158
- P1168
- P1169
- P1177
- P117A
- P117B
- P117F
- P1180
- P1181
- P1183
- P1184
- P1199
- P119F
- P1201
- P1202
- P1204
- P1205
- P1206
- P1207
- P1208
- P1209
- P1210
- P1211
- p1212
- P1220
- P1224
- P1227
- P1228
- P1229
- P123
- P1231
- P1232
- P1233
- P1235
- P1236
- P1237
- P1238
- P123C
- P123F
- P1244
- P1245
- P1246
- P1247
- P1248
- P1249
- P1250
- P126
- P126
- P1260
- P1261
- P1262
- P1264
- P1265
- P1266
- P1267
- P126B
- P126C
- P126D
- P127
- P1270
- P1271
- P1272
- P1273
- P1274
- P1275
- P1276
- P1277
- P1278
- P1280
- P1281
- P1283
- P1284
- P1285
- P1288
- P1289
- P1290
- P1291
- P1292
- P1294
- P1296
- P1297
- P1299
- P1309
- P130D
- P1316
- P132
- P132C
- P1335
- P1351
- P1352
- P1353
- P1354
- P1355
- P1358
- P1359
- P1378
- P1379
- P1381
- P1383
- P1385
- P1386
- P1388
- P138B
- P138D
- P1390
- P1391
- P1393
- P1396
- P1397
- P139A
- P139B
- P139C
- P1400
- P1401
- P1403
- P1405
- P1406
- P1407
- P1408
- P1409
- P1410
- P1411
- P1413
- P1414
- P1432
- P1436
- P1442
- P1444
- P1445
- P144A
- P144B
- P144C
- P1450
- P1451
- P1452
- P1455
- P145B
- P145E
- P1460
- P1461
- P1462
- P1463
- P1464
- P1469
- P1473
- P1474
- P1477
- P1479
- P147B
- P147C
- P1480
- P1481
- P1483
- P1484
- P1487
- P1489
- P1500
- P1501
- P1504
- P1505
- P1506
- P1507
- P1512
- P1513
- P1516
- P1517
- P1518
- P1519
- P1520
- P1530
- P1531
- P1536
- P1537
- P1538
- P1539
- P1548
- P1549
- P1550
- P1551
- P1552
- P1553
- P1554
- P1555
- P1556
- P1557
- P1558
- P1561
- P1572
- P1575
- P1582
- P1584
- P1586
- P1588
- P1605
- P160C
- P1610
- P1611
- P1615
- P1616
- P1617
- P1618
- P161A
- P161B
- P162
- P1625
- P1626
- P162D
- P162F
- P163
- P163
- P1633
- P1635
- P1636
- P1639
- P163C
- P163F
- P164
- P164
- P1640
- P1641
- P1646
- P1647
- P164B
- P164C
- P1650
- P1651
- P166
- P1660
- P1662
- P1663
- P1667
- P1668
- P1670
- P1671
- P1674
- P167F
- P1690
- P1698
- P169B
- P169C
- P170
- P1700
- P1701
- P1702
- P1703
- P1704
- P1705
- P1707
- P1708
- P1709
- P1710
- P1712
- P1714
- P1715
- P1717
- P1718
- P1719
- P1725
- P1727
- P1728
- P1729
- P1741
- P1742
- P1744
- P1746
- P1747
- P1748
- P1749
- P174E
- P175
- P1751
- P1754
- P1756
- P1760
- P1761
- P1762
- P1767
- P1779E
- P177F
- P1780
- P1781
- P1783
- P1784
- P1785
- P1786
- P1787
- P1788
- P1789
- P1793
- P179A
- P1815
- P181F
- P182B
- P182C
- P182D
- P1832
- P183D
- P183F
- P1849
- P1853
- P1857
- P1861
- P1867
- P187B
- P188B
- P188C
- P188D
- P1901
- P1910
- P1911E
- P1912E
- P1921E
- P193
- P1933
- P1934
- P1935
- P193C
- P193D
- P193F
- P1A03
- P1A04
- P1A05
- P1A06
- P1A07
- P1A08
- P1A0A
- P1A0C
- P1A0D
- P1A0E
- P1A0F
- P1A10
- P1A13
- P1A16
- P1A17
- P1A18
- P1A19
- P1A1A
- P1A1B
- P200
- P2002
- P2004
- P2005
- P2006
- P2007
- P2008
- P2011
- P2014
- P2015
- P2019
- P2020
- P2025
- P2026
- P2027
- P202D
- P203
- P2031
- P2033
- P203B
- P203C
- P203D
- P203F
- P2043
- P2047
- P2048
- P2049
- P204B
- P204C
- P204D
- P204F
- P2054
- P205B
- P205C
- P205D
- P2065
- P2066
- P2067
- P2068
- P206B
- P206C
- P206D
- P2071
- P2072
- P2073
- P2074
- P207F
- P2080
- P2084
- P2088
- P2089
- P208B
- P208C
- P208D
- P208E
- P2090
- P2091
- P2097
- P2099
- P20A0
- P20A1
- P20A2
- P20A3
- P20A5
- P20B9
- P20BA
- P20BC
- P20BE
- P20C0
- P20C1
- P20C2
- P20C3
- P20C4
- P20CC
- P20D9
- P20DA
- P20E2
- P20E3
- P20E4
- P20E8
- P20E9
- P20EA
- P20EB
- P20EE
- P20FE
- P2100
- P2101
- P2104
- P2106
- P2107
- P2109
- P2110
- P2111
- P2112
- P2118
- P2119
- P2121
- P2122
- P2123
- P2126
- P2127
- P2128
- P2129
- P2132
- P2134
- P2135
- P2138
- P2139
- P214
- P2140
- P2149
- P214F
- P215B
- P2163
- P2182
- P2184
- P2185
- P2195
- P2196
- P2197
- P2199
- P219A
- P219B
- P219C
- P219E
- P219F
- P21A
- P21A0
- P21A1
- P21AB
- P21AF
- P21CF
- P21D0
- P21D1
- P21D2
- P21D3
- P21D4
- P21D5
- P21D6
- P21DD
- P220
- P220
- P2201
- P2204
- P2209
- P220F
- P221C
- P221D
- P2226
- P2227
- P2228
- P2229
- P2230
- P2237
- P2240
- P2243
- P2247
- P225
- P2251
- P2254
- P2257
- P2258
- P225B
- P2262
- P2263
- P2264
- P2266
- P2267
- P226D
- P2270
- P2271
- P2272
- P2273
- P2274
- P2275
- P2279
- P228
- P2280
- P2281
- P2282
- P2284
- P2285
- P2286
- P2287
- P2288
- P2289
- P228D
- P228F
- P2290
- P2291
- P2297
- P229E
- P22A7
- P2300
- P2301
- P2303
- P2304
- P2306
- P2307
- P2309
- P2310
- P2312
- P2313
- P2316
- P2402
- P2418
- P242
- P242
- P2425
- P2426
- P2427
- P242C
- P242D
- P242F
- P244
- P2448
- P244C
- P244D
- P2450
- P2451
- P2452
- P2453
- P2454
- P2455
- P2456
- P2457
- P2458
- P2459
- P245A
- P2463
- P246C
- P246D
- P246E
- P246F
- P2470
- P2471
- P2478
- P2479
- P247A
- P247B
- P249C
- P249D
- P249E
- P249F
- P24A2
- P24A5
- P24AE
- P24AF
- P24B1
- P24B3
- P24B4
- P24B7
- P24B9
- P24BA
- P24BB
- P24BC
- P24BE
- P24BF
- P24C0
- P24C1
- P24C2
- P24C6
- P24C7
- P24D0
- P24D1
- P24DA
- P2506
- P2507
- P2508
- P2510
- P2531
- P2532
- P2533
- P2535
- P2539
- P2545
- P2552
- P2560
- P259E
- P259F
- P25B0
- P25B1
- P25B2
- P25B3
- P25B4
- P25B5
- P25B6
- P2600
- P260F
- P2610
- P2614
- P2617
- P262
- P2623
- P2626
- P2627
- P2628
- P2629
- P263
- P2630
- P2631
- P2632
- P263C
- P263D
- P264F
- P2669
- P268A
- P268C
- P268D
- P268E
- P268F
- P2690
- P2691
- P2692
- P2693
- P2698
- P269B
- P269D
- P269E
- P26A0
- P26C3
- P26C4
- P26EA
- P2700
- P2701
- P2702
- P2703
- P2704
- P2705
- P2758
- P2760
- P2764
- P2765
- P2766
- P2767
- P2768
- P2783
- P2796
- P2800
- P2801
- P2802
- P2803
- P2805
- P2806
- P2A00
- P2A01
- P2A04
- P2AB7
- P2AB8
- P2AB9
- P2ABA
- P2ABB
- P2ABC
- P2ABD
- P2ABE
- P2B11
- P2B13
- P2B15
- P2B17
- P2B19
- P2B1B
- P2B1D
- P2B1F
- P2BA7
- P2BEC
- P2BED
- P2BEE
- P2BEF
- P2BF0
- P2BF1
- P2BF3
- P2C27
- P2C28
- U0001
- U0002
- U0028
- U0046
- U0073
- U0074
- U0100
- U0101
- U0102
- U0104
- U0105
- U0106
- U0109
- U010E
- U010F
- U0115
- U0120
- U0121
- U0126
- U0129
- U012D
- U0133
- U0137
- U0138
- U0140
- U0141
- U0151
- U0155
- U0164
- U016A
- U016C
- U0198
- U019B
- U0212
- U0214
- U0235
- U0284
- U0293
- U0294
- U0298
- U029D
- U029E
- U02A2
- U02A3
- U0300
- U0306
- U0307
- U0401
- U0402
- U0405
- U0407
- U040F
- U0412
- U0415
- U0418
- U0419
- U041E
- U0422
- U0423
- U0424
- U042E
- U0433
- U0452
- U0469
- U04A4
- U0515
- U059E
- U05A0
- U05A1
- U05A2
- U0606
- U101
- U1010
- U1011
- U1013
- U1017
- U101F
- U1020
- U1021
- U1037
- U1039
- U1041
- U1051
- U1073
- U1089
- U1098
- U1130
- U1131
- U1135
- U1147
- U1243
- U1256
- U1260
- U1261
- U1262
- U1341
- U1451
- U2015
- U2016
- U2023
- U2100
- U2101
- U210B
- U210C
- U210F
- U2110
- U2195
- U2200
- U2243
- U2472
- U2510
- U2511
- U300C
- GMC DTC
- B101D
- B1428
- B2722
- B3105
- B3844
- C0055
- C0235
- C0236
- C0237
- C0241
- C0244
- C0267
- C0298
- C120
- C120
- C120C
- C120D
- C121
- C121
- C121C
- C121D
- C121F
- C122
- C123
- C123
- C123B
- C123C
- C123D
- C123F
- C1256
- C126D
- C126E
- C126F
- C127C
- C127D
- C127E
- C128
- C128B
- C128C
- C128D
- C128F
- C129
- C129
- C129B
- C129D
- C12A7
- C12B1
- C12B2
- C12B3
- C12B4
- C12B6
- C12B7
- C12B8
- C12B9
- C12BA
- C12BB
- C12BC
- C12BD
- C12C2
- C12C5
- C12C6
- C12C8
- C12CC
- C12CF
- C12D0
- C12D1
- C12D2
- C12D3
- C12D4
- C12D5
- C12D6
- C12D7
- C12D8
- C12D9
- C12DA
- C12DB
- C12DC
- C12DD
- C12DE
- C12DF
- C12E4
- C12E7
- C12F2
- C12F3
- C12F4
- C12F5
- C12F6
- C12F7
- C12F8
- P0005
- P0010
- P0011
- P0013
- P0017
- P003
- P0030
- P0045
- P0046
- P0047
- P0048
- P0050
- P0053
- P0054
- P0056
- P0059
- P006
- P0068
- P006F
- P007C
- P007D
- P0087
- P0088
- P0089
- P008F
- P0090
- P0091
- P0092
- P0093
- P0098
- P00CA
- P0101
- P0103
- P0105
- P0106
- P0107
- P0111
- P0113
- P0116
- P0117
- P0118
- P0120
- P0121
- P0122
- P0123
- P0125
- P0128
- P0130
- P0131
- P0132
- P0133
- P0134
- P0135
- P0136
- P0138
- P013A
- P013B
- P013C
- P013D
- P013E
- P0140
- P0141
- P0143
- P0144
- P0147
- P0148
- P014B
- P0151
- P0152
- P0153
- P0156
- P0158
- P0160
- P0161
- P0168
- P0171
- P0174
- P0179
- P0181
- P0182
- P0183
- P0187
- P018B
- P018D
- P0191
- P0193
- P0201
- P0202
- P0203
- P0204
- P0205
- P0206
- P0208
- P0216
- P0218
- P0220
- P0221
- P0222
- P0225
- P0227
- P0228
- P0231
- P0234
- P0236
- P025
- P0251
- P0263
- P0266
- P0269
- P0272
- P0275
- P0278
- P0284
- P0299
- P02E0
- P02E2
- P02E3
- P02EB
- P0300
- P0302
- P0303
- P0305
- P0306
- P0307
- P0308
- P0315
- P0324
- P0325
- P0326
- P0327
- P0328
- P0330
- P0331
- P0332
- P0333
- P0335
- P0336
- P0337
- P0338
- P0339
- P0340
- P0342
- P0343
- P0351
- P0352
- P0353
- P0354
- P0355
- P0356
- P0357
- P0358
- P0365
- P0366
- P0370
- P0374
- P0380
- P0400
- P0401
- P0402
- P0403
- P0404
- P0405
- P0406
- P040C
- P040D
- P0410
- P0411
- P0418
- P041D
- P0420
- P0430
- P0440
- P0441
- P0442
- P0443
- P0449
- P0451
- P0452
- P0453
- P0454
- P0460
- P0461
- P0462
- P0463
- P0464
- P046C
- P0480
- P0481
- P0482
- P0489
- P0490
- P0493
- P0496
- P049D
- P0500
- P0501
- P0503
- P0504
- P0506
- P0507
- P0520
- P0521
- P0522
- P0523
- P0526
- P0530
- P0532
- P0540
- P0545
- P0546
- P0557
- P0558
- P0560
- P0561
- P0562
- P0563
- P0564
- P0567
- P0568
- P0571
- P0572
- P0573
- P0575
- P060
- P0600
- P0601
- P0602
- P0603
- P0604
- P0605
- P0606
- P0607
- P0608
- P0609
- P060B
- P060D
- P0611
- P0612
- P0613
- P0615
- P061A
- P061B
- P061C
- P0621
- P0622
- P0628
- P0629
- P062C
- P062F
- P0630
- P0634
- P0640
- P0641
- P0642
- P0643
- P0645
- P0646
- P064A
- P064C
- P0650
- P0651
- P0652
- P0653
- P0654
- P0657
- P0658
- P0659
- P0667
- P0668
- P0669
- P0670
- P0671
- P0672
- P0673
- P0675
- P0676
- P0677
- P0678
- P0685
- P0689
- P0690
- P0697
- P0699
- P06A3
- P06AC
- P06AD
- P06AE
- P06AF
- P06B1
- P06B2
- P06B4
- P06B6
- P06B7
- P06D2
- P0700
- P0701
- P0703
- P0704
- P0705
- P0708
- P0711
- P0712
- P0713
- P0716
- P0717
- P0719
- P071A
- P0721
- P0723
- P0724
- P0726
- P0727
- P0729
- P0730
- P0731
- P0732
- P0733
- P0734
- P0735
- P0736
- P0740
- P0741
- P0742
- P0743
- P0746
- P0747
- P0748
- P0751
- P0752
- P0753
- P0756
- P0757
- P0758
- P0761
- P0762
- P0763
- P0768
- P0773
- P0776
- P0777
- P0778
- P0785
- P0787
- P0788
- P079
- P0796
- P0797
- P079B
- P079C
- P079D
- P07A3
- P07A5
- P07A7
- P07A9
- P080
- P0802
- P0806
- P0807
- P0808
- P0815
- P0816
- P0826
- P0827
- P0828
- P0831
- P0833
- P0836
- P0840
- P0842
- P0845
- P0846
- P0847
- P0848
- P0850
- P0851
- P0852
- P0856
- P0870
- P0871
- P0872
- P0873
- P0875
- P0877
- P0878
- P0880
- P0881
- P0882
- P0883
- P0894
- P0960
- P0961
- P0962
- P0963
- P0965
- P0966
- P0967
- P0970
- P0971
- P0972
- P0974
- P0975
- P0976
- P0978
- P0979
- P0980
- P0989
- P0990
- P0A01
- P0A02
- P0A03
- P0A07
- P0A0A
- P0A1B
- P0A1C
- P0A1D
- P0A1F
- P0A2B
- P0A2C
- P0A2D
- P0A2F
- P0A31
- P0A32
- P0A35
- P0A3E
- P0A3F
- P0A40
- P0A45
- P0A46
- P0A78
- P0A7E
- P0A80
- P0A81
- P0A8D
- P0A8E
- P0A95
- P0A9C
- P0A9D
- P0A9E
- P0AAD
- P0AAE
- P0AAF
- P0AB2
- P0AB3
- P0AB4
- P0AB9
- P0ABB
- P0ABC
- P0ABD
- P0AC0
- P0AC1
- P0AC2
- P0AC4
- P0AC6
- P0AC7
- P0AC8
- P0ACB
- P0ACC
- P0ACD
- P0ADB
- P0ADF
- P0AE0
- P0AE7
- P0AEA
- P0AEB
- P0AEF
- P0AF0
- P0AF4
- P0AF7
- P0AFA
- P0AFB
- P0AFF
- P0B3C
- P0B3D
- P0B3E
- P0B41
- P0B42
- P0B43
- P0B46
- P0B47
- P0B48
- P0B4B
- P0B4C
- P0B4D
- P0B50
- P0B51
- P0B52
- P0B55
- P0B56
- P0B57
- P0B5A
- P0B5B
- P0B5C
- P0B5F
- P0B60
- P0B61
- P0B64
- P0B65
- P0B66
- P0B69
- P0B6A
- P0B6B
- P0B6E
- P0B6F
- P0B70
- P0B73
- P0B74
- P0B75
- P0B78
- P0B79
- P0B7A
- P0B7D
- P0B7E
- P0B7F
- P0B82
- P0B83
- P0B84
- P0B87
- P0B88
- P0B89
- P0B8C
- P0B8D
- P0B8E
- P0B91
- P0B92
- P0B93
- P0B96
- P0B97
- P0B98
- P0B9B
- P0B9C
- P0B9D
- P0BBD
- P0BC1
- P0BD3
- P0BD4
- P0BD8
- P0BD9
- P0BDD
- P0BDE
- P0BE2
- P0BE3
- P0BFD
- P0BFE
- P0C05
- P0C08
- P0C0B
- P0C0E
- P0C11
- P0C13
- P0C14
- P0C15
- P0C16
- P0C17
- P0C18
- P0C19
- P0C1A
- P0C2B
- P0C2F
- P0C52
- P0C53
- P0C57
- P0C58
- P0C5C
- P0C5D
- P0C61
- P0C62
- P0C77
- P1020
- P1021
- P1022
- P1023
- P1024
- P1025
- P1026
- P1027
- P1028
- P1043
- P1044
- P1045
- P1048
- P1049
- P1082
- P1093
- P1094
- P10CC
- P10CD
- P10CE
- P1101
- P1106
- P1107
- P1111
- P1112
- P1114
- P1115
- P111C
- P111D
- P1120
- P1121
- P1122
- P1125
- P113
- P1133
- P1134
- P1137
- P1138
- P1153
- P1154
- P1171
- P1172
- P1174
- P1175
- P1191
- P11AF
- P11B2
- P11B5
- P11CB
- P11CC
- P11DB
- P11DC
- P1201
- P1203
- P1207
- P1208
- P1214
- P1215
- P1216
- P1217
- P1218
- P122
- P122
- P1220
- P1223
- P1224
- P1227
- P1229
- P122D
- P122F
- P1232
- P1233
- P1235
- P1236
- P1238
- P1239
- P1241
- P1242
- P1244
- P1247
- P125
- P1255
- P1258
- P125B
- P1261
- P1262
- P1270
- P1271
- P1272
- P1273
- P1275
- P1276
- P1277
- P1278
- P1280
- P1281
- P1282
- P1283
- P1285
- P1286
- P1287
- P1288
- P128E
- P1293
- P1294
- P1295
- P1296
- P12B3
- P12B4
- P12B5
- P12B6
- P12B7
- P12B8
- P12B9
- P12BA
- P12BB
- P12BC
- P12BD
- P12BE
- P12BF
- P12C0
- P12C1
- P12C2
- P1336
- P1345
- P1351
- P1361
- P1380
- P1381
- P140
- P140
- P1400
- P1404
- P1406
- P1407
- P1409
- P140B
- P140C
- P140D
- P140F
- P1411
- P1412
- P1413
- P1414
- P1415
- P1416
- P1431
- P1432
- P1433
- P1441
- P144B
- P144F
- P1481
- P1482
- P1484
- P150
- P1504
- P1508
- P1509
- P150B
- P150C
- P1514
- P1515
- P1516
- P1517
- P1518
- P1520
- P1523
- P154
- P1545
- P154B
- P154D
- P1550
- P1571
- P1574
- P159C
- P15F0
- P15F1
- P15F2
- P1600
- P1601
- P160C
- P161A
- P1621
- P1626
- P1627
- P163
- P1630
- P1631
- P1632
- P1633
- P1634
- P1635
- P1637
- P1638
- P1639
- P163C
- P163D
- P1641
- P1643
- P1644
- P1654
- P1655
- P1656
- P1658
- P1668
- P166B
- P1680
- P1681
- P1682
- P1683
- P1684
- P1685
- P1686
- P1687
- P1688
- P1689
- P168C
- P168D
- P16A0
- P16A1
- P16A2
- P16F2
- P16F3
- P16F4
- P16F5
- P16F6
- P16F9
- P1709
- P1710
- P1711
- P1712
- P1713
- P1714
- P1720
- P1721
- P1723
- P1724
- P1751
- P1760
- P1761
- P1762
- P1779E
- P1781
- P179B
- P181
- P1810
- P1811
- P1812
- P1816
- P1818
- P181C
- P181D
- P181F
- P1824
- P1825
- P182A
- P182B
- P182C
- P182D
- P182E
- P182F
- P183
- P183
- P1831
- P1832
- P1838
- P1839
- P183B
- P183C
- P183D
- P183F
- P184A
- P184B
- P1860
- P1862
- P1863
- P1864
- P1870
- P1871
- P1875
- P1876
- P1886
- P1915
- P1A00
- P1A01
- P1A02
- P1A03
- P1A04
- P1A05
- P1A06
- P1A07
- P1A08
- P1A09
- P1A0C
- P1A0D
- P1A1F
- P1A20
- P1A21
- P1A4F
- P1A50
- P1A51
- P1A52
- P1A53
- P1A54
- P1A6C
- P1A7E
- P1A7F
- P1A80
- P1A81
- P1A82
- P1A83
- P1A84
- P1A85
- P1A86
- P1A87
- P1A88
- P1A89
- P1A8C
- P1ABE
- P1AC1
- P1AC2
- P1AC6
- P1AC7
- P1AC9
- P1ADC
- P1ADD
- P1ADE
- P1AE0
- P1AE2
- P1AE3
- P1AE4
- P1AE5
- P1AE6
- P1AE7
- P1AE8
- P1AE9
- P1AEA
- P1AEB
- P1AEC
- P1AED
- P1AEE
- P1AEF
- P1AF0
- P1AF2
- P1AF4
- P1AF6
- P1AF8
- P1AFA
- P1AFB
- P1AFC
- P1AFD
- P1AFE
- P1B01
- P1B02
- P1B03
- P1B04
- P1B05
- P1B06
- P1B0D
- P1B0E
- P1B0F
- P1B10
- P1B15
- P2002
- P202
- P2032
- P2033
- P203B
- P203C
- P203D
- P2047
- P2048
- P2049
- P204B
- P204C
- P204F
- P205B
- P205C
- P2066
- P2067
- P2068
- P207F
- P2080
- P208A
- P208B
- P208D
- P20A0
- P20A1
- P20A2
- P20A3
- P20B9
- P20BA
- P20BB
- P20BC
- P20BD
- P20BF
- P20C0
- P20C1
- P20C3
- P20C4
- P20CB
- P20CC
- P20CD
- P20CE
- P20E2
- P20EE
- P2108
- P2119
- P2120
- P2121
- P2122
- P2123
- P2125
- P2127
- P2132
- P2133
- P2135
- P2138
- P2139
- P2140
- P2141
- P2142
- P2144
- P2145
- P2146
- P2149
- P2152
- P2155
- P215B
- P2161
- P2176
- P2199
- P219A
- P219B
- P21A
- P21AB
- P21AF
- P21B0
- P220
- P2201
- P2202
- P2203
- P2205
- P2209
- P220B
- P2227
- P2228
- P2263
- P2266
- P2270
- P2271
- P2272
- P2273
- P2279
- P2294
- P2295
- P2296
- P229E
- P229F
- P22A0
- P22A1
- P22A3
- P22A7
- P2413
- P242B
- P242D
- P2430
- P2431
- P2432
- P2433
- P2440
- P2444
- P244D
- P2453
- P2454
- P2455
- P2457
- P245A
- P245C
- P245D
- P2463
- P246F
- P2470
- P2471
- P2493
- P2494
- P2495
- P24A0
- P24A1
- P2510
- P251A
- P251E
- P251F
- P2534
- P2536
- P253D
- P2544
- P254F
- P2563
- P2564
- P2565
- P258E
- P2598
- P260
- P260B
- P260C
- P260D
- P2610
- P2632
- P2633
- P2634
- P2668
- P2669
- P2670
- P268A
- P268C
- P268D
- P268E
- P268F
- P2690
- P2691
- P2692
- P2693
- P2714
- P2715
- P2719
- P2720
- P2721
- P2723
- P2724
- P2727
- P2728
- P2729
- P2730
- P2761
- P2763
- P2769
- P2770
- P2771
- P2796
- P2797
- P279D
- P2A01
- P2A04
- P3400
- P3401
- P3425
- P3441
- P3449
- U0001
- U0073
- U0100
- U0101
- U0105
- U0106
- U0111
- U0131
- U0140
- U0151
- U0155
- U0184
- U0299
- U1000
- U1001
- U1016
- U1017
- U1024
- U1026
- U1040
- U1041
- U1048
- U1064
- U1088
- U1092
- U1096
- U1097
- U1098
- U1099
- U1111
- U1128
- U1129
- U1133
- U1137
- U1144
- U1147
- U1152
- U1153
- U1160
- U1161
- U1162
- U1166
- U1167
- U1173
- U1176
- U1192
- U1193
- U1241
- U1254
- U1255
- U1300
- U1301
- U1305
- U1500
- U1800
- U180F
- U1842
- U1843
- U186B
- U1881
- U1882
- U1883
- U1884
- U1885
- U1886
- U1887
- U1888
- U1889
- U1891
- U1892
- U1893
- U1894
- U1895
- U1896
- U1897
- U1898
- U1899
- U2100
- U2104
- U2105
- U2106
- Honda DTC
- B1000
- B1001
- B1002
- B1005
- B1006
- B1007
- B1008
- B1009
- B1010
- B1011
- B1026
- B1027
- B1028
- B1036
- B1050
- B1052
- B1055
- B1056
- B1057
- B1058
- B1059
- B1060
- B1376
- B1377
- B1378
- B1380
- B1381
- B1382
- B1383
- B1384
- B1386
- B1387
- B1388
- B1389
- B1390
- B1575
- B1776
- B1779
- B1780
- B1792
- B1802
- B1825
- B1826
- B1827
- B1828
- B1829
- B1836
- B1837
- B1844
- B1845
- B1900
- B1905
- B1906
- B1C55
- B1C56
- B1C57
- B1C58
- B1C60
- B1C61
- B1C62
- B1C63
- B1C69
- B1C70
- B1C71
- B2456
- B2476
- B2477
- B2479
- B2482
- B2601
- B2602
- B2625
- B2628
- B2629
- B2630
- B2631
- B2632
- B2633
- B2634
- B2635
- B2636
- B2967
- B2968
- B2969
- B2983
- B2986
- P0096
- P0097
- P0098
- P0102
- P0103
- P0106
- P0107
- P0108
- P0111
- P0112
- P0113
- P0116
- P0117
- P0118
- P0121
- P0122
- P0123
- P0125
- P0131
- P0132
- P0135
- P0137
- P0138
- P0140
- P0141
- P0143
- P0144
- P0147
- P0151
- P0152
- P0153
- P0154
- P0157
- P0159
- P0160
- P0161
- P0171
- P0172
- P0174
- P0175
- P0191
- P0192
- P0193
- P0202
- P0203
- P0204
- P0205
- P0206
- P0218
- P0222
- P0223
- P0300
- P0301
- P0303
- P0304
- P0305
- P0306
- P0325
- P0326
- P0327
- P0330
- P0335
- P0336
- P0337
- P0339
- P0340
- P0341
- P0342
- P0344
- P0351
- P0352
- P0353
- P0354
- P0355
- P0356
- P0365
- P0385
- P0389
- P0400
- P0402
- P0404
- P0405
- P0406
- P0410
- P0411
- P0420
- P0430
- P0440
- P0441
- P0442
- P0443
- P0445
- P0447
- P0448
- P0455
- P0456
- P0461
- P0462
- P0463
- P0464
- P0496
- P0497
- P0499
- P050
- P0501
- P0502
- P0505
- P0506
- P0507
- P050B
- P0511
- P0522
- P0523
- P0532
- P0533
- P0555
- P0557
- P055B
- P055C
- P055D
- P0560
- P0562
- P0563
- P0565
- P0566
- P0568
- P060
- P0600
- P0601
- P0602
- P0603
- P0604
- P0606
- P0607
- P0615
- P061F
- P0630
- P0641
- P0651
- P0700
- P0705
- P0706
- P0711
- P0712
- P0716
- P0718
- P0719
- P0720
- P0721
- P0722
- P0723
- P0724
- P0725
- P0730
- P0733
- P0734
- P0735
- P0741
- P0742
- P0746
- P0747
- P0748
- P0752
- P0753
- P0756
- P0758
- P0762
- P0763
- P0766
- P0767
- P0771
- P0776
- P0777
- P0780
- P0796
- P0797
- P0812
- P0842
- P0847
- P0848
- P0872
- P0873
- P0963
- P0966
- P0967
- P0970
- P0971
- P0973
- P0976
- P0977
- P0979
- P0980
- P0982
- P0983
- P0985
- P0A14
- P0A16
- P0AB6
- P0AB7
- P0AB8
- P1009
- P1077
- P1078
- P1102
- P1106
- P1107
- P1108
- P1109
- P1111
- P1112
- P1114
- P1116
- P1120
- P1121
- P1122
- P1125
- P1128
- P1129
- P1133
- P1149
- P1153
- P1154
- P1157
- P1162
- P1163
- P1164
- P1165
- P1166
- P1167
- P1168
- P1169
- P1171
- P1172
- P1174
- P1182
- P1183
- P1187
- P1188
- P1193
- P1220
- P1221
- P1253
- P1257
- P1258
- P1259
- P1271
- P1272
- P1273
- P1275
- P1280
- P1285
- P1286
- P128A
- P128C
- P128D
- P1290
- P1295
- P1297
- P1298
- P1299
- P1310
- P1311
- P1312
- P1324
- P1326
- P1336
- P1337
- P1340
- P1359
- P1361
- P1362
- P1366
- P1367
- P1381
- P1382
- P1391
- P1392
- P1393
- P1394
- P1404
- P1406
- P1415
- P1416
- P1441
- P1454
- P1456
- P1457
- P1459
- P145C
- P1486
- P1491
- P1498
- P1508
- P1519
- P1523
- P1541
- P1549
- P15AB
- P15AC
- P15AE
- P15B1
- P15BD
- P15BE
- P15BF
- P15C2
- P15C3
- P1618
- P1635
- P1639
- P1640
- P1641
- P1643
- P1644
- P1645
- P1646
- P1655
- P1658
- P1659
- P1660
- P1671
- P1676
- P1678
- P1681
- P1682
- P1683
- P1684
- P16BB
- P16BC
- P16BD
- P16BE
- P16C0
- P16C4
- P16C5
- P16C6
- P16C7
- P16C8
- P16C9
- P16D6
- P1705
- P1706
- P1709
- P1717
- P1730
- P1731
- P1732
- P1733
- P1734
- P1738
- P1739
- P1743
- P1744
- P1745
- P1746
- P1747
- P1751
- P1753
- P1758
- P1768
- P1773
- P1785
- P1786
- P1790
- P1791
- P1794
- P1850
- P1860
- P1870
- P1882
- P1885
- P1886
- P1888
- P1890
- P1891
- P2101
- P2108
- P2118
- P2122
- P2123
- P2127
- P2128
- P2135
- P2138
- P2176
- P2183
- P2184
- P2185
- P2195
- P2227
- P2228
- P2229
- P2237
- P2238
- P2240
- P2241
- P2243
- P2245
- P2247
- P2249
- P2251
- P2255
- P2270
- P2271
- P2272
- P2273
- P2279
- P2413
- P2422
- P2446
- P2552
- P2610
- P2628
- P2630
- P2631
- P2646
- P2647
- P2648
- P2649
- P2653
- P2658
- P2659
- P2769
- P2770
- P2A00
- P2A03
- P3400
- P3497
- U0028
- U0029
- U0073
- U0107
- U0110
- U0114
- U0121
- U0127
- U0151
- U0155
- U0164
- U0180
- U0199
- U0230
- U0300
- U0416
- U1064
- U1101
- U1102
- U1205
- U1221
- U1280
- U1281
- U1282
- U1283
- U1288
- U128D
- Hummer DTC
- B0004
- B0005
- B0010
- B0012
- B0013
- B0014
- B0016
- B0017
- B0018
- B0024
- B0026
- B0043
- B0044
- B0051
- B0053
- B0057
- B0058
- B0059
- B0061
- B0062
- B0065
- B0066
- B0068
- B0069
- B0070
- B0071
- B0077
- B0078
- B0079
- B0080
- B0081
- B0082
- B0083
- B0084
- B0092
- B0098
- B0100
- B0101
- B0102
- B0103
- B0104
- B0105
- B0285
- B0286
- B0525
- B0527
- B0528
- B0529
- B0530
- B0532
- B0533
- B0534
- B0687
- B0688
- B0790
- B1002
- B1004
- B1005
- B1006
- B1007
- B1008
- B1009
- B1010
- B1011
- B1025
- B1026
- B1027
- B1028
- B1035
- B1036
- B1045
- B1050
- B1052
- B1055
- B1056
- B1057
- B1058
- B1059
- B1060
- B1259
- B1327
- B1372
- B1373
- B1382
- B1383
- B1390
- B1420
- B1442
- B1443
- B1477
- B1478
- B1516
- B1530
- B2455
- B2462
- B2476
- B2482
- B2485
- B2532
- B2533
- B2557
- B2558
- B2575
- B2582
- B2585
- B2602
- B2603
- B2622
- B2623
- B2647
- B2648
- B2707
- B2708
- B2725
- B272C
- B2745
- B2752
- B2753
- B2957
- B2958
- B2960
- B3033
- B3142
- B3143
- B3152
- B3153
- B3717
- B3718
- B3855
- B3856
- B3857
- B3935
- B3976
- C0045
- C0050
- C0110
- C0131
- C0136
- C0186
- C0191
- C0196
- C0244
- C0245
- C0267
- C0268
- C0276
- C0327
- C0329
- C0388
- C0395
- C0550
- C0558
- C0569
- C0710
- C0750
- C0755
- C0760
- C0765
- C0775
- C0899
- C0901
- P0010
- P0011
- P0013
- P0016
- P0017
- P0030
- P0036
- P0101
- P0102
- P0103
- P0107
- P0108
- P0112
- P0113
- P0116
- P0118
- P0120
- P0121
- P0123
- P0125
- P0128
- P0130
- P0131
- P0132
- P0133
- P0134
- P0135
- P0138
- P013A
- P013B
- P013C
- P013D
- P013F
- P0141
- P014A
- P014B
- P0152
- P0154
- P0155
- P0157
- P0160
- P0161
- P0172
- P0174
- P0175
- P0200
- P0201
- P0202
- P0203
- P0204
- P0205
- P0218
- P0220
- P0222
- P0223
- P0230
- P0301
- P0303
- P0304
- P0305
- P0306
- P0308
- P0325
- P0327
- P0328
- P0330
- P0332
- P0333
- P0335
- P0336
- P0340
- P0341
- P0351
- P0352
- P0353
- P0354
- P0356
- P0357
- P0358
- P0365
- P0420
- P0430
- P0442
- P0446
- P0453
- P0461
- P0463
- P0481
- P0502
- P0506
- P0507
- P0520
- P0530
- P0562
- P0564
- P0601
- P0602
- P0603
- P0604
- P0605
- P0606
- P0607
- P0608
- P060D
- P0611
- P0615
- P062F
- P0641
- P0650
- P0654
- P069E
- P0700
- P0711
- P0712
- P0713
- P0716
- P0717
- P0719
- P0722
- P0724
- P0740
- P0741
- P0742
- P0748
- P0751
- P0752
- P0753
- P0757
- P0758
- P0785
- P080
- P0806
- P0807
- P0808
- P0856
- P0961
- P0973
- P0974
- P0976
- P0977
- P1101
- P1106
- P1111
- P1112
- P1114
- P1115
- P1125
- P1133
- P1134
- P1153
- P1174
- P1175
- P1258
- P1380
- P1381
- P150
- P1514
- P1516
- P1518
- P1574
- P1621
- P1626
- P1627
- P1631
- P1635
- P1638
- P1639
- P1680
- P1681
- P1682
- P1683
- P1689
- P1810
- P182A
- P182C
- P182D
- P182F
- P1860
- P1915
- P2120
- P2121
- P2125
- P2135
- P219A
- P2270
- P2271
- P2272
- P2534
- P2635
- P2764
- U1300
- U1301
- Hyundai DTC
- B1101
- B1102
- B1105
- B1111
- B1112
- B1200
- B1201
- B1202
- B1203
- B1204
- B1205
- B1206
- B1207
- B1208
- B1209
- B1210
- B1211
- B1212
- B1213
- B1214
- B1215
- B1216
- B1217
- B1220
- B1223
- B1233
- B1234
- B1237
- B1238
- B1241
- B1242
- B1245
- B1246
- B1249
- B1250
- B1257
- B1258
- B1259
- B1260
- B1261
- B1262
- B1263
- B1270
- B1271
- B1272
- B1273
- B1274
- B1275
- B1276
- B1277
- B1278
- B1279
- B1280
- B1281
- B1282
- B1283
- B1284
- B1285
- B1301
- B1302
- B1303
- B1304
- B1305
- B1306
- B1307
- B1319
- B1322
- B1323
- B1324
- B1325
- B1326
- B1327
- B1328
- B1329
- B1330
- B1331
- B1332
- B1333
- B1334
- B1335
- B1338
- B1344
- B1346
- B1347
- B1348
- B1349
- B1352
- B1353
- B1354
- B1355
- B1361
- B1362
- B1363
- B1364
- B1367
- B1368
- B1369
- B1370
- B1371
- B1378
- B1379
- B1380
- B1381
- B1382
- B1383
- B1384
- B1385
- B1387
- B1388
- B1389
- B1390
- B1391
- B1392
- B1395
- B1396
- B1397
- B1398
- B1399
- B1400
- B1401
- B1402
- B1403
- B1405
- B1409
- B1410
- B1412
- B1413
- B1414
- B1415
- B1416
- B1417
- B1418
- B1419
- B1429
- B1430
- B1431
- B1432
- B1433
- B1435
- B1436
- B1447
- B1448
- B1449
- B1450
- B1451
- B1452
- B1454
- B1455
- B1473
- B1474
- B1475
- B1476
- B1477
- B1478
- B1479
- B1480
- B1481
- B1482
- B1483
- B1484
- B1485
- B1486
- B1487
- B1488
- B1489
- B1490
- B1493
- B1494
- B1495
- B1496
- B1510
- B1511
- B1512
- B1513
- B1514
- B1515
- B1516
- B1517
- B1518
- B1521
- B1522
- B1523
- B1524
- B1550
- B1551
- B1552
- B1553
- B1554
- B1555
- B1562
- B1580
- B1583
- B1586
- B1587
- B1588
- B1589
- B1590
- B1592
- B1602
- B1603
- B1604
- B1605
- B1607
- B1608
- B1611
- B1612
- B1613
- B1619
- B1620
- B1621
- B1622
- B1624
- B1625
- B1627
- B1628
- B1629
- B1630
- B1636
- B1637
- B1638
- B1639
- B1640
- B1641
- B1642
- B1643
- B1644
- B1645
- B1646
- B1647
- B1650
- B1651
- B1652
- B1655
- B1657
- B1658
- B1659
- B1661
- B1672
- B1681
- B1682
- B1683
- B1684
- B1686
- B1687
- B1689
- B1690
- B1699
- B1722
- B1723
- B1724
- B1725
- B1726
- B1727
- B1728
- B1729
- B1730
- B1731
- B1732
- B1733
- B1734
- B1735
- B1736
- B1737
- B1738
- B1744
- B1748
- B1901
- B1905
- B1906
- B1907
- B1908
- B1909
- B1910
- B1911
- B1912
- B1913
- B1952
- B1954
- B1956
- B1957
- B1958
- B1959
- B1960
- B1971
- B1978
- B1988
- B1989
- B1990
- B1991
- B2115
- B2119
- B2325
- B2326
- B2330
- B2332
- B2333
- B2400
- B2401
- B2405
- B2406
- B2408
- B2409
- B2411
- B2415
- B2416
- B2420
- B2421
- B2423
- B2424
- B2425
- B2426
- B2427
- B2429
- B2441
- B2447
- B2448
- B2450
- B2451
- B2452
- B2455
- B2456
- B2457
- B2500
- B2502
- B2510
- B2511
- B2512
- B2513
- B2514
- B2515
- B2516
- B2517
- B2518
- B2520
- B2521
- B2522
- B2523
- B2524
- B2525
- B2529
- B2535
- B2537
- B2539
- B2541
- B2543
- B2545
- B2547
- B2549
- B2553
- B2555
- B2557
- B2559
- B2561
- B2563
- B2565
- B2571
- B2573
- B2575
- B2579
- B2581
- B2583
- B2585
- B2587
- B2589
- B2598
- B2599
- B2800
- B2837
- B2859
- B2860
- C1101
- C1102
- C1103
- C1112
- C1121
- C1122
- C1123
- C1124
- C1126
- C1127
- C1200
- C1201
- C1202
- C1203
- C1204
- C1205
- C1206
- C1207
- C1208
- C1209
- C1210
- C1211
- C1212
- C1213
- C1235
- C1237
- C1240
- C1255
- C1259
- C1260
- C1261
- C1262
- C1274
- C1275
- C1282
- C1283
- C1285
- C1290
- C1300
- C1301
- C1306
- C1312
- C1313
- C1314
- C1315
- C1317
- C1318
- C1319
- C1320
- C1322
- C1323
- C1325
- C1332
- C1333
- C1345
- C1346
- C1503
- C1513
- C1522
- C1527
- C1603
- C1604
- C1605
- C1606
- C1610
- C1612
- C1613
- C1616
- C1617
- C1620
- C1622
- C1625
- C1626
- C1643
- C1647
- C1660
- C1664
- C1665
- C1666
- C1668
- C1687
- C1688
- C1692
- C1693
- C1700
- C1702
- C1704
- C1705
- C2101
- C2112
- C2130
- C2226
- C2227
- C2308
- C2312
- C2316
- C2324
- C2328
- C2332
- C2336
- C2366
- C2370
- C2372
- C2374
- C2380
- C2401
- C2402
- C2412
- C2413
- C2420
- C2421
- C2511
- C2512
- C2513
- C2514
- C2515
- C2610
- P0010
- P0011
- P0012
- P0014
- P0015
- P0016
- P0017
- P0018
- P0019
- P0021
- P0022
- P0024
- P0025
- P0026
- P0028
- P0029
- P0030
- P0032
- P0036
- P0037
- P0038
- P0050
- P0051
- P0052
- P0053
- P0054
- P0056
- P0057
- P0058
- P0059
- P0060
- P0068
- P0075
- P0076
- P0077
- P0078
- P0079
- P0080
- P0081
- P0082
- P0083
- P0084
- P0086
- P0087
- P0088
- P0090
- P0091
- P0092
- P0100
- P0101
- P0102
- P0103
- P0105
- P0106
- P0107
- P0108
- P0109
- P0110
- P0112
- P0113
- P0115
- P0116
- P0117
- P0118
- P0119
- P0120
- P0121
- P0122
- P0123
- P0125
- P0128
- P0130
- P0131
- P0132
- P0133
- P0134
- P0135
- P0136
- P0137
- P0138
- P0139
- P0140
- P0141
- P0150
- P0151
- P0152
- P0153
- P0154
- P0156
- P0157
- P0158
- P0159
- P0160
- P0161
- P0170
- P0171
- P0172
- P0173
- P0174
- P0175
- P0181
- P0182
- P0183
- P0191
- P0192
- P0193
- P0196
- P0197
- P0198
- P020
- P0201
- P0202
- P0203
- P0204
- P0206
- P0207
- P0208
- P020B
- P020C
- P020D
- P0217
- P0219
- P0221
- P0222
- P0223
- P0230
- P0253
- P0254
- P0258
- P0259
- P0261
- P0262
- P0264
- P0265
- P0267
- P0268
- P0271
- P0273
- P0274
- P0276
- P0277
- P0279
- P0280
- P0282
- P0283
- P0300
- P0301
- P0302
- P0303
- P0304
- P0305
- P0306
- P0307
- P0315
- P0320
- P0325
- P0326
- P0327
- P0328
- P032C
- P032D
- P0330
- P0331
- P0332
- P0333
- P0335
- P0336
- P0337
- P0338
- P033D
- P0340
- P0341
- P0342
- P0343
- P0345
- P0346
- P0350
- P0351
- P0352
- P0353
- P0354
- P0355
- P0356
- P0365
- P0366
- P0390
- P0391
- P0400
- P0403
- P0420
- P0421
- P0422
- P0430
- P0431
- P0440
- P0441
- P0442
- P0443
- P0444
- P0445
- P0446
- P0447
- P0448
- P0449
- P0450
- P0451
- P0452
- P0453
- P0454
- P0455
- P0456
- P0457
- P0458
- P0459
- P0460
- P0461
- P0462
- P0463
- P0464
- P0480
- P0481
- P0489
- P0490
- P0496
- P0497
- P0502
- P0503
- P0504
- P0505
- P0506
- P0507
- P050B
- P0510
- P0532
- P0533
- P0551
- P0552
- P0553
- P0560
- P0562
- P0563
- P0564
- P0565
- P0566
- P0567
- P0571
- P0600
- P0601
- P0602
- P0603
- P0604
- P0605
- P0606
- P0607
- P0616
- P061B
- P0620
- P0625
- P0626
- P0638
- P0641
- P0642
- P0643
- P0645
- P0647
- P0650
- P0651
- P0652
- P0653
- P0660
- P0661
- P0662
- P0663
- P0664
- P0665
- P0666
- P0667
- P0685
- P0699
- P06A4
- P06A5
- P0703
- P0704
- P0705
- P0706
- P0707
- P0708
- P0710
- P0711
- P0712
- P0715
- P0716
- P0717
- P0721
- P0722
- P0727
- P0729
- P0730
- P0731
- P0732
- P0733
- P0734
- P0735
- P0736
- P0740
- P0741
- P0742
- P0743
- P0744
- P0745
- P0746
- P0747
- P0748
- P0749
- P0750
- P0751
- P0752
- P0753
- P0754
- P0756
- P0757
- P0758
- P0761
- P0762
- P0763
- P0764
- P0765
- P0769
- P0770
- P0771
- P0773
- P0774
- P0775
- P0780
- P0782
- P0783
- P0784
- P0829
- P0880
- P0882
- P0883
- P0885
- P0889
- P0890
- P0891
- P0892
- P0905
- P0924
- P0926
- P0927
- P0928
- P0930
- P0931
- P0942
- P0961
- P0962
- P0963
- P0965
- P0966
- P0967
- P0970
- P0971
- P0973
- P0974
- P0976
- P0977
- P0978
- P0979
- P0980
- P0981
- P0982
- P0983
- P0985
- P0986
- P0995
- P0997
- P0998
- P0999
- P1100
- P1102
- P1103
- P1106
- P1107
- P1110
- P1111
- P1112
- P1114
- P1115
- P1118
- P1123
- P1124
- P1127
- P1128
- P1134
- P1154
- P1155
- P1166
- P1167
- P1171
- P1172
- P1173
- P1174
- P1175
- P1176
- P1177
- P1178
- P1193
- P1194
- P1195
- P1196
- P1295
- P1308
- P1309
- P1330
- P1372
- P1500
- P1501
- P1502
- P1506
- P1507
- P1508
- P1523
- P1529
- P1586
- P1602
- P1607
- P1610
- P1613
- P1614
- P161B
- P1624
- P1674
- P1675
- P1676
- P1677
- P1678
- P1679
- P1688
- P1690
- P1691
- P1692
- P1693
- P1694
- P1695
- P1696
- P1697
- P1698
- P1699
- P169A
- P1709
- P1716
- P1717
- P1718
- P1719
- P1723
- P1728
- P1729
- P1738
- P1745
- P1750
- P1755
- P1756
- P1757
- P1760
- P1764
- P1765
- P1766
- P1767
- P1769
- P1770
- P1771
- P1780
- P1800
- P1801
- P1803
- P1805
- P200
- P2004
- P2006
- P2008
- P2015
- P2016
- P2017
- P2065
- P2067
- P2069
- P2096
- P2098
- P2100
- P2101
- P2102
- P2105
- P2106
- P2107
- P2108
- P2110
- P2111
- P2112
- P2118
- P2119
- P2122
- P2123
- P2125
- P2127
- P2135
- P2138
- P2159
- P2187
- P2189
- P2190
- P2192
- P2193
- P2194
- P2196
- P2197
- P2198
- P2231
- P2237
- P2243
- P2251
- P2252
- P2253
- P2271
- P2272
- P2273
- P2297
- P2401
- P2402
- P2404
- P2405
- P2406
- P2414
- P2419
- P2422
- P2501
- P2502
- P2503
- P2507
- P2610
- P2626
- P2637
- P2700
- P2701
- P2702
- P2703
- P2704
- P2762
- P2763
- P2764
- P2A00
- P2A01
- P2A03
- P2A04
- U0001
- U0100
- U0101
- U0104
- U0121
- U0122
- U0126
- U1000
- U1001
- U1002
- U1003
- U1004
- U1006
- U1007
- U1010
- U1111
- U1112
- U1500
- U1501
- U1601
- U1606
- U1700
- U1702
- U1710
- U1712
- U1713
- U1714
- U1900
- U1940
- U1941
- U1942
- U1945
- U1970
- U1971
- U1972
- U1980
- U1981
- U1982
- U1983
- Infiniti DTC
- B1017
- B1018
- B1019
- B1020
- B1021
- B1022
- B1023
- B1033
- B1034
- B1035
- B1049
- B1050
- B1051
- B1052
- B1054
- B1055
- B1056
- B1057
- B1065
- B1066
- B1067
- B1068
- B1070
- B1071
- B1072
- B1073
- B1081
- B1082
- B1083
- B1084
- B1088
- B1089
- B1113
- B1114
- B1115
- B1118
- B1119
- B1120
- B1129
- B1130
- B1131
- B1132
- B1134
- B1135
- B1136
- B1137
- B1145
- B1146
- B1147
- B1148
- B1150
- B1151
- B1152
- B1153
- B1177
- B1178
- B1179
- B1180
- B1182
- B1183
- B1184
- B1185
- B1193
- B1194
- B1195
- B1196
- B1198
- B1199
- B1200
- B1201
- B1209
- B1210
- B1211
- B2013
- B2112
- B2113
- B2114
- B2115
- B2117
- B2118
- B2120
- B2126
- B2128
- B2190
- B2191
- B2192
- B2193
- B2590
- B270
- B270
- B2700
- B2701
- B2702
- B2703
- B2704
- B2705
- B2706
- B2707
- B2708
- B2709
- B270B
- B270C
- B270D
- B270F
- C1101
- C1102
- C1103
- C1104
- C1105
- C1106
- C1107
- C1108
- C1109
- C1110
- C1111
- C1113
- C1115
- C1116
- C1120
- C1121
- C1122
- C1123
- C1124
- C1125
- C1126
- C1127
- C1130
- C1131
- C1132
- C1133
- C1136
- C1138
- C1140
- C1142
- C1143
- C1144
- C1145
- C1146
- C1155
- C1156
- C1160
- C1163
- C1164
- C1165
- C1166
- C1167
- C1170
- C1178
- C1179
- C1181
- C1185
- C1189
- C1705
- C1706
- C1707
- C1708
- C1709
- C1710
- C1711
- C1712
- C1713
- C1716
- C1717
- C1718
- C1719
- C1720
- C1721
- C1722
- C1723
- C1724
- C1725
- C1726
- C1727
- C1729
- C1734
- C1801
- C1802
- C1805
- C1807
- C1808
- P0011
- P0021
- P0031
- P0032
- P0037
- P0038
- P0051
- P0052
- P0057
- P0058
- P0075
- P0081
- P0100
- P0101
- P0102
- P0103
- P0105
- P0107
- P0108
- P0110
- P0112
- P0113
- P0115
- P0116
- P0117
- P0118
- P0121
- P0123
- P0127
- P0128
- P0130
- P0131
- P0132
- P0133
- P0135
- P0136
- P0137
- P0138
- P0139
- P0140
- P0141
- P0150
- P0151
- P0152
- P0153
- P0154
- P0155
- P0156
- P0157
- P0158
- P0159
- P0160
- P0161
- P0171
- P0172
- P0174
- P0175
- P0180
- P0181
- P0183
- P0217
- P0222
- P0223
- P0226
- P0227
- P0228
- P0300
- P0302
- P0304
- P0305
- P0306
- P0307
- P0308
- P0325
- P0327
- P0328
- P0330
- P0332
- P0333
- P0335
- P0340
- P0345
- P0402
- P0403
- P0420
- P0430
- P0440
- P0441
- P0443
- P0444
- P0445
- P0446
- P0447
- P0448
- P0450
- P0451
- P0452
- P0453
- P0455
- P0456
- P0461
- P0462
- P0463
- P0464
- P0500
- P0505
- P0506
- P0507
- P0510
- P0550
- P0600
- P0603
- P0605
- P0607
- P0615
- P0700
- P0705
- P0710
- P0717
- P0720
- P0725
- P0731
- P0732
- P0733
- P0734
- P0735
- P0744
- P0750
- P0755
- P0850
- P1035
- P1065
- P1102
- P1105
- P1110
- P1111
- P1120
- P1121
- P1122
- P1125
- P1126
- P1128
- P1130
- P1135
- P1136
- P1137
- P1138
- P1140
- P1143
- P1144
- P1145
- P1146
- P1148
- P1164
- P1165
- P1166
- P1167
- P1168
- P1210
- P1211
- P1217
- P1220
- P1225
- P1226
- P1335
- P1401
- P1402
- P1421
- P1440
- P1443
- P1444
- P1445
- P1446
- P1447
- P1448
- P1464
- P1490
- P1491
- P1550
- P1551
- P1552
- P1553
- P1554
- P1564
- P1568
- P1572
- P1574
- P1605
- P1610
- P1611
- P1612
- P1613
- P1615
- P1706
- P1710
- P1716
- P1721
- P1730
- P1731
- P1752
- P1754
- P1757
- P1759
- P1760
- P1762
- P1764
- P1767
- P1772
- P1774
- P1805
- P1900
- P2103
- P2119
- P2122
- P2123
- P2127
- P2128
- P2135
- P2138
- P2A00
- P2A03
- U1000
- U1001
- U1010
- U1200
- U1201
- U1204
- U1205
- U1206
- U1207
- U1216
- U1217
- U1218
- U1219
- U121A
- U121B
- U121C
- U121D
- U121F
- U1220
- U1243
- U1244
- U1258
- U1300
- U1310
- → P1320
- Isuzu DTC
- B0014
- B0018
- B0059
- B0062
- B0066
- B0068
- B0071
- B0077
- B0078
- B0079
- B0080
- B0081
- B0082
- B0083
- B0084
- B0092
- B0159
- B0164
- B0174
- B0179
- B0183
- B0188
- B0229
- B0248
- B0263
- B0268
- B0283
- B0408
- B0414
- B0418
- B0424
- B0510
- B0515
- B0540
- B0560
- B0770
- B0775
- B0780
- B0785
- B0790
- B1000
- B1017
- B1390
- B1397
- B1487
- B1488
- B1492
- B1516
- B1530
- B1550
- B1720
- B1721
- B1723
- B1724
- B1735
- B1740
- B1745
- B1750
- B1755
- B1760
- B1815
- B1820
- B1825
- B1830
- B1835
- B1850
- B2365
- B2375
- B2425
- B2430
- B2435
- B2440
- B2580
- B2585
- B2615
- B2697
- B2815
- B2945
- B2955
- B2960
- B3031A
- B3033
- B3606
- B3607
- B3761
- B3770
- B3808
- B3809
- B3810
- B3811
- B3819
- B3820
- B3821
- B3822
- B3823
- B3824
- B3855
- B3856
- B3857
- B3935
- B3976
- C0055
- C0161
- C0241
- C0244
- C0267
- C0287
- C0292
- C0300
- C0305
- C0306
- C0321
- C0327
- C0374
- C0379
- C0750
- C0755
- C0760
- C0765
- C0775
- P0013
- P0014
- P0017
- P0030
- P0036
- P0050
- P0053
- P0054
- P0056
- P0059
- P0060
- P0068
- P0101
- P0102
- P0103
- P0106
- P0107
- P0112
- P0113
- P0116
- P0117
- P0118
- P0120
- P0121
- P0122
- P0123
- P0125
- P0128
- P0130
- P0131
- P0132
- P0133
- P0135
- P0136
- P0137
- P0138
- P013A
- P013B
- P013E
- P013F
- P0140
- P0141
- P0151
- P0153
- P0155
- P0156
- P0157
- P0160
- P0161
- P0171
- P0172
- P0174
- P0175
- P0201
- P0202
- P0203
- P0204
- P0205
- P0206
- P0208
- P0218
- P0220
- P0222
- P0301
- P0302
- P0303
- P0304
- P0305
- P0306
- P0307
- P0308
- P0315
- P0324
- P0325
- P0326
- P0327
- P0328
- P0330
- P0332
- P0333
- P0335
- P0336
- P0337
- P0340
- P0341
- P0342
- P0351
- P0352
- P0353
- P0354
- P0356
- P0357
- P0358
- P0365
- P0366
- P0401
- P0402
- P0404
- P0405
- P0406
- P0410
- P0412
- P0418
- P0420
- P0430
- P0440
- P0442
- P0443
- P0446
- P0451
- P0452
- P0453
- P0454
- P0455
- P0462
- P0463
- P0464
- P0480
- P0481
- P0483
- P0493
- P0495
- P0496
- P0503
- P0506
- P0507
- P0520
- P0521
- P0522
- P0523
- P0526
- P0530
- P0532
- P0533
- P0556
- P0557
- P0558
- P0562
- P0563
- P0564
- P0567
- P0568
- P0571
- P060
- P0601
- P0602
- P0603
- P0604
- P0605
- P0606
- P0607
- P0608
- P0609
- P060D
- P0615
- P0621
- P0622
- P062F
- P0641
- P0645
- P0650
- P0654
- P0685
- P0689
- P0690
- P0705
- P0706
- P0711
- P0713
- P0716
- P0717
- P0719
- P071A
- P0722
- P0723
- P0724
- P0740
- P0741
- P0742
- P0748
- P0751
- P0752
- P0753
- P0756
- P0757
- P0758
- P0785
- P0787
- P0788
- P0851
- P0856
- P0894
- P0961
- P0974
- P0977
- P1106
- P1107
- P1112
- P1114
- P1115
- P1121
- P1122
- P1133
- P1134
- P1137
- P1138
- P1153
- P1154
- P1171
- P1174
- P1175
- P1258
- P1380
- P1381
- P1400
- P1404
- P1441
- P1481
- P1484
- P150
- P1508
- P150B
- P1516
- P1545
- P1546
- P1574
- P1600
- P1618
- P1625
- P1626
- P1630
- P1631
- P1632
- P1633
- P1634
- P1635
- P1637
- P1639
- P1644
- P1650
- P1668
- P1681
- P1682
- P1683
- P1689
- P1762
- P1790
- P1792E
- P1810
- P1815
- P1816
- P1818
- P1850
- P1860
- P2101
- P2119
- P2120
- P2123
- P2125
- P2127
- P2128
- P2135
- P2138
- P2176
- P2270
- P2271
- P2272
- P2273
- P2430
- P2431
- P2433
- P2440
- P2444
- P2534
- P2544
- P2610
- P2761
- P2764
- P2770
- P2771
- P2A00
- P2A01
- P2A03
- P2A04
- P3400
- P3401
- P3425
- P3441
- P3449
- U0001
- U0073
- U0100
- U0101
- U0140
- U0151
- U0155
- U0184
- U0299
- U1000
- U1001
- U1017
- U1024
- U1026
- U1040
- U1041
- U1064
- U1096
- U1097
- U1098
- U1099
- U1111
- U1128
- U1129
- U1133
- U1137
- U1144
- U1147
- U1151
- U1152
- U1153
- U1160
- U1161
- U1162
- U1166
- U1167
- U1192
- U1241
- U1254
- U1255
- U1300
- U1301
- U1305
- U1500
- U2100
- U2105
- U2107
- U2108
- Iveco DTC
- Jaguar DTC
- Jeep DTC
- B0004-01
- B0028-13
- B0050-95
- B0099
- B00B5-9A
- B0104-11
- B010F-1B
- B0119
- B0120
- B0121
- B0122
- B0127
- B012F
- B0131
- B104
- B1040-19
- B104D
- B1051-55
- B1054-62
- B1063
- B10B2
- B10C4-11
- B10E9
- B10EA
- B1106-64
- B11C3
- B11C4
- B11C6
- B11C7
- B11C9
- B11CA
- B11CC
- B11CD
- B11D5
- B1423
- B1424
- B142B
- B143-12
- B1441
- B1464
- B1469
- B146E
- B1473
- B1478
- B147D
- B1482
- B1487
- B14DF
- B156D
- B1579-11
- B157E
- B167D
- B1681
- B1810
- B1811
- B188C-13
- B1916-11
- B1945-12
- B1952
- B1953
- B1954
- B1955
- B1956
- B1963
- B1968
- B1969
- B196A
- B196B
- B196C
- B196F
- B1970
- B1971
- B1972
- B1973
- B1974
- B1975
- B1977
- B1979
- B197A
- B1A08
- B1A09
- B1A0A
- B1A0B
- B1A0C
- B1A0D
- B1A0E
- B1A0F
- B1A10
- B1A11
- B1A12
- B1A13
- B1A14
- B1A15
- B1A16
- B1A17
- B1A20
- B1A28
- B1A3C
- B1A3D
- B1A3E
- B1A3F
- B1A7F
- B1A80
- B1A81
- B1A89
- B1A8A
- B1BC7
- B1D7B
- B1D7F
- B1D87
- B1D93
- B1D97
- B1D9C
- B1E64
- B1E65
- B1E9A-1E
- B1F08
- B210
- B210
- B210B
- B210D
- B2193
- B2201
- B2204
- B2205
- B2206
- B2207
- B2208
- B220B
- B2211
- B2216
- B221A
- B221D
- B221E
- B221F
- B2225
- B222A
- B222B
- B222C
- B222D
- B222F
- B2232
- B223B
- B223C
- B2254
- B225C
- B2298
- B2299
- B22A4
- B22A9
- B232
- B235A
- B23AA
- B23BB
- B23BC
- B23BD
- B23BE
- B23BF
- B23C0
- B23C1
- B23C2
- B23C3
- B259A
- B259B
- B25BC
- B25C7
- B25C8
- B25C9
- B25CB
- B2722
- B273F
- B275B
- B2761-01
- B2765-11
- B280B
- B2854
- C0037-2F
- C0042-54
- C0061
- C0062
- C0077
- C008
- C008F
- C0501
- C0507
- C050D
- C0513
- C053E
- C053F
- C0542
- C0543
- C0546
- C1003-97
- C1005-12
- C100B-14
- C1013-29
- C121C
- C1222-87
- C1231
- C1232
- C1234
- C1235
- C1238
- C1239
- C1240
- C124F
- C127A
- C140
- C1403-11
- C1403-13
- C1406-11
- C1408-19
- C141C-12
- C1430-87
- C1438
- C1444
- C1476
- C1481-12
- C148D
- C1490
- C14A4
- C14A5
- C1501-16
- C1503-07
- C1510-54
- C151C
- C151D
- C153-11
- C156
- C1597
- C15A1
- C15A2
- C15A3
- C15A9
- C15AA
- C15AB
- C15AE
- C15B4-04
- C15C1
- C15CB
- C15CC
- C15D6
- C15D8
- C15D9
- C15DB
- C2100-15
- C2201
- C2202
- C2205
- C2206
- C220C
- C2210
- C2210-92
- C2212
- C2217
- C2219
- C221C
- C2220
- C2221
- C2223
- C2225
- C2226
- C2227
- C2300
- P000
- P0001
- P0003
- P0004
- P0008
- P000B
- P000C
- P000D
- P0010
- P0011
- P0012
- P0013
- P0014
- P0016
- P0017
- P0018
- P0019
- P0020
- P0023
- P0030
- P0031
- P0032
- P0033
- P0034
- P0035
- P0036
- P0037
- P0038
- P0045
- P0047
- P0051
- P0052
- P0053
- P0054
- P0057
- P0058
- P0060
- P0061
- P0062
- P0068
- P0069
- P006C
- P006D
- P0070
- P0071
- P0072
- P0073
- P007B
- P007C
- P007D
- P0087
- P0088
- P0089
- P009
- P0090
- P0091
- P0092
- P0096
- P0097
- P0098
- P00A1
- P00A2
- P00A3
- P00AF
- P00DF
- P00E0
- P00E1
- P00E9
- P00EA
- P00EB
- P00F3
- P00F4
- P00F5
- P00F6
- P00F8
- P00F9
- P00FA
- P00FB
- P00FD
- P0101
- P0102
- P0103
- P0105
- P0106
- P0107
- P0108
- P0109
- P0111
- P0112
- P0113
- P0114
- P0115
- P0116
- P0117
- P0118
- P0119
- P0120
- P0121
- P0122
- P0124
- P0125
- P0128
- P0129
- P012A
- P012B
- P012C
- P012F
- P0130
- P0131
- P0132
- P0133
- P0135
- P0136
- P0137
- P0138
- P0139
- P0140
- P0141
- P0151
- P0152
- P0153
- P0154
- P0155
- P0157
- P0158
- P0159
- P015E
- P015F
- P016
- P016
- P0160
- P0161
- P0165
- P016D
- P016F
- P0171
- P0172
- P0174
- P0175
- P0182
- P0183
- P018C
- P018D
- P0190
- P0191
- P0193
- P0196
- P0197
- P0198
- P0199
- P01CB
- P01CC
- P01CD
- P01CE
- P01CF
- P01D0
- P01D1
- P01D2
- P01D3
- P01D4
- P01D5
- P01D6
- P020
- P020
- P0201
- P0202
- P0203
- P0204
- P0205
- P0206
- P0207
- P0208
- P020B
- P020C
- P020D
- P020F
- P0218
- P0219
- P0221
- P0222
- P0223
- P023
- P0234
- P0235
- P0237
- P0238
- P023B
- P023C
- P0243
- P0245
- P0246
- P025
- P0251
- P0252
- P0253
- P0254
- P025B
- P025C
- P025D
- P0262
- P0263
- P0264
- P0265
- P0266
- P0267
- P0268
- P0269
- P026A
- P026C
- P026D
- P026E
- P0270
- P0271
- P0272
- P0273
- P0274
- P0275
- P0276
- P0277
- P0278
- P027A
- P027B
- P027C
- P027D
- P0298
- P0299
- P02E0
- P02E1
- P02E7
- P02E8
- P02E9
- P02EC
- P02ED
- P02FA
- P0300
- P0301
- P0302
- P0303
- P0304
- P0305
- P0306
- P0307
- P0308
- P0310
- P0315
- P0320
- P0324
- P0325
- P0326
- P0327
- P0328
- P0330
- P0335
- P0336
- P0339
- P0340
- P0341
- P0342
- P0343
- P0344
- P0345
- P0349
- P0351
- P0352
- P0353
- P0354
- P0355
- P0356
- P0357
- P0358
- P0365
- P0369
- P0390
- P0394
- P0401
- P0402
- P0403
- P0404
- P0406
- P040B
- P040C
- P040D
- P0420
- P0421
- P0426
- P0427
- P0428
- P0430
- P0431
- P0432
- P0440
- P0441
- P0442
- P0443
- P0444
- P0452
- P0455
- P0456
- P0457
- P0458
- P0459
- P0460
- P0461
- P0462
- P0463
- P0471
- P0472
- P0473
- P0480
- P0481
- P0489
- P0490
- P0498
- P0499
- P049D
- P04CE
- P04D0
- P04D1
- P04D8
- P04D9
- P04DA
- P04DB
- P04DD
- P04DE
- P050
- P0500
- P0501
- P0503
- P0504
- P0505
- P0506
- P0507
- P0508
- P0509
- P050B
- P050D
- P0513
- P0516
- P0517
- P0519
- P051B
- P051C
- P051D
- P0520
- P0521
- P0522
- P0523
- P0524
- P052F
- P0530
- P0532
- P0533
- P053A
- P053B
- P053C
- P0545
- P0546
- P054A
- P054C
- P054E
- P054F
- P0551
- P0556
- P0557
- P0558
- P0562
- P0563
- P0564
- P0571
- P0572
- P0573
- P0578
- P0579
- P0580
- P0581
- P0582
- P0585
- P0586
- P0589
- P058A
- P058B
- P058C
- P058D
- P0591
- P0592
- P0593
- P0594
- P05EC
- P05ED
- P05EE
- P05EF
- P05F0
- P05F1
- P05F3
- P05F5
- P05F8
- P060
- P060
- P0600
- P0601
- P0602
- P0604
- P0605
- P0606
- P0607
- P060B
- P060C
- P060D
- P0610
- P0611
- P0613
- P0614
- P0615
- P0616
- P061A
- P061B
- P061C
- P0622
- P0625
- P0627
- P0628
- P0629
- P062A
- P062B
- P062C
- P062D
- P062E
- P062F
- P0631
- P0632
- P0633
- P0634
- P063A
- P0641
- P0642
- P0643
- P0645
- P0646
- P0647
- P064A
- P064D
- P064F
- P0651
- P0652
- P0653
- P0658
- P0659
- P065A
- P065B
- P065C
- P0660
- P0666
- P0667
- P0668
- P0669
- P066A
- P066B
- P066C
- P066D
- P066E
- P066F
- P0670
- P0671
- P0672
- P0673
- P0674
- P0675
- P067A
- P067B
- P067C
- P067D
- P067E
- P067F
- P0683
- P0685
- P0686
- P0687
- P0688
- P068A
- P068B
- P0691
- P0693
- P0694
- P0697
- P06AB
- P06AC
- P06AD
- P06AE
- P06BA
- P06BB
- P06BC
- P06BD
- P06BE
- P06DA
- P06DD
- P06DE
- P06E9
- P06EA
- P06EB
- P06EF
- P06FE
- P0700
- P0701
- P0703
- P0705
- P0706
- P0707
- P0708
- P0710
- P0711
- P0712
- P0713
- P0714
- P0715
- P0716
- P0720
- P0721
- P0725
- P0729
- P072F
- P0730
- P0733
- P0734
- P0735
- P0736
- P073E
- P0740
- P0743
- P0746
- P0747
- P0748
- P0750
- P0751
- P0753
- P0755
- P0756
- P0760
- P0765
- P076F
- P0770
- P0776
- P0777
- P077C
- P077D
- P077E
- P0783
- P079
- P07A7
- P07B3
- P07B4
- P07B5
- P07B9
- P07BA
- P07BE
- P07BF
- P07C0
- P07D9
- P07E4
- P07F6
- P080
- P0805
- P0806
- P0807
- P0808
- P0810
- P0812
- P0814
- P081C
- P0820
- P0836
- P0838
- P0839
- P0841
- P0842
- P0843
- P0845
- P0846
- P0850
- P0864
- P0867
- P0868
- P0869
- P086A
- P086C
- P086D
- P086E
- P086F
- P0870
- P0871
- P0875
- P0876
- P0882
- P0884
- P0885
- P0887
- P0888
- P0890
- P0891
- P0893
- P0904
- P0905
- P0906
- P0907
- P0911
- P0914
- P0919
- P0928
- P0929
- P093
- P0930
- P0931
- P0932
- P0933
- P0934
- P0935
- P093B
- P093C
- P0942
- P0944
- P0951
- P0952
- P0953
- P0955
- P0960
- P0961
- P0962
- P0963
- P0964
- P0965
- P0966
- P0967
- P0968
- P0969
- P097
- P0970
- P0971
- P0972
- P0974
- P0976
- P0977
- P0978
- P0979
- P097B
- P097C
- P097D
- P0980
- P0981
- P0982
- P0983
- P0984
- P0985
- P0986
- P0987
- P0988
- P0992
- P0998
- P0999
- P099B
- P099C
- P0A1A
- P0EA7
- P1004
- P1009
- P101
- P101B
- P101C
- P102
- P1021
- P1022
- P1024
- P1025
- P1026
- P1027
- P1028
- P1029
- P102B
- P102C
- P103
- P103
- P1031
- P1032
- P1033
- P1034
- P1035
- P1036
- P1037
- P1038
- P1039
- P103B
- P103C
- P103D
- P103F
- P104
- P1040
- P1041
- P1042
- P1043
- P1044
- P1045
- P1046
- P1047
- P1049
- P104B
- P104C
- P105
- P1050
- P1051
- P1052
- P1053
- P1054
- P1055
- P1056
- P1057
- P1058
- P1059
- P105B
- P105C
- P105D
- P106
- P1061
- P1062
- P1063
- P1064
- P1065
- P1066
- P1067
- P1068
- P1069
- P106B
- P106C
- P1070
- P1072
- P1073
- P1101
- P1102
- P1115
- P112
- P1128
- P1129
- P112B
- KIA DTC
- B1101
- B1102
- B1105
- B1200
- B1201
- B1202
- B1203
- B1204
- B1205
- B1206
- B1207
- B1208
- B1209
- B1223
- B1233
- B1234
- B1237
- B1238
- B1241
- B1242
- B1245
- B1246
- B1249
- B1250
- B1260
- B1261
- B1262
- B1263
- B1270
- B1271
- B1272
- B1273
- B1274
- B1282
- B1284
- B1322
- B1324
- B1325
- B1326
- B1327
- B1328
- B1329
- B1330
- B1331
- B1332
- B1333
- B1334
- B1335
- B1338
- B1339
- B1346
- B1347
- B1348
- B1349
- B1352
- B1353
- B1354
- B1355
- B1361
- B1362
- B1363
- B1364
- B1367
- B1368
- B1369
- B1370
- B1378
- B1379
- B1380
- B1381
- B1382
- B1383
- B1384
- B1385
- B1387
- B1388
- B1389
- B1395
- B1396
- B1397
- B1398
- B1399
- B1400
- B1401
- B1402
- B1403
- B1404
- B1405
- B1406
- B1409
- B1410
- B1412
- B1413
- B1414
- B1415
- B1418
- B1419
- B1447
- B1448
- B1449
- B1473
- B1474
- B1475
- B1476
- B1477
- B1478
- B1479
- B1480
- B1481
- B1483
- B1484
- B1485
- B1486
- B1487
- B1489
- B1490
- B1493
- B1495
- B1511
- B1512
- B1513
- B1514
- B1515
- B1516
- B1517
- B1518
- B1521
- B1522
- B1523
- B1524
- B1580
- B1585
- B1586
- B1588
- B1589
- B1590
- B1591
- B1602
- B1603
- B1605
- B1606
- B1607
- B1611
- B1612
- B1613
- B1620
- B1621
- B1627
- B1628
- B1645
- B1646
- B1647
- B1650
- B1652
- B1655
- B1657
- B1658
- B1670
- B1690
- B1711
- B1712
- B1713
- B1714
- B1722
- B1723
- B1725
- B1726
- B1727
- B1728
- B1729
- B1748
- B1910
- B1911
- B1912
- B1913
- B1952
- B1954
- B1955
- B1956
- B1957
- B1958
- B2115
- B2119
- B2330
- B2332
- B2333
- B2405
- B2406
- B2408
- B2409
- B2411
- B2416
- B2420
- B2421
- B2422
- B2423
- B2424
- B2425
- B2426
- B2427
- B2429
- B2441
- B2450
- B2451
- B2452
- B2455
- B2456
- B2457
- B2500
- B2502
- B2503
- B2504
- B2508
- B2521
- B2524
- B2525
- B2529
- B2533
- B2535
- B2537
- B2539
- B2541
- B2543
- B2545
- B2547
- B2549
- B2551
- B2553
- B2555
- B2557
- B2559
- B2561
- B2563
- B2565
- B2571
- B2573
- B2575
- B2577
- B2579
- B2581
- B2583
- B2585
- B2587
- B2589
- B2598
- B2599
- B2837
- B2859
- B2860
- C1101
- C1107
- C1108
- C1112
- C1121
- C1122
- C1123
- C1124
- C1126
- C1127
- C1200
- C1201
- C1202
- C1203
- C1204
- C1205
- C1206
- C1207
- C1210
- C1211
- C1212
- C1213
- C1235
- C1236
- C1237
- C1240
- C1259
- C1260
- C1261
- C1274
- C1275
- C1278
- C1279
- C1281
- C1282
- C1283
- C1300
- C1306
- C1312
- C1313
- C1314
- C1315
- C1317
- C1318
- C1319
- C1320
- C1322
- C1323
- C1324
- C1325
- C1332
- C1333
- C1334
- C1335
- C1341
- C1342
- C1343
- C1344
- C1503
- C1513
- C1526
- C1604
- C1605
- C1611
- C1612
- C1613
- C1616
- C1623
- C1625
- C1626
- C1627
- C1647
- C1660
- C1661
- C1664
- C1665
- C1666
- C1668
- C1692
- C1693
- C1700
- C1702
- C1704
- C1705
- C2112
- C2124
- C2212
- C2227
- C2308
- C2312
- C2316
- C2320
- C2324
- C2328
- C2332
- C2336
- C2366
- C2370
- C2372
- C2374
- C2380
- C2400
- C2401
- C2402
- C2412
- C2413
- C2510
- C2511
- C2512
- C2513
- C2514
- C2515
- P0011
- P0012
- P0014
- P0016
- P0017
- P0018
- P0019
- P0021
- P0022
- P0024
- P0025
- P0026
- P0027
- P0028
- P0030
- P0031
- P0032
- P0036
- P0037
- P0038
- P0050
- P0051
- P0052
- P0056
- P0057
- P0058
- P0068
- P0075
- P0076
- P0077
- P0082
- P0083
- P0085
- P0100
- P0101
- P0102
- P0105
- P0107
- P0108
- P0111
- P0113
- P0115
- P0116
- P0117
- P0118
- P0119
- P0120
- P0121
- P0122
- P0123
- P0124
- P0128
- P0130
- P0131
- P0132
- P0133
- P0134
- P0137
- P0138
- P0139
- P0140
- P0141
- P0150
- P0151
- P0152
- P0154
- P0155
- P0156
- P0157
- P0158
- P0159
- P0160
- P0161
- P0170
- P0171
- P0172
- P0173
- P0174
- P0175
- P0181
- P0182
- P0183
- P0196
- P0197
- P0198
- P0201
- P0202
- P0203
- P0204
- P0205
- P0206
- P0217
- P0220
- P0221
- P0222
- P0223
- P0227
- P0231
- P0232
- P0262
- P0264
- P0265
- P0270
- P0271
- P0273
- P0274
- P0276
- P0277
- P0300
- P0301
- P0302
- P0303
- P0304
- P0305
- P0306
- P0315
- P0320
- P0325
- P0326
- P0327
- P0328
- P0330
- P0331
- P0335
- P0336
- P0337
- P0338
- P0339
- P0340
- P0341
- P0342
- P0343
- P0346
- P0350
- P0351
- P0352
- P0353
- P0354
- P0355
- P0356
- P0400
- P0401
- P0403
- P0420
- P0421
- P0422
- P0430
- P0431
- P0440
- P0441
- P0442
- P0443
- P0444
- P0445
- P0446
- P0447
- P0448
- P0450
- P0451
- P0453
- P0454
- P0455
- P0456
- P0459
- P0460
- P0461
- P0463
- P0464
- P0480
- P0481
- P0489
- P0490
- P0496
- P0497
- P0498
- P0499
- P0500
- P0501
- P0504
- P0506
- P0507
- P050B
- P0510
- P0532
- P0533
- P0551
- P0560
- P0561
- P0563
- P0564
- P0571
- P0600
- P0602
- P0604
- P0606
- P061B
- P0624
- P0625
- P0626
- P0630
- P0638
- P0642
- P0643
- P0645
- P0646
- P0647
- P0651
- P0652
- P0653
- P0660
- P0661
- P0662
- P0663
- P0664
- P0665
- P0685
- P0698
- P0699
- P0700
- P0703
- P0705
- P0706
- P0707
- P0708
- P0710
- P0711
- P0712
- P0713
- P0715
- P0716
- P0717
- P0720
- P0722
- P0726
- P0727
- P0731
- P0732
- P0733
- P0734
- P0735
- P0736
- P0740
- P0742
- P0743
- P0748
- P0750
- P0753
- P0755
- P0758
- P0760
- P0765
- P0768
- P0770
- P0819
- P0891
- P0995
- P1102
- P1105
- P1107
- P1111
- P1112
- P1114
- P1115
- P1117
- P1121
- P1123
- P1124
- P1127
- P1128
- P1140
- P1151
- P1159
- P1166
- P1167
- P1192
- P1193
- P1195
- P1196
- p1213
- P1215
- P1225
- P1227
- P1228
- P1229
- P1295
- P1307
- P1330
- P1345
- P1372
- P1386
- P1401
- P1402
- P1403
- P1404
- P1410
- P1412
- P1413
- P1425
- P1440
- P1446
- P1447
- P1448
- P1449
- P1450
- P1455
- P1458
- P1485
- P1486
- P1487
- P1496
- P1497
- P1498
- P1499
- P1500
- P1505
- P1506
- P1507
- P1508
- P1510
- P1511
- P1513
- P1515
- P1529
- P1550
- P1552
- P1553
- P1560
- P1586
- P1602
- P1606
- P1608
- P1610
- P1613
- P1614
- P1616
- P1617
- P161B
- P1624
- P1625
- P1631
- P1632
- P1633
- P1634
- P1640
- P1642
- P1660
- P1665
- P1673
- P1674
- P1675
- P1676
- P1677
- P1678
- P1679
- P1688
- P1690
- P1691
- P1692
- P1693
- P1694
- P1695
- P1696
- P1697
- P1698
- P1699
- P169A
- P1700
- P1716
- P1718
- P1723
- P1725
- P1727
- P1728
- P1729
- P1730
- P1731
- P1732
- P1733
- P1734
- P1735
- P1736
- P1739
- P1740
- P1741
- P1742
- P1743
- P1764
- P1765
- P1766
- P1780
- P1794
- P1795
- P1797
- P1800
- P2015
- P2096
- P2097
- P2101
- P2104
- P2105
- P2106
- P2107
- P2108
- P2110
- P2111
- P2112
- P2118
- P2119
- P2122
- P2123
- P2127
- P2128
- P2135
- P2138
- P2159
- P2173
- P2176
- P2187
- P2188
- P2189
- P2191
- P2192
- P2195
- P2196
- P2197
- P2198
- P2226
- P2227
- P2228
- P2229
- P2231
- P2232
- P2237
- P2251
- P2270
- P2271
- P2414
- P2422
- P2507
- P2610
- P2A01
- P2A03
- P2A04
- U0001
- U0100
- U0101
- U0121
- Lancia DTC
- Landrover DTC
- P0101
- P0102
- P0103
- P0116
- P0117
- P0118
- P0122
- P0123
- P0126
- P0130
- P0132
- P0133
- P0134
- P0135
- P0136
- P0137
- P0138
- P0140
- P0141
- P0150
- P0152
- P0153
- P0154
- P0155
- P0156
- P0157
- P0158
- P0160
- P0161
- P0171
- P0172
- P0174
- P0175
- P0261
- P0262
- P0264
- P0265
- P0267
- P0268
- P0270
- P0271
- P0273
- P0274
- P0276
- P0277
- P0279
- P0280
- P0282
- P0283
- P0300
- P0301
- P0302
- P0303
- P0304
- P0305
- P0306
- P0307
- P0308
- P0327
- P0328
- P0332
- P0333
- P0335
- P0336
- P0340
- P0500
- P0501
- P0505
- P0600
- P1117
- P1118
- P1129
- P1170
- P1171
- P1172
- P1173
- P1174
- P1230
- P1231
- P1232
- P1300
- P1319
- P1510
- P1513
- P1514
- P1535
- P1536
- P1537
- P1538
- P1551
- P1552
- P1553
- P1590
- P1591
- P1592
- P1663
- P1664
- P1665
- P1666
- P1667
- P1668
- P1672
- P1673
- P1674
- P1776
- Lexus DTC
- B1200
- B1204
- B1205
- B1206
- B1207
- B1210
- B1211
- B1212
- B1213
- B1214
- B1215
- B1216
- B1217
- B1247
- B1262
- B1263
- B1266
- B1267
- B1271
- B1272
- B1273
- B1278
- B1279
- B1281
- B1289
- B1291
- B1292
- B1296
- B2271
- B2275
- B2277
- B2282
- B2286
- B2412
- B2779
- B2784
- B278A
- B2790
- B2799
- B279A
- B279C
- C1300
- P0010
- P0011
- P0012
- P0013
- P0014
- P0015
- P0016
- P0017
- P0018
- P0019
- P0020
- P0021
- P0022
- P0023
- P0024
- P0025
- P0030
- P0031
- P0032
- P0036
- P0037
- P0038
- P0051
- P0052
- P0058
- P0060
- P0062
- P0068
- P0070
- P0071
- P0072
- P0073
- P0087
- P0088
- P0100
- P0101
- P0102
- P0103
- P0106
- P0107
- P0108
- P0110
- P0111
- P0112
- P0113
- P0115
- P0116
- P0117
- P0118
- P011B
- P0120
- P0121
- P0122
- P0123
- P0125
- P0128
- P0129
- P0130
- P0131
- P0132
- P0133
- P0134
- P0135
- P0136
- P0137
- P0138
- P0140
- P0141
- P0150
- P0151
- P0152
- P0153
- P0154
- P0155
- P0156
- P0157
- P0158
- P0159
- P0161
- P0165
- P0170
- P0171
- P0172
- P0174
- P0175
- P0190
- P0193
- P0196
- P0197
- P0198
- P0201
- P0202
- P0203
- P0205
- P0206
- P0207
- P0208
- P0218
- P0220
- P0221
- P0223
- P0230
- P0301
- P0302
- P0303
- P0304
- P0305
- P0306
- P0307
- P0308
- P0309
- P0310
- P0315
- P0320
- P0326
- P0327
- P0328
- P0330
- P0332
- P0333
- P0335
- P0339
- P0341
- P0342
- P0343
- P0344
- P0345
- P0346
- P0348
- P0351
- P0352
- P0353
- P0354
- P0356
- P0357
- P0358
- P0365
- P0367
- P0368
- P0385
- P0392
- P0393
- P0401
- P0403
- P0405
- P0406
- P0420
- P0430
- P0432
- P043E
- P043F
- P0440
- P0441
- P0442
- P0443
- P0450
- P0451
- P0452
- P0453
- P0455
- P0456
- P0457
- P0460
- P0461
- P0463
- P0480
- P0498
- P0499
- P050
- P0500
- P0501
- P0502
- P0503
- P0504
- P0505
- P0506
- P0508
- P0509
- P050B
- P0510
- P0511
- P0513
- P0516
- P0520
- P0521
- P0522
- P0524
- P0533
- P0560
- P0562
- P0563
- P0571
- P0573
- P0579
- P0580
- P0581
- P0582
- P0586
- P0591
- P0592
- P0594
- P060
- P060
- P0600
- P0601
- P0604
- P0605
- P0606
- P0607
- P060D
- P0617
- P0622
- P0627
- P0628
- P062D
- P0633
- P0645
- P0652
- P0653
- P0660
- P0685
- P0688
- P0700
- P0703
- P0705
- P0710
- P0711
- P0713
- P0714
- P0717
- P0724
- P0729
- P0731
- P0733
- P0734
- P0735
- P0736
- P0740
- P0741
- P0743
- P0746
- P0748
- P0750
- P0751
- P0755
- P0756
- P0758
- P0760
- P0761
- P0766
- P0773
- P0776
- P0778
- P0783
- P0791
- P0793
- P0796
- P0798
- P0841
- P0845
- P0846
- P0867
- P0868
- P0870
- P0871
- P0872
- P0873
- P0875
- P0876
- P0877
- P0878
- P0884
- P0891
- P0894
- P0897
- P0944
- P0951
- P0952
- P0953
- P0973
- P0974
- P0976
- P0977
- P0979
- P0980
- P0982
- P0983
- P0985
- P0986
- P0987
- P0988
- P0989
- P0992
- P0A94-564
- P1120
- P1133
- P1135
- P1155
- P1195
- P1197
- P1200
- P1235
- P1279
- P127B
- P1282
- P1294
- P1297
- P1315
- P1325
- P1330
- P1340
- P1390
- P1400
- P1401
- P1406
- P1410
- P1481
- P1486
- P1491
- P1492
- P1493
- P1494
- P1495
- P1496
- P1498
- P1499
- P1500
- P1511
- P1512
- P1520
- P1525
- P1566
- P1570
- P1572
- P1593
- P1594
- P1596
- P1597
- P1598
- P1599
- P1600
- P1603
- P1604
- P1605
- P1607
- P1615
- P1616
- P1617
- P1630
- P1631
- P1633
- P1652
- P1682
- P1684
- P1685
- P1686
- P1687
- P1694
- P1695
- P1696
- P1697
- P1700
- P1705
- P1715
- P1716
- P1717
- P1718
- P1739
- P1740
- P1742
- P1743
- P1744
- P1745
- P1747
- P1748
- P1749
- P1756
- P1757
- P1762
- P1763
- P1764
- P1767
- P1768
- P1775
- P1780
- P1781
- P1782
- P1784
- P1789
- P1790
- P1791
- P1792E
- P1793
- P1794
- P1795
- P1796
- P1798
- P1799
- P2074
- P2096
- P2098
- P2099
- P2102
- P2103
- P2111
- P2112
- P2118
- P2119
- P2120
- P2121
- P2122
- P2123
- P2125
- P2127
- P2135
- P2138
- P2195
- P2196
- P2197
- P2198
- P2237
- P2238
- P2239
- P2241
- P2242
- P2252
- P2253
- P2256
- P2302
- P2305
- P2311
- P2314
- P2317
- P2320
- P2323
- P2401
- P2402
- P2419
- P2420
- P2503
- P2610
- P2700
- P2701
- P2702
- P2704
- P2714
- P2716
- P2725
- U0122
- U0123
- U0126
- U0130
- U0132
- U0146-827
- U0155
- U0168
- U0235
- U1101
- → P1320
- Lincoln DTC
- B103B
- B103C
- B103D
- B106F
- B107D
- B1105
- B1111
- B111C
- B111D
- B117
- B1179
- B117B
- B117C
- B1317
- B1318
- B1342
- B153
- B1534
- B1538
- B1663
- B1665
- B1666
- B1667
- B1668
- B1669
- B1670
- B1707
- B1711
- B1715
- B1719
- B1723
- B1727
- B1731
- B1737
- B1741
- B1745
- B1952
- B1953
- B1956
- B1957
- B1960
- B1961
- B1964
- B1965
- B19A1
- B19A2
- B19A3
- B19A4
- B19A5
- B19A6
- B19A7
- B19A8
- B201
- B2019
- B2223
- B2224
- B2312
- B2314
- B2316
- B2318
- B2320
- B2322
- b2324
- B2326
- B236A
- B2420
- B2477
- B2552
- B2574
- B2575
- B2700
- B2701
- B2702
- B2703
- B2718
- B2721
- B2729
- B272A
- B272B
- B272C
- B272D
- B272E
- B272F
- B2730
- B2819
- B2903
- B2908
- B2935
- B2936
- B2937
- B2939
- B2940
- C113
- P000
- P0001
- P0003
- P0004
- P000B
- P0010
- P0011
- P0012
- P0013
- P0014
- P0015
- P0016
- P0017
- P0018
- P0019
- P0020
- P0021
- P0022
- P0023
- P0024
- P0025
- P0030
- P0034
- P0035
- P0036
- P0037
- P0038
- P0040
- P0041
- P0045
- P0050
- P0053
- P0054
- P0055
- P0056
- P0059
- P0060
- P0068
- P0071
- P0072
- P0073
- P007B
- P007C
- P007D
- P0087
- P008A
- P008B
- P0096
- P0097
- P0098
- P00AB
- P00AC
- P00AD
- P00BA
- P00BB
- P00BC
- P00BD
- P00BE
- P00BF
- P00C1
- P00C2
- P00C6
- P00CE
- P00D2
- P00DF
- P00E1
- P00E2
- P010
- P010
- P0101
- P0102
- P0103
- P0104
- P0106
- P0107
- P0108
- P010C
- P010D
- P010F
- P0111
- P0112
- P0113
- P0114
- P0116
- P0117
- P0118
- P0119
- P011E
- P0120
- P0121
- P0122
- P0123
- P0124
- P0125
- P0126
- P0127
- P0128
- P012B
- P012C
- P012D
- P012E
- P0130
- P0131
- P0132
- P0133
- P0134
- P0135
- P0136
- P0137
- P0138
- P0139
- P013A
- P013B
- P013E
- P0141
- P0144
- P0147
- P0148
- P014A
- P0150
- P0151
- P0152
- P0153
- P0154
- P0155
- P0156
- P0157
- P0158
- P0159
- P0161
- P0171
- P0172
- P0175
- P0176
- P017C
- P017D
- P017E
- P0180
- P0181
- P0182
- P0183
- P018B
- P018C
- P018D
- P0190
- P0191
- P0192
- P0193
- P0196
- P0197
- P0198
- P0201
- P0202
- P0203
- P0204
- P0205
- P0206
- P0207
- P0209
- P0210
- P0217
- P0218
- P0219
- P0222
- P0223
- P023
- P0230
- P0231
- P0232
- P0234
- P0236
- P0237
- P0238
- P023B
- P023C
- P0243
- P0244
- P0245
- P0246
- P0247
- P0248
- P0249
- P025
- P025
- P0250
- P025B
- P025C
- P025D
- P0261
- P0262
- P0264
- P0265
- P0267
- P0268
- P026A
- P0270
- P0271
- P0273
- P0274
- P0276
- P0279
- P027B
- P028
- P0280
- P0282
- P0283
- P028D
- P0297
- P0298
- P0299
- P02E
- P02EF
- P02F0
- P02F1
- P02F2
- P02F3
- P02F4
- P02F5
- P02FC
- P02FD
- P0300
- P0301
- P0302
- P0303
- P0304
- P0305
- P0306
- P0308
- P0309
- P0310
- P0313
- P0315
- P0316
- P0320
- P0322
- P0325
- P0326
- P0327
- P0328
- P032A
- P032C
- P032D
- P0330
- P0331
- P0332
- P0333
- P0335
- P0336
- P0339
- P033A
- P033C
- P033D
- P0340
- P0341
- P0344
- P0345
- P0346
- P0349
- P0350
- P0351
- P0352
- P0353
- P0354
- P0355
- P0356
- P0357
- P0358
- P0359
- P0360
- P0365
- P0369
- P0390
- P0391
- P0394
- P0400
- P0401
- P0402
- P0403
- P0405
- P0406
- P0410
- P0411
- P0412
- P0413
- P0414
- P0416
- P0417
- P041B
- P041C
- P041D
- P042E
- P042F
- P0431
- P043E
- P043F
- P0442
- P0443
- P0446
- P044C
- P0451
- P0453
- P0454
- P0455
- P0457
- P0460
- P0461
- P0462
- P0463
- P046D
- P0470
- P0471
- P0472
- P0473
- P0475
- P0476
- P0478
- P0480
- P0482
- P0483
- P0491
- P04DB
- P04EA
- P04EB
- P04ED
- P04EE
- P04EF
- P04FA
- P050
- P0500
- P0501
- P0503
- P0504
- P0505
- P0507
- P050B
- P050F
- P0511
- P0512
- P051C
- P051D
- P0528
- P052A
- P052B
- P052C
- P052D
- P0532
- P0533
- P0534
- P0537
- P0538
- P053F
- P0544
- P0546
- P054B
- P054C
- P054D
- P0552
- P0553
- P0560
- P0562
- P0565
- P0566
- P0567
- P0568
- P0569
- P0571
- P0572
- P0573
- P059F
- P05C0
- P05C8
- P05C9
- P05FF
- P060
- P0600
- P0602
- P0603
- P0604
- P0605
- P0606
- P0607
- P060B
- P060C
- P060D
- P0611
- P0613
- P061A
- P061C
- P061D
- P061E
- P0620
- P0622
- P0625
- P0626
- P0627
- P062B
- P062C
- P062F
- P0630
- P0642
- P0643
- P0645
- P064D
- P064E
- P064F
- P0652
- P0653
- P0657
- P0658
- P0659
- P065B
- P0660
- P0663
- P0667
- P0670
- P0671
- P0672
- P0673
- P0674
- P0675
- P0676
- P0677
- P0678
- P0683
- P0684
- P0685
- P0686
- P0687
- P0689
- P068A
- P0690
- P06A0
- P06A6
- P06A7
- P06A8
- P06A9
- P06B1
- P06B2
- P06B6
- P06B8
- P06D1
- P06E9
- P0701
- P0703
- P0704
- P0705
- P0706
- P0707
- P0708
- P0709
- P0710
- P0712
- P0713
- P0714
- P0715
- P0716
- P0717
- P0718
- P071A
- P071B
- P0720
- P0721
- P0722
- P0723
- P0726
- P0729
- P072C
- P072E
- P072F
- P0731
- P0732
- P0734
- P0735
- P0736
- P073A
- P073B
- P0740
- P0741
- P0742
- P0744
- P0746
- P0748
- P0750
- P0751
- P0752
- P0753
- P0755
- P0756
- P0757
- P0758
- P0760
- P0761
- P0762
- P0763
- P0767
- P0770
- P0771
- P0772
- P0773
- P0775
- P0778
- P0780
- P0781
- P0782
- P0783
- P0791
- P0794
- P0795
- P0798
- P0812
- P0813
- P0815
- P0816
- P0830
- P0833
- P0840
- P0886
- P0887
- P08A9
- P08AA
- P08B6
- P08B7
- P08B9
- P0960
- P0962
- P0963
- P0972
- P0974
- P0975
- P0976
- P0977
- P0978
- P0979
- P0980
- P0981
- P0982
- P0983
- P0984
- P0A05
- P0A06
- P0A07
- P0A08
- P0A09
- P0A0A
- P0A11
- P0A18
- P0A1A
- P0A1B
- P0A1D
- P0A23
- P0A2C
- P0A2D
- P0A2F
- P0A37
- P0A38
- P0A39
- P0A3B
- P0A3C
- P0A40
- P0A44
- P0A4C
- P0A50
- P0A5A
- P0A5B
- P0A5C
- P0A5D
- P0A5F
- P0A60
- P0A62
- P0A63
- P0A65
- P0A6F
- P0A71
- P0A72
- P0A74
- P0A75
- P0A77
- P0A78
- P0A7A
- P0A7D
- P0A90
- P0A92
- P0A94
- P0AEE
- P0AEF
- P0AF0
- P0B0D
- P0BCD
- P0BCE
- P0BCF
- P0BFD
- P0C00
- P0C03
- P0C0C
- P0C17
- P0C19
- P0C2F
- P0C39
- P0C3A
- P0C3B
- P0C3E
- P0C3F
- P0C40
- P0C51
- P0C64
- P0C65
- P0C73
- P0C79
- P0CA3
- P0D2D
- P0D32
- P0D33
- P0DFA
- P0DFC
- P0E10
- P0E31
- P0E4E
- P0E51
- P0E52
- P0E57
- P0E59
- P0E5A
- P0E5B
- P0E71
- P1000
- P1001
- P1009
- P100F
- P1011
- P1012
- P1013
- P1014
- P1015
- P1016
- P101F
- P1021
- P1022
- P1023
- P1024
- P1025
- P1026
- P103
- P1030
- P1031
- P1032
- P1033
- P1034
- P1035
- P1038
- P1039
- P103B
- P1060
- P1061
- P1100
- P1101
- P1112
- P1114
- P1115
- P1116
- P1117
- P111B
- P1120
- P1121
- P1124
- P1125
- P1127
- P1128
- P1129
- P1130
- P1131
- P1132
- P1137
- P1138
- P1145
- P115
- P1150
- P1151
- P1152
- P1156
- P1157
- P1158
- P117A
- P1183
- P1184
- P1224
- P1227
- P1228
- P1229
- P1231
- P1232
- P1233
- P1234
- P1235
- P1236
- P1237
- P1238
- P1243
- P1244
- P1245
- P1246
- P1260
- P1261
- P1262
- P1264
- P1265
- P1266
- P1267
- P1268
- P1270
- P1271
- P1272
- P1273
- P1275
- P1276
- P1277
- P1278
- P1280
- P1281
- P1282
- P1283
- P1284
- P1285
- P1288
- P1289
- P1290
- P1291
- P1292
- P1293
- P1294
- P1295
- P1296
- P1297
- P1299
- P1309
- P130D
- P1316
- P1336
- P1351
- P1352
- P1353
- P1354
- P1355
- P1356
- P1358
- P1359
- P1380
- P1381
- P1383
- P1385
- P1386
- P1388
- P1390
- P1391
- P1393
- P1395
- P1396
- P1397
- P139A
- P139B
- P1400
- P1401
- P1403
- P1405
- P1408
- P1409
- P1411
- P1413
- P1414
- P1432
- P1436
- P1437
- P1442
- P1443
- P1444
- P1445
- P144A
- P144B
- P144C
- P1450
- P1451
- P1452
- P1455
- P145E
- P1460
- P1461
- P1462
- P1463
- P1464
- P1469
- P1473
- P1474
- P1477
- P1479
- P1480
- P1483
- P1489
- P1500
- P1501
- P1502
- P1504
- P1506
- P1507
- P151
- P1512
- P1513
- P1516
- P1517
- P1518
- P1519
- P1520
- P1531
- P1536
- P1537
- P1538
- P1539
- P1548
- P1549
- P1550
- P1561
- P1572
- P1575
- P1582
- P1588
- P1595
- P160
- P1605
- P161A
- P161B
- P1625
- P1626
- P162D
- P162F
- P163
- P1633
- P1635
- P1636
- P1639
- P163F
- P164
- P164
- P1640
- P1641
- P1646
- P1647
- P164B
- P164C
- P164D
- P1650
- P1651
- P166
- P1660
- P1662
- P1674
- P1678
- P1698
- P169B
- P169C
- P1700
- P1701
- P1702
- P1703
- P1704
- P1705
- P1708
- P1709
- P1710
- P1711
- P1712
- P1713
- P1714
- P1715
- P1716
- P1717
- P1718
- P1719
- P1727
- P1728
- P1729
- P1740
- P1742
- P1744
- P1746
- P1747
- P1749
- P175
- P1751
- P1754
- P1756
- P1760
- P1761
- P1762
- P1767
- P1780
- P1783
- P1784
- P1785
- P1786
- P1787
- P1788
- P1789
- P1793
- P181F
- P187B
- P188B
- P188C
- P188D
- P1900
- P1901
- P1910
- P1920
- P1934
- P1935
- P193C
- P193D
- P193F
- P1A07
- P1A08
- P1A0A
- P1A0D
- P1A0E
- P1A0F
- P1A10
- P2004
- P2005
- P2006
- P2007
- P2008
- P2011
- P2015
- P2019
- P2020
- P2065
- P2066
- P2067
- P2068
- P2070
- P2071
- P2072
- P2075
- P2090
- P2091
- P2096
- P2097
- P2098
- P2099
- P2100
- P2101
- P2104
- P2105
- P2106
- P2109
- P2110
- P2111
- P2112
- P2118
- P2119
- P2121
- P2122
- P2123
- P2126
- P2127
- P2128
- P2131
- P2132
- P2133
- P2135
- P2138
- P2149
- P2163
- P2176
- P2183
- P2184
- P2185
- P2186
- P2195
- P2196
- P2197
- P2198
- P219A
- P219B
- P219C
- P219D
- P219E
- P219F
- P21A0
- P21A1
- P21CF
- P21D0
- P21D1
- P21D2
- P21D3
- P21D4
- P21D5
- P21D6
- P2227
- P2228
- P2230
- P2237
- P2240
- P2243
- P2247
- P2251
- P2254
- P2258
- P226D
- P2270
- P2271
- P2272
- P2273
- P2274
- P2275
- P2279
- P2282
- P2300
- P2301
- P2303
- P2304
- P2306
- P2307
- P2309
- P2310
- P2312
- P2315
- P2316
- P2401
- P2402
- P2418
- P242F
- P2448
- P2450
- P2451
- P2452
- P2453
- P2454
- P2455
- P2457
- P246C
- P24B9
- P24BA
- P24BB
- P24BC
- P24BE
- P24BF
- P24C0
- P24C1
- P2510
- P2535
- P25B0
- P25B1
- P25B3
- P25B4
- P25B5
- P25B6
- P260F
- P2610
- P2626
- P2627
- P2628
- P2629
- P2630
- P2631
- P2632
- P264F
- P26C3
- P26C4
- P2700
- P2701
- P2702
- P2704
- P2783
- P2796
- P2801
- P2802
- P2805
- P2A01
- P2AB7
- P2AB8
- P2AB9
- P2ABA
- P2ABB
- P2ABC
- P2ABD
- P2ABE
- P2BEC
- P2BED
- P2BEE
- P2BEF
- P2BF0
- P2BF1
- P2BF2
- P2BF3
- P2C27
- P2C28
- U0046
- U0100
- U0101
- U0104
- U0109
- U010F
- U0121
- U0129
- U0138
- U0140
- U0155
- U0164
- U016A
- U016C
- U0198
- U019B
- U0212
- U0235
- U0284
- U0298
- U0300
- U0401
- U0402
- U0405
- U0412
- U0415
- U0418
- U0422
- U0423
- U042E
- U0433
- U0452
- U0515
- U0606
- U101
- U1010
- U1011
- U1012
- U1013
- U101F
- U1020
- U1021
- U1037
- U1039
- U1041
- U1051
- U1071
- U1073
- U1089
- U1098
- U1130
- U1131
- U1135
- U1147
- U1243
- U1256
- U1260
- U1261
- U1262
- U1341
- U1451
- U2016
- U2050
- U2051
- U2100
- U2101
- U210B
- U210F
- U2110
- U2195
- U2200
- U2243
- U2471
- U2472
- U2473
- Mazda DTC
- B1013
- B1014
- B1016
- B1031 Odpady
- B1032
- B104
- B1046
- B1047
- B1048
- B1049
- B104B
- B104C
- B104D
- B104F
- B105
- B1050
- B1054
- B1055
- B1056
- B1057
- B1058
- B1059
- B105B
- B105F
- B106
- B106
- B106B
- B106C
- B106D
- B106F
- B1093
- B110
- B110C
- B110D
- B110F
- B1117
- B1119
- B112
- B1126
- B1127
- B1128
- B1129
- B1131
- B1132
- B1133
- B1134
- B1136
- B1137
- B1139
- B1140
- B1143
- B1144
- B1145
- B1146
- B1147
- B1155
- B1158
- B1200
- B1202
- B1204
- B1205
- B1206
- B1208
- B1231
- B1232
- B1239
- B1251
- B1253
- B1255
- B1257
- B129B
- B129C
- B129D
- B129F
- B12a
- B12A0
- B12A1
- B12A2
- B12A4
- B12A6
- B12A7
- B12A9
- B12AB
- B12AC
- B12AD
- B12AF
- B12B0
- B12B1
- B12B2
- B12B3
- B12B5
- B12B6
- B12B7
- B12B8
- B12B9
- B12BA
- B12BE
- B12BF
- B1302
- B1304
- B1311
- B1317
- B1318
- B1320
- B1322
- B1328
- B1330
- B1336
- B1342
- B1352
- B1472
- B1483
- B1484
- B1485
- B1506
- B1510
- B1520
- B1572
- B1578
- B1600
- B1601
- B1602
- B1624
- B1626
- B1676
- B1681
- B1685
- B1688
- B1696
- B1791
- B1793
- B1868
- B1869
- B1870
- B1877
- B1878
- B1879
- B1881
- B1882
- B1883
- B1884
- B1885
- B1886
- B1890
- B1916
- B1921
- B1925
- B1932
- B1933
- B1934
- B1935
- B1936
- B1992
- B1993
- B1994
- B1995
- B1996
- B1997
- B1998
- B1999
- B2008
- B2032
- B2044
- B2045
- B2047
- B2048
- B2049
- B2050
- B2051
- B2071
- B2077
- B2097
- B2100
- B2103
- B2108
- B2139
- B2143
- B2170
- B2172
- B2204
- B2212
- B2218
- B2226
- B2227
- B2229
- B2230
- B2231
- B2232
- B2233
- B2234
- B2235
- B2254
- B2274
- B2276
- B2277
- B2278
- B227B
- B2281
- B2282
- B2290
- B2384
- B2404
- B2406
- B241A
- B2425
- B2426
- B2427
- B2431
- B2477
- B2479
- B2498
- B2572
- B2574
- B2656
- B2666
- B2667
- B266A
- B266B
- B266C
- B266E
- B267A
- B267B
- B267C
- B2699
- B2700
- B2701
- B2702
- B273A
- B273B
- B2741
- B2773
- B2774
- B2775
- B2776
- B2777
- B2778
- B2779
- B2780
- B2783
- B2784
- B2794
- B2795
- B2796
- B2826
- B2844
- B2855
- B2856
- B2868
- B2869
- B2870
- B2871
- B2872
- B287A
- B2886
- B2887
- B2900
- B2909
- B2913
- B2924
- B2936
- B2937
- B2939
- B2947
- B2949
- B2950
- B2965
- B297A
- B297B
- B297C
- B297D
- B297E
- B297F
- B2982
- B298A
- B298B
- B298C
- B29B7
- B29B8
- B2A20
- B2A21
- B2A22
- B2A23
- B2A24
- B2A25
- B2A28
- B2A29
- B2A2A
- B2A2B
- B2A2C
- B2A2D
- B2A2E
- B2A2F
- B2A30
- B2A31
- B2A32
- B2A33
- B2A35
- B2A36
- B2A37
- B2A38
- B2A39
- B2A3A
- B2A4C
- B3104
- B3444
- C1095
- C1096
- C1115
- C1117
- C1118
- C1119
- C1125
- C1145
- C1155
- C1158
- C1165
- C1168
- C1175
- C1178
- C1185
- C1194
- C1198
- C1210
- C1214
- C1222
- C1234
- C1235
- C1236
- C1242
- C1246
- C1250
- C1254
- C1266
- C1277
- C1278
- C1279
- C1280
- C1281
- C1282
- C1288
- C1295
- C1307
- C1327
- C1329
- C1330
- C1331
- C1332
- C1333
- C1334
- C1335
- C1336
- C1404
- C1410
- C1440
- C1441
- C1442
- C1443
- C1444
- C1446
- C144A
- C144B
- C144C
- C144D
- C1470
- C1516
- C1517
- C1527
- C1528
- C1530
- C1531
- C1805
- C1862
- C1937
- C1941
- C1946
- C1947
- C1948
- C1950
- C1957
- C1958
- C1963
- C1981
- C1982
- C1991
- C1992
- C1996
- C2000
- C2769
- C2770
- C2777
- C2778
- C2780
- C3485
- P0010
- P0011
- P0012
- P0016
- P0018
- P0020
- P0021
- P0022
- P0030
- P0031
- P0032
- P0037
- P0038
- P0040
- P0041
- P0043
- P0044
- P0051
- P0052
- P0053
- P0054
- P0058
- P0059
- P0060
- P0068
- P0076
- P0077
- P0100
- P0101
- P0102
- P0103
- P0105
- P0106
- P0107
- P0108
- P0109
- P0110
- P0111
- P0113
- P0114
- P0115
- P0116
- P0117
- P0118
- P0119
- P0120
- P0121
- P0122
- P0123
- P0125
- P0126
- P0128
- P0130
- P0131
- P0132
- P0133
- P0134
- P0135
- P0136
- P0137
- P0139
- P013A
- P013E
- P0140
- P0141
- P0142
- P0144
- P0145
- P0146
- P0147
- P0148
- P014A
- P0150
- P0151
- P0152
- P0153
- P0154
- P0155
- P0156
- P0157
- P0158
- P0159
- P0160
- P0161
- P0170
- P0171
- P0172
- P0173
- P0174
- P0175
- P0176
- P0180
- P0181
- P0182
- P0183
- P0190
- P0191
- P0192
- P0193
- P0201
- P0203
- P0204
- P0205
- P0206
- P0217
- P0219
- P0222
- P0223
- P0230
- P0231
- P0232
- P025
- P025B
- P0261
- P0262
- P0264
- P0265
- P0267
- P0268
- P0270
- P0273
- P0274
- P0276
- P0277
- P0297
- P0298
- P02CF
- P0300
- P0301
- P0302
- P0303
- P0304
- P0305
- P0306
- P0315
- P0316
- P0320
- P0325
- P0326
- P0327
- P0328
- P0330
- P0335
- P0336
- P0339
- P0340
- P0341
- P0344
- P0345
- P0346
- P0349
- P0350
- P0351
- P0352
- P0353
- P0354
- P0355
- P0356
- P0400
- P0401
- P0402
- P0403
- P0404
- P0405
- P0406
- P0410
- P0420
- P0421
- P0430
- P0431
- P0440
- P0441
- P0442
- P0443
- P0444
- P0445
- P0446
- P0450
- P0451
- P0452
- P0453
- P0454
- P0455
- P0456
- P0457
- P0460
- P0461
- P0462
- P0463
- P0464
- P0470
- P0480
- P0481
- P050
- P050
- P0500
- P0501
- P0503
- P0504
- P0505
- P0506
- P0507
- P050B
- P0510
- P0511
- P0512
- P052B
- P0532
- P0533
- P0534
- P0535
- P0550
- P0551
- P0552
- P0553
- P0562
- P0563
- P0564
- P0571
- P0579
- P0581
- P060
- P0600
- P0601
- P0602
- P0603
- P0604
- P0606
- P0607
- P060B
- P060C
- P060D
- P0610
- P0613
- P0614
- P061A
- P061B
- P061C
- P061D
- P061F
- P0620
- P0622
- P0625
- P0626
- P0627
- P062F
- P0638
- P0642
- P0643
- P0645
- P064D
- P0657
- P065B
- P0660
- P0661
- P0662
- P0685
- P0690
- P06B8
- P0700
- P0703
- P0704
- P0705
- P0706
- P0707
- P0708
- P0710
- P0711
- P0712
- P0713
- P0714
- P0715
- P0717
- P0718
- P0720
- P0722
- P0723
- P0729
- P072C
- P072E
- P072F
- P0730
- P0731
- P0732
- P0733
- P0734
- P0735
- P073A
- P073B
- P0740
- P0741
- P0743
- P0744
- P0745
- P0748
- P0750
- P0751
- P0752
- P0753
- P0755
- P0756
- P0757
- P0758
- P0760
- P0761
- P0763
- P0765
- P0766
- P0767
- P0768
- P0770
- P0771
- P0772
- P0773
- P0774
- P0778
- P0781
- P0782
- P0783
- P0791
- P0794
- P0797
- P0812
- P0841
- P0850
- P0928
- P0930
- P0960
- P0962
- P0963
- P0964
- P0966
- P0967
- P0973
- P0974
- P0976
- P0977
- P0979
- P0980
- P0982
- P0983
- P0A00
- P0A01
- P0A02
- P0A03
- P0A05
- P0A08
- P0A09
- P0A0A
- P0A0C
- P0A0E
- P0A10
- P0A11
- P0A12
- P0A13
- P0A18
- P0A1A
- P0A1B
- P0A1F
- P0A23
- P0A27
- P0A2A
- P0A36
- P0A3B
- P0A3C
- P0A3E
- P0A44
- P0A50
- P0A78
- P0A7A
- P0A7C
- P0A7D
- P0A7E
- P0A80
- P0A81
- P0A8B
- P0A8D
- P0A8E
- P0A90
- P0A92
- P0A95
- P0A96
- P0A9B
- P0AA6
- P0AA7
- P0AAC
- P0AB1
- P0ABF
- P0AC0
- P0ADD
- P0AE1
- P1000
- P1001
- P1100
- P1101
- P1102
- P1103
- P1110
- P1112
- P1113
- P1114
- P1115
- P1116
- P1117
- P1120
- P1121
- P1122
- P1123
- P1124
- P1127
- P1129
- P1130
- P1131
- P1133
- P1134
- P1135
- P1137
- P1138
- P1141
- P1142
- P1143
- P1144
- P1145
- P115
- P1150
- P1151
- P1152
- P1157
- P1168
- P1169
- P1170
- P117A
- P1195
- P1196
- P1233
- P1236
- P1237
- P1244
- P1246
- P1251
- P1252
- P1260
- P1270
- P1285
- P1288
- P1289
- P128A
- P1290
- P1299
- P1309
- P1336
- P1351
- P1352
- P1353
- P1354
- P1358
- P1361
- P1362
- P1364
- P1365
- P1382
- P1387
- P1390
- P1397
- P1400
- P1401
- P1402
- P1405
- P1406
- P1407
- P1408
- P1409
- P1410
- P1412
- P1432
- P1443
- P1444
- P1445
- P1446
- P1449
- P144A
- P1450
- P1451
- P1455
- P1456
- P1457
- P145E
- P1460
- P1461
- P1462
- P1463
- P1464
- P1465
- P1469
- P1473
- P1474
- P1475
- P1476
- P1477
- P1479
- P1481
- P1485
- P1486
- P1487
- P1489
- P1496
- P1497
- P1498
- P1499
- P1501
- P1502
- P1504
- P1505
- P1506
- P1507
- P1509
- P1510
- P1511
- P1512
- P1516
- P1518
- P1519
- P1520
- P1521
- P1522
- P1523
- P1524
- P1525
- P1526
- P1527
- P1537
- P1538
- P1540
- P1548
- P1549
- P1550
- P1562
- P1565
- P1566
- P1567
- P1568
- P1569
- P1570
- P1572
- P1574
- P1575
- P1577
- P1600
- P1601
- P1602
- P1603
- P1604
- P1605
- P1608
- P1609
- P1621
- P1622
- P1623
- P1624
- P1627
- P1628
- P163
- P1630
- P1631
- P1632
- P1633
- P1634
- P1635
- P1636
- P1639
- P163F
- P164
- P1640
- P1641
- P1645
- P1646
- P164B
- P1650
- P1651
- P1652
- P1686
- P1687
- P1688
- P1700
- P1701
- P1702
- P1703
- P1704
- P1705
- P1707
- P1708
- P1709
- P1711
- P1713
- P1714
- P1715
- P1716
- P1717
- P1718
- P1719
- P1720
- P1721
- P1723
- P1724
- P1729
- P1735
- P1736
- P1737
- P1738
- P1740
- P1741
- P1742
- P1743
- P1744
- P1745
- P1746
- P1747
- P1748
- P1749
- P1751
- P1752
- P1754
- P1756
- P1757
- P1761
- P1762
- P1765
- P1767
- P1770
- P1771
- P1772
- P1775
- P1776
- P1777
- P1780
- P1781
- P1788
- P1789
- P1790
- P1792E
- P1793
- P1794
- P1797
- P1798
- P1799
- P1824
- P1825
- P1879
- P1900
- P1901
- P1910
- P1921E
- P1A03
- P1A04
- P1A05
- P1A06
- P1A07
- P1A08
- P1A0A
- P1A0C
- P1A0D
- P1A0E
- P1A14
- P2004
- P2006
- P2008
- P2009
- P2010
- P2014
- P2016
- P2017
- P2067
- P2068
- P2069
- P2070
- P2071
- P2072
- P2088
- P2089
- P2096
- P2097
- P2098
- P2099
- P2100
- P2102
- P2103
- P2104
- P2105
- P2106
- P2107
- P2109
- P2110
- P2111
- P2112
- P2119
- P2121
- P2122
- P2123
- P2127
- P2128
- P2131
- P2132
- P2133
- P2135
- P2136
- P2138
- P2144
- P2145
- P2178
- P2179
- P2180
- P2187
- P2188
- P2189
- P2195
- P2196
- P2197
- P2198
- P2227
- P2228
- P2257
- P2258
- P2259
- P2260
- P2270
- P2271
- P2272
- P2274
- P2275
- P2279
- P2401
- P2402
- P2404
- P2405
- P2407
- P2418
- P2450
- P2502
- P2503
- P2504
- P2507
- P2515
- P2521
- P2524
- P2531
- P2533
- P2535
- P2600
- P260F
- P2610
- P2611
- P2612
- P2613
- P2627
- P2630
- P2676
- P2677
- P2700
- P2701
- P2702
- P2703
- P2704
- P2705
- P2783
- P2800
- P2801
- P2802
- P2803
- P2805
- P2806
- U0001
- U0073
- U0100
- U0101
- U0109
- U0111
- U0114
- U0121
- U0127
- U0129
- U0131
- U0140
- U0151
- U0155
- U0159
- U0163
- U0164
- U0167
- U0184
- U0193
- U0196
- U0197
- U0214
- U0236
- U0238
- U0249
- U0255
- U0256
- U0294
- U0300
- U0302
- U0323
- U0401
- U0402
- U0414
- U0415
- U0418
- U1020
- U1039
- U1040
- U1051
- U1131
- U1147
- U1451
- U1900
- U1901
- U2012
- u2013
- U2018
- U2021
- U2023
- U2030
- U2050
- U2051
- U2064
- U210B
- U2243
- U2472
- U2473
- U2510
- U2511
- U2516
- U2527
- U2616
- U2617
- U2618
- U2619
- U261A
- Mercedes DTC
- P0010
- P0011
- P0012
- P0014
- P0015
- P0016
- P0017
- P0018
- P0019
- P0020
- P0022
- P0024
- P0025
- P0030
- P0031
- P0032
- P0036
- P0037
- P0038
- P0040
- P0041
- P0050
- P0051
- P0052
- P0056
- P0057
- P0058
- P0068
- P0071
- P0072
- P0073
- P0100
- P0101
- P0102
- P0103
- P0104
- P0106
- P0107
- P0108
- P0110
- P0111
- P0112
- P0113
- P0114
- P0115
- P0116
- P0117
- P0118
- P0119
- P0122
- P0123
- P0126
- P0128
- P0130
- P0133
- P0135
- P0136
- P0138
- P0139
- P0140
- P0141
- P0144
- P0150
- P0153
- P0155
- P0156
- P0158
- P0160
- P0161
- P0170
- P0171
- P0172
- P0173
- P0174
- P0176
- P0201
- P0203
- P0205
- P0206
- P0207
- P0219
- P0222
- P0223
- P0261
- P0262
- P0265
- P0267
- P0268
- P0270
- P0271
- P0273
- P0274
- P0276
- P0277
- P0280
- P0283
- P0300
- P0301
- P0303
- P0304
- P0305
- P0306
- P0307
- P0308
- P0324
- P0325
- P0327
- P0328
- P0330
- P0332
- P0333
- P0335
- P0336
- P0339
- P0340
- P0341
- P0342
- P0343
- P0346
- P0347
- P0350
- P0351
- P0352
- P0353
- P0354
- P0355
- P0356
- P0357
- P0358
- P0366
- P0367
- P0368
- P0370
- P0391
- P0392
- P0393
- P0410
- P0412
- P0413
- P0414
- P0415
- P0418
- P0422
- P0432
- P0440
- P0441
- P0442
- P0443
- P0444
- P0446
- P0447
- P0448
- P0450
- P0451
- P0452
- P0453
- P0455
- P0456
- P0458
- P0459
- P0460
- P0500
- P0506
- P0507
- P0513
- P0520
- P0560
- P0562
- P0563
- P0565
- P0597
- P0598
- P0599
- P0600
- P0604
- P0605
- P0606
- P0607
- P0620
- P0638
- P0642
- P0643
- P0651
- P0702
- P0706
- P0715
- P0716
- P0717
- P0718
- P0720
- P0722
- P0723
- P0726
- P0730
- P0740
- P0743
- P0748
- P0753
- P0758
- P0763
- P0778
- P0798
- P0801
- P0804
- P1031
- P1177
- P1178
- P1179
- P1185
- P1186
- P1225
- P1233
- P1357
- P1358
- P1359
- P1360
- P1366
- P1380
- P1386
- P1400
- P1420
- P1453
- P1491
- P1542
- P1550
- P1580
- P1584
- P1642
- P1644
- P1666
- P1681
- P1747
- P1999
- P2004
- P2005
- P2006
- P2009
- P2010
- P2072
- P2088
- P2089
- P2090
- P2091
- P2092
- P2093
- P2101
- P2111
- P2112
- P2122
- P2123
- P2127
- P2128
- P2135
- P2138
- P2158
- P2176
- P2195
- P2196
- P2197
- P2198
- P2227
- P2228
- P2237
- P2240
- P2243
- P2247
- P2254
- P2257
- P2258
- P2270
- P2271
- P2272
- P2273
- P2279
- P2300
- P2301
- P2304
- P2306
- P2307
- P2309
- P2310
- P2312
- P2313
- P2315
- P2316
- P2318
- P2319
- P2321
- P2322
- P2414
- P2415
- P2421
- P2422
- P2505
- P2539
- P2541
- P2542
- P2610
- P2626
- P2629
- P2716
- P2734
- P2757
- P2759
- P2766
- P2767
- P2768
- P2810
- Mercury DTC
- Mini Cooper DTC
- P0010
- P0011
- P0012
- P0013
- P0014
- P0015
- P0017
- P0030
- P0031
- P0036
- P0037
- P0038
- P0053
- P0054
- P0070
- P0100
- P0102
- P0103
- P0106
- P0107
- P0108
- P0112
- P0113
- P0114
- P0117
- P0118
- P0119
- P0122
- P0123
- P0125
- P0128
- P0130
- P0131
- P0132
- P0133
- P0135
- P0136
- P0138
- P0141
- P0153
- P0154
- P0171
- P0172
- P0201
- P0202
- P0203
- P0204
- P0218
- P0222
- P0223
- P0261
- P0262
- P0264
- P0265
- P0267
- P0268
- P0271
- P0300
- P0303
- P0313
- P0324
- P0326
- P0335
- P0336
- P0340
- P0341
- P0351
- P0352
- P0420
- P0440
- P0441
- P0442
- P0443
- P0444
- P0445
- P0455
- P0456
- P0462
- P0463
- P0500
- P0506
- P0507
- P0532
- P0533
- P0562
- P0563
- P0571
- P0600
- P0601
- P0603
- P0646
- P0647
- P0704
- P0705
- P0712
- P0713
- P1104
- P1106
- P1107
- P1108
- P1109
- P1122
- P1123
- P1125
- P1126
- P1143
- P115C
- P1222
- P1223
- P1224
- P1234
- P1236
- P1321
- P1366
- P1367
- P1436
- P1437
- P143F
- P1442
- P1443
- P1475
- P1476
- P1477
- P1481
- P1482
- P1485
- P1600
- P1607
- P1611
- P1612
- P1613
- P1615
- P1656
- P1661
- P1679
- P1680
- P1681
- P1682
- P1684
- P1686
- P1687
- P1688
- P1689
- P1691
- P1692
- P1693
- P1698
- P1699
- P1705
- P1706
- P1739
- P1741
- P1742
- P1749
- P1751
- P1752
- P2067
- P2068
- P2096
- P2097
- P2122
- P2123
- P2127
- P2128
- P2138
- P2177
- P2178
- P2270
- P2271
- P2300
- P2301
- P2303
- P2304
- P2400
- P2401
- P2402
- P2404
- P2421
- P306
- P306D
- U0001
- → P1320
- Mitsubishi DTC
- B1000
- B1001
- B1002
- B1003
- B1011
- B1012
- B1018
- B1021
- B1022
- B1031 Odpady
- B1034
- B1035
- B1041
- B1042
- B1045
- B1061
- B1065
- B1079
- B10C0
- B10C1
- B1400
- B1401
- B1404
- B1406
- B1407
- B1408
- B1409
- B1410
- B1412
- B1413
- B1414
- B1415
- B1416
- B1417
- B1418
- B1419
- B1420
- B1421
- B1422
- B1423
- B1424
- B1425
- B1426
- B1427
- B1428
- B1429
- B1430
- B1431
- B1432
- B1433
- B1434
- B1435
- B1436
- B1437
- B1438
- B1439
- B1441
- B1442
- B1443
- B1444
- B1445
- B1446
- B1447
- B1448
- B1450
- B1451
- B1452
- B1453
- B1454
- B1455
- B1457
- B1458
- B1460
- B1461
- B1462
- B1463
- B1464
- B1465
- B1466
- B1467
- B1468
- B1469
- B1470
- B1471
- B1472
- B1473
- B1474
- B1475
- B1476
- B1477
- B1478
- B1479
- B1480
- B1481
- B1482
- B1483
- B1484
- B1485
- B1486
- B1487
- B1488
- B1489
- B1490
- B1491
- B1492
- B1493
- B1494
- B1495
- B1496
- B1497
- B1499
- B1506
- B1507
- B1508
- B1509
- B1519
- B1520
- B1521
- B1522
- B1523
- B1524
- B1525
- B1526
- B1527
- B1528
- B1529
- B1530
- B1531
- B1532
- B1533
- B1534
- B1535
- B1536
- B1537
- B1539
- B1540
- B1541
- B1543
- B1545
- B1546
- B1548
- B1549
- B1552
- B1553
- B1554
- B1555
- B1557
- B1558
- B1761
- B1A08
- B1A09
- B1A0A
- B1A0B
- B1A10
- B1A11
- B1A12
- B1A13
- B1A24
- B1A25
- B1A28
- B1A35
- B1B78
- B1B79
- B1B7D
- B2101
- B2204
- B2206
- B2214
- B222C
- B223B
- B2352
- B240
- B240
- B2400
- B2401
- B2402
- B2403
- B2404
- B2405
- B2406
- B2408
- B2409
- B240B
- B240D
- B2412
- B2413
- B2415
- B2416
- C100
- C1000
- C1011
- C1014
- C1015
- C101C
- C101F
- C102
- C1020
- C1027
- C102B
- C1032
- C1042
- C1043
- C1044
- C1046
- C1047
- C1048
- C1049
- C104B
- C104F
- C1053
- C1057
- C105B
- C105F
- C1063
- C1067
- C1073
- C1200
- C1204
- C120C
- C1210
- C1219
- C123
- C123B
- C123C
- C1242
- C1608
- C2002
- C2003
- C2101
- C2104
- C2111
- C2112
- C2114
- C2115
- C2116
- C2200
- C2203
- C2204
- C2206
- P0010
- P0011
- P0012
- P0013
- P0014
- P0016
- P0017
- P0031
- P0032
- P0037
- P0038
- P0043
- P0044
- P0052
- P0057
- P0058
- P0069
- P0090
- P0096
- P0097
- P0098
- P0100
- P0101
- P0102
- P0103
- P0105
- P0106
- P0107
- P0108
- P0110
- P0111
- P0112
- P0113
- P0115
- P0116
- P0117
- P0118
- P0120
- P0121
- P0122
- P0123
- P0125
- P0128
- P0130
- P0131
- P0132
- P0134
- P0135
- P0136
- P0137
- P0138
- P0139
- P0141
- P0150
- P0151
- P0152
- P0153
- P0154
- P0155
- P0157
- P0158
- P0159
- P0160
- P0161
- P0170
- P0171
- P0172
- P0173
- P0174
- P0175
- P0181
- P0182
- P0183
- P0201
- P0202
- P0203
- P0204
- P0205
- P0206
- P0219
- P0222
- P0223
- P0234
- P0243
- P0300
- P0301
- P0302
- P0303
- P0304
- P0305
- P0306
- P0326
- P0327
- P0328
- P0335
- P0340
- P0352
- P0400
- P0401
- P0403
- P0411
- P0412
- P0420
- P0421
- P0422
- P0431
- P0440
- P0441
- P0442
- P0443
- P0446
- P0450
- P0451
- P0452
- P0455
- P0461
- P0462
- P0463
- P0489
- P0490
- P0500
- P0505
- P0506
- P0507
- P050B
- P0510
- P0513
- P0551
- P0554
- P0563
- P0600
- P0601
- P0603
- P0605
- P0606
- P0622
- P0630
- P0638
- P0642
- P0657
- P0660
- P0700
- P0701
- P0702
- P0703
- P0705
- P0710
- P0711
- P0712
- P0713
- P0715
- P0716
- P0717
- P0720
- P0725
- P0731
- P0732
- P0733
- P0734
- P0735
- P0736
- P0740
- P0741
- P0742
- P0743
- P0745
- P0746
- P0750
- P0753
- P0755
- P0760
- P0763
- P0765
- P0768
- P0773
- P0776
- P0777
- P0783
- P0816
- P0826
- P0830
- P0840
- P0841
- P0842
- P0846
- P0847
- P0868
- P0882
- P0960
- P0961
- P0962
- P0963
- P0964
- P0965
- P0967
- P0968
- P0970
- P0971
- P0973
- P0974
- P0976
- P0977
- P1020
- P1101
- P1102
- P1103
- P1104
- P1105
- P1231
- P1232
- P1233
- P1234
- P1235
- P1236
- P1237
- P1239
- P1240
- P1241
- P1242
- P1243
- P1245
- P1247
- P1294
- P1296
- P1297
- P1300
- P1390
- P1391
- P1398
- P1400
- P1443
- P1487
- P1489
- P1490
- P1492
- P1493
- P1494
- P1495
- P1496
- P1500
- P1506
- P1530
- P1590
- P1600
- P1601
- P1602
- P1610
- P1637
- P1676
- P1696
- P1697
- P1698
- P1706
- P1710
- P1715
- P1723
- P1738
- P1740
- P1745
- P1750
- P1751
- P1773
- P1777
- P1778
- P1791
- P1795
- P1802
- P1803
- P1804
- P1805
- P1806
- P1807
- P1808
- P180C
- P181
- P181B
- P181C
- P181F
- P1820
- P1821
- P1822
- P1823
- P1824
- P1826
- p1828
- P182A
- P182B
- P182C
- P182D
- P182E
- P1831
- P1832
- P1833
- P1834
- P1835
- P1836
- P183D
- P1844
- P184B
- P1852
- P1855
- P1857
- P1858
- P185D
- P1862
- P1863
- P1864
- P1866
- P1867
- P1868
- P186B
- P186C
- P186D
- P186E
- P186F
- P1870
- P1871
- P1872
- P1873
- P1874
- P1875
- P1876
- P1877
- P1878
- P1879
- P187A
- P187B
- P1880
- P1881
- P1885
- P1886
- P1887
- P1888
- P1890
- P1899
- P1902
- P198
- P198D
- P198F
- P2096
- P2097
- P2100
- P2101
- P2102
- P2103
- P2108
- P2121
- P2122
- P2123
- P2126
- P2135
- P2138
- P2173
- P2195
- P2197
- P2227
- P2228
- P2229
- P2252
- P2253
- P2263
- P2423
- P2718
- P2719
- P2721
- P2727
- P2728
- P2729
- P2730
- P2733
- P2736
- P2738
- P2739
- P2742
- P2743
- P2766
- P2809
- P2812
- P2814
- P2815
- U0001
- U0019
- u0020
- U0100
- U0141
- U0151
- U0154
- U0155
- U0168
- U0169
- U0184
- U0197
- U0401
- U0431
- U1006
- U1007
- U1073
- U1102
- U1108
- U1109
- U1110
- U1117
- U1180
- U1415
- U1417
- U1425
- U1512
- U1514
- Nissan DTC
- B1017
- B1018
- B1020
- B1021
- B1022
- B1023
- B1033
- B1034
- B1035
- B1049
- B1050
- B1051
- B1052
- B1054
- B1055
- B1056
- B1057
- B1065
- B1066
- B1067
- B1068
- B1070
- B1071
- B1072
- B1073
- B1081
- B1082
- B1083
- B1084
- B1086
- B1087
- B1088
- B1089
- B1113
- B1114
- B1115
- B1118
- B1119
- B1120
- B1129
- B1130
- B1131
- B1132
- B1134
- B1135
- B1136
- B1137
- B1145
- B1146
- B1147
- B1148
- B1150
- B1151
- B1152
- B1153
- B1177
- B1178
- B1179
- B1180
- B1193
- B1194
- B1196
- B1198
- B1199
- B1200
- B1201
- B1209
- B1210
- B1211
- B2013
- B2014
- B2099
- B210
- B210
- B2108
- B2109
- B210C
- B210D
- B210F
- B2110
- B2190
- B2191
- B2192
- B2193
- B2195
- B2205
- B2552
- B2553
- B2555
- B2556
- B2557
- B2560
- B2562
- B2563
- B2578
- B2579
- B257B
- B257C
- B2581
- B2590
- B260
- B2601
- B2602
- B2603
- B2604
- B2605
- B2606
- B2607
- B2608
- B2609
- B260B
- B260C
- B260D
- B260F
- B2612
- B2617
- B2619
- B261A
- B261E
- B2621
- B2622
- B2623
- B2630
- B2632
- B2633
- B2634
- B2635
- B2636
- B2637
- B2638
- B2639
- B263F
- B2641
- B2642
- B2643
- B2644
- B2645
- B2646
- B2648
- B2649
- B264A
- B264C
- B264D
- B264E
- B264F
- B2651
- B2652
- B2653
- B2654
- B2655
- B2656
- B26E8
- B26E9
- B26EA
- B270
- B270
- B2700
- B2701
- B2702
- B2703
- B2704
- B2705
- B2706
- B2707
- B2708
- B2709
- B270B
- B270C
- B270D
- B270F
- B2878
- C0371
- C1101
- C1102
- C1103
- C1104
- C1105
- C1106
- C1108
- C1110
- C1111
- C1113
- C1115
- C1116
- C1120
- C1121
- C1122
- C1123
- C1124
- C1125
- C1126
- C1130
- C1131
- C1132
- C1133
- C1134
- C1136
- C1140
- C1142
- C1143
- C1144
- C1145
- C1146
- C1155
- C1156
- C1160
- C1163
- C1165
- C1167
- C1170
- C1176
- C1179
- C1181
- C1184
- C1189
- C11A0
- C1231
- C1232
- C1234
- C1243
- C1244
- C1245
- C1271
- C1272
- C1273
- C1274
- C1275
- C1276
- C1277
- C1278
- C1279
- C1290
- C1300
- C1310
- C1311
- C1312
- C1313
- C1314
- C1336
- C1345
- C1346
- C1368
- C1381
- C1392
- C1601
- C1604
- C1606
- C1607
- C1608
- C1609
- C1613
- C16A0
- C16A1
- C16A2
- C1704
- C1705
- C1706
- C1707
- C1708
- C1709
- C1710
- C1711
- C1712
- C1713
- C1714
- C1715
- C1716
- C1717
- C1718
- C1719
- C1720
- C1721
- C1722
- C1723
- C1724
- C1725
- C1726
- C1727
- C1729
- C1730
- C1735
- C1801
- C1802
- C1803
- C1804
- C1805
- C1806A
- C1807
- C1808
- P0000
- P0010
- P0011
- P0012
- P0016
- P0021
- P0031
- P0032
- P0037
- P0038
- P0043
- P0044
- P0051
- P0052
- P0057
- P0058
- P0075
- P0081
- P0100
- P0101
- P0102
- P0105
- P0106
- P0107
- P0108
- P0110
- P0111
- P0112
- P0113
- P0115
- P0116
- P0118
- P011B
- P0120
- P0121
- P0122
- P0123
- P0125
- P0128
- P0130
- P0131
- P0132
- P0133
- P0134
- P0135
- P0136
- P0137
- P0138
- P0139
- P0140
- P0141
- P0143
- P0145
- P0146
- P0147
- P014C
- P014D
- P0151
- P0153
- P0154
- P0155
- P0156
- P0157
- P0158
- P0159
- P0160
- P0161
- P0171
- P0172
- P0174
- P0175
- P0180
- P0181
- P0182
- P0183
- P0196
- P0197
- P0198
- P0201
- P0203
- P0204
- P0217
- P0220
- P0221
- P0222
- P0223
- P0245
- P0299
- P0300
- P0301
- P0302
- P0303
- P0304
- P0305
- P0306
- P0307
- P0308
- P0325
- P0327
- P0328
- P0332
- P0333
- P0335
- P0340
- P0345
- P0351
- P0352
- P0354
- P0400
- P0402
- P0403
- P0405
- P0406
- P0420
- P0430
- P043E
- P043F
- P0440
- P0441
- P0442
- P0443
- P0444
- P0445
- P0446
- P0447
- P0448
- P0450
- P0451
- P0452
- P0453
- P0455
- P0456
- P0460
- P0461
- P0462
- P0463
- P0464
- P050
- P0500
- P0506
- P0507
- P050B
- P0510
- P0550
- P0560
- P0571
- P0575
- P060
- P060
- P0603
- P0604
- P0605
- P0606
- P0607
- P0615
- P0643
- P0650
- P0657
- P0700
- P0703
- P0705
- P0710
- P0715
- P0717
- P0720
- P0725
- P0730
- P0731
- P0733
- P0734
- P0735
- P0740
- P0744
- P0745
- P0746
- P0750
- P0755
- P0778
- P0826
- P0840
- P0841
- P0845
- P0868
- P0AC4
- P101D
- P102D
- P106
- P1065
- P1102
- P1105
- P1108
- P1110
- P1111
- P1121
- P1124
- P1126
- P1128
- P1130
- P1131
- P1132
- P1135
- P1136
- P1137
- P1140
- P1143
- P1144
- P1145
- P1146
- P1147
- P1148
- P1163
- P1164
- P1166
- P1167
- P1168
- P1188
- P1189
- P1195
- P1196
- P1197
- P1211
- p1212
- P1217
- P1220
- P1225
- P1229
- P1271
- P1272
- P1273
- P1274
- P1275
- P1277
- P1335
- P1336
- P1400
- P1401
- P1402
- P1421
- P1440
- P1441
- P1442
- P1443
- P1444
- P1445
- P1446
- P1447
- P1448
- P1456
- P1464
- P1490
- P1491
- P1492
- P1493
- P1551
- P1552
- P1553
- P1554
- P1564
- P1568
- P1571
- P1572
- P1574
- P1575
- P1578
- P1605
- P1611
- P1612
- P1613
- P1614
- P1615
- P1616
- P1617
- P1630
- P1631
- P1705
- P1706
- P1710
- P1715
- P1720
- P1721
- P1722
- P1723
- P1730
- P1731
- P1740
- P1745
- P1752
- P1754
- P1757
- P1759
- P1760
- P1762
- P1764
- P1767
- P1769
- P1772
- P1774
- P1775
- P1776
- P1777
- P1778
- P1800
- P1805
- P1900
- P2100
- P2101
- P2102
- P2103
- P2111
- P2112
- P2118
- P2119
- P2122
- P2123
- P2127
- P2128
- P2135
- P2138
- P2195
- P2196
- P2237
- P2238
- P2239
- P2252
- P2401
- P2402
- P2419
- P2420
- P2423
- P2610
- P2637
- P2A00
- P2A03
- P3107-214
- P3190
- P3191
- P3193
- P3226-562
- U0101
- U0129
- U0140
- U0164
- U0293
- U0400
- U0415
- U0418
- U0424
- U1000
- U1001
- U1010
- U1020
- U1021
- U1022
- U1023
- U1200
- U1201
- U1202
- U1204
- U1205
- U1206
- U1207
- U1216
- U1217
- U1218
- U1219
- U121A
- U121B
- U121C
- U121D
- U121E
- U121F
- U1220
- U1225
- U1227
- U1228
- U1229
- U122A
- U122E
- U1240
- U1243
- U1244
- U1250
- U1255
- U1258
- U1263
- U1300
- U1310
- → P1320
- Oldsmobile DTC
- Opel DTC
- Peugeot DTC
- Pontiac DTC
- Porsche DTC
- Renault DTC
- Rover DTC
- Saab DTC
- Saturn DTC
- Scion DTC
- Seat DTC
- Skoda DTC
- Smart DTC
- Ssang Yong DTC
- Subaru DTC
- B1101
- B1103
- B1104
- B1105
- B1106
- B1401
- B1402
- B1403
- B1500
- C0021
- C0022
- C0023
- C0024
- C0028
- C0029
- C0031
- C0032
- C0033
- C0035
- C0036
- C0037
- C0038
- C0039
- C0041
- C0044
- C0045
- C0047
- C0051
- C0052
- C0054
- C0056
- C0057
- C0061
- C0062
- C0063
- C0064
- C0071
- C0072
- C0073
- C0074
- C0076
- C0081
- P0011
- P0018
- P0021
- P0026
- P0028
- P0031
- P0032
- P0037
- P0038
- P0050
- P0051
- P0057
- P0058
- P0065
- P0066
- P0067
- P0076
- P0077
- P0082
- P0083
- P0101
- P0102
- P0103
- P0105
- P0106
- P0107
- P0112
- P0113
- P0115
- P0116
- P0117
- P0118
- P0120
- P0123
- P0125
- P0126
- P0128
- P0129
- P0130
- P0131
- P0132
- P0133
- P0134
- P0135
- P0136
- P0137
- P0138
- P013B
- P013F
- P0140
- P0141
- P0142
- P0145
- P0147
- P014D
- P0150
- P0151
- P0152
- P0154
- P0157
- P0158
- P0159
- P015A
- P015B
- P0160
- P0171
- P0172
- P0174
- P0181
- P0182
- P0183
- P0196
- P0197
- P0201
- P0202
- P0203
- P0204
- P0205
- P0206
- P0223
- P0230
- P0244
- P0245
- P0262
- P0264
- P0265
- P0267
- P0268
- P0270
- P0271
- P0301
- P0303
- P0304
- P0305
- P0306
- P0325
- P0327
- P0328
- P0332
- P0333
- P0335
- P0336
- P0340
- P0341
- P0345
- P0352
- P0353
- P0354
- P0356
- P0400
- P0410
- P0411
- P0413
- P0416
- P0417
- P0418
- P0420
- P0440
- P0441
- P0442
- P0443
- P0445
- P0447
- P0448
- P0451
- P0452
- P0453
- P0456
- P0458
- P0459
- P0461
- P0463
- P0464
- P0480
- P0483
- P050
- P0502
- P0506
- P0507
- P0508
- P0509
- P0512
- P0513
- P0519
- P0545
- P0558
- P0559
- P0565
- P0600
- P0604
- P0692
- P0700
- P0703
- P0705
- P0710
- P0712
- P0713
- P0716
- P0719
- P0720
- P0724
- P0725
- P0726
- P0731
- P0732
- P0733
- P0740
- P0741
- P0743
- P0748
- P0758
- P0760
- P0763
- P0851
- P0852
- P0864
- P0865
- P1086
- P1087
- P1088
- P1089
- P1090
- P1091
- P1092
- P1094
- P1095
- P1096
- P1097
- P1100
- P1101
- P1103
- P1106
- P1107
- P1108
- P1111
- P1115
- P1120
- P1122
- P1130
- P1132
- P1133
- P1134
- P1137
- P1139
- P1140
- P1141
- P1142
- P1143
- P1144
- P1146
- P1151
- P1152
- P1153
- P1154
- P1155
- P1160
- P1207
- P1208
- P1301
- P1312
- P1325
- P1400
- P1418
- P1420
- P1421
- P1423
- P1440
- P1441
- P1442
- P1443
- P1446
- P1447
- P1448
- P1449
- P1451
- P1480
- P1491
- P1493
- P1494
- P1495
- P1496
- P1497
- P1498
- P1499
- P1500
- P1502
- P1505
- P1507
- P1511
- P1512
- P1513
- P1515
- P1516
- P1518
- P1520
- P1530
- P1531
- P1532
- P1540
- P1544
- P1560
- P1570
- P1571
- P1572
- P1576
- P1577
- P1578
- P1590
- P1591
- P1594
- P1595
- P1596
- P1602
- P1698
- P1699
- P1700
- P1701
- P1703
- P1704
- P1705
- P1706
- P1710
- P1711
- P1712
- P1718
- P1720
- P1722
- P1742
- P1767
- P1769
- P1841
- P1842
- P1843
- P1875
- P2004
- P2006
- P2007
- P2009
- P2011
- P2016
- P2017
- P2021
- P2088
- P2089
- P2090
- Suzuki DTC
- Toyota DTC
- Volkswagen DTC
- Volvo DTC
- Acura DTC
- HOW TO
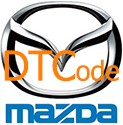
Mazda P0642
Basic DTC analysis according to OBD2 protocol standard.
OBD2 or On-Board Diagnostics displays messages for basic group styles. More comprehensible code composition has been standard since 2000. The DTC code consists of five characters and its composition will be shown in this video
Insight into programming
The basic unit for the operation of any computer is the bit. Logic 0 and 1 are expressed by a single bit. Diagnostics The error code is composed of 16 bits. The first two bits define one of the four basic circuits. The video will show you a comprehensive overview of the composition of the error report
A diagnostically understandable description of the Diagnostic Trouble Code
Mazda P0642
Basic error definition
Sensor Cluster Signal Out Of Range
Cause of DTC
Case 1 Lateral Acceleration Sensor Signal Offset The measured lateral acceleration is monitored if the vehicle is standing still (vehicle speed lt; 1.0 kph). A failure is detected if |measured lateral acceleration| gt; 0.714G is continued for 0.1sec. A failure is detected if the absolute value of the calculated lateral acceleration sensor signal offset is higher than 0.1734G for 7msec. Case 2 Lateral Acceleration Sensor Signal Plausibility Constant speed without turning driving - A failure is detected if |The difference between the reference signal and the sensor signal| gt; 0.51G is continued for 0.5sec. maneuvers with variable speed and steering - A failure is detected if |The difference between the reference signal and the sensor signal| gt; 1.12G is continued for 1.75sec. Case 3 Yaw Rate Sensor Signal Offset The measured yaw rate sensor signal is monitored when the vehicle is standing still. A failure is detected if the absolute value of the yaw rate sensor signal is continuously higher than 20° s longer than 0.1sec or higher than 10° s during the last 5.0s before vehicle drive-off. A failure is detected during vehicle drive-off if the difference between the measured yaw rate sensor signal and the latched signal value during vehicle stand-still is higher than 13° s. A failure is detected if the absolute value of the calculated yaw rate sensor offset is higher than 6° s for 7msec. Case 4 Yaw Rate Sensor Signal Plausibility Constant speed without turning driving - A failure is detected if |The gradient of the measured sensor signal| gt; 540° s and |The difference between the reference signal and the sensor signal| gt; 10° s are continued for 0.25sec. - A failure is detected if |The gradient of the measured sensor signal| lt; 540° s and |The difference between the reference signal and the sensor signal| gt; 10° s are continued for 0.5sec. Fixed radius constant speed driving - A failure is detected if |The gradient of the measured sensor signal| gt; 540° s and |The difference between the reference signal and the sensor signal| gt; 13° s are continued for 0.25sec. - A failure is detected if |The gradient of the measured sensor signal| lt; 540° s and |The difference between the reference signal and the sensor signal| gt; 13° s are continued for 0.5sec. Maneuvers with variable speed and steering - A failure is detected if |The gradient of the measured sensor signal| gt; 540° s and |The difference between the reference signal and the sensor signal| gt; 53° s are continued for 0.25sec. - A failure is detected if |The gradient of the measured sensor signal| lt; 540° s and |The difference between the reference signal and the sensor signal| gt; 53° s are continued for 1.75sec.